Selecting the appropriate type of washer is crucial in any assembly or mechanical configuration. Among the many types available,
spring washers and flat washers often lead the pack, praised for their reliability and functional efficacy. This article delves into the nuanced differences and applications of these two types of washers, drawing from authentic experiences and expert insights to guide buyers and engineers in making informed decisions.
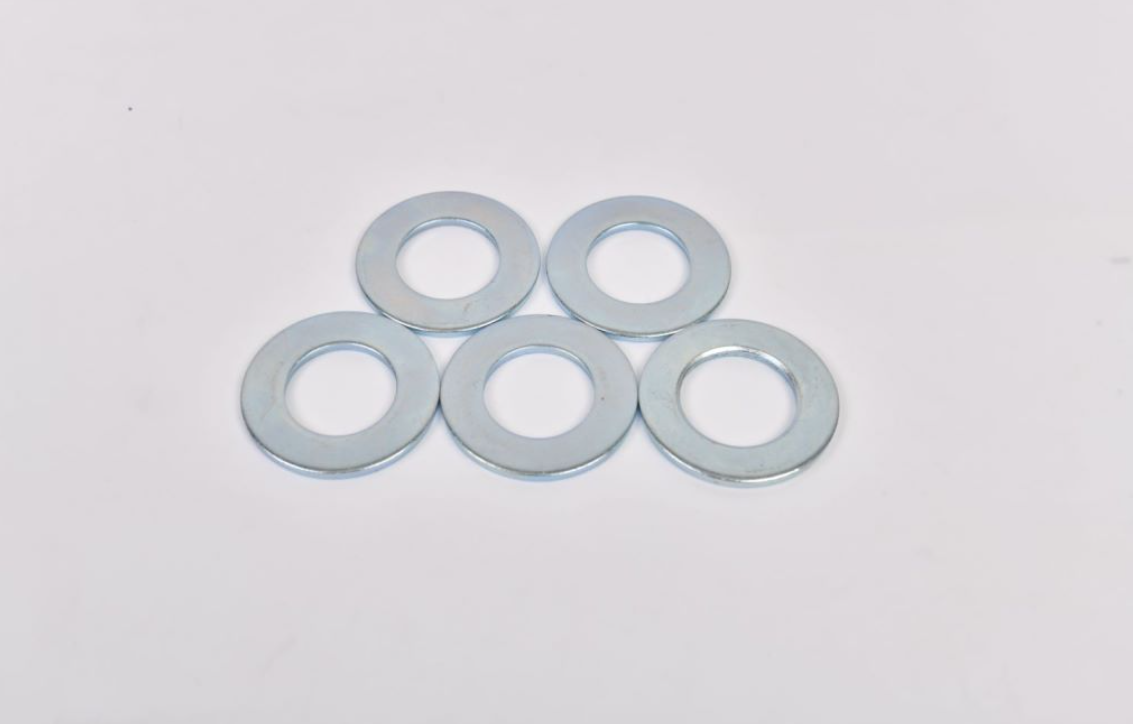
Spring washers, sometimes referred to as split washers or lock washers, are designed to provide a locking function to fasteners. Their shape—typically a ring split at one point and bent into a helical shape—creates tension between the head of a fastener and the substrate it secures. This tension gives spring washers their unique ability to maintain the necessary pre-load on a bolted joint despite vibrations or torque. Real-world applications of spring washers abound Think of automotive assemblies where engine vibrations are ever-present or in heavy machinery that operates under conditions of constant motion. By imparting a uniform spring force, these washers minimize the risk of loose bolts, which cumulatively could lead to equipment failure.
Flat washers, on the other hand, serve a more straightforward function but are no less essential. They primarily distribute the load of a threaded fastener, like a screw or nut, over a larger area. This distribution reduces the surface damage to the materials being joined and allows for a more secure fastening. Flat washers also provide a smooth surface for the nut or bolt to meet, which is critical in ensuring that torque is applied evenly and effectively. This makes flat washers indispensable in applications ranging from electronic enclosures, where sensitive components could be easily damaged, to large-scale construction projects, where durability and resilience are of utmost importance.
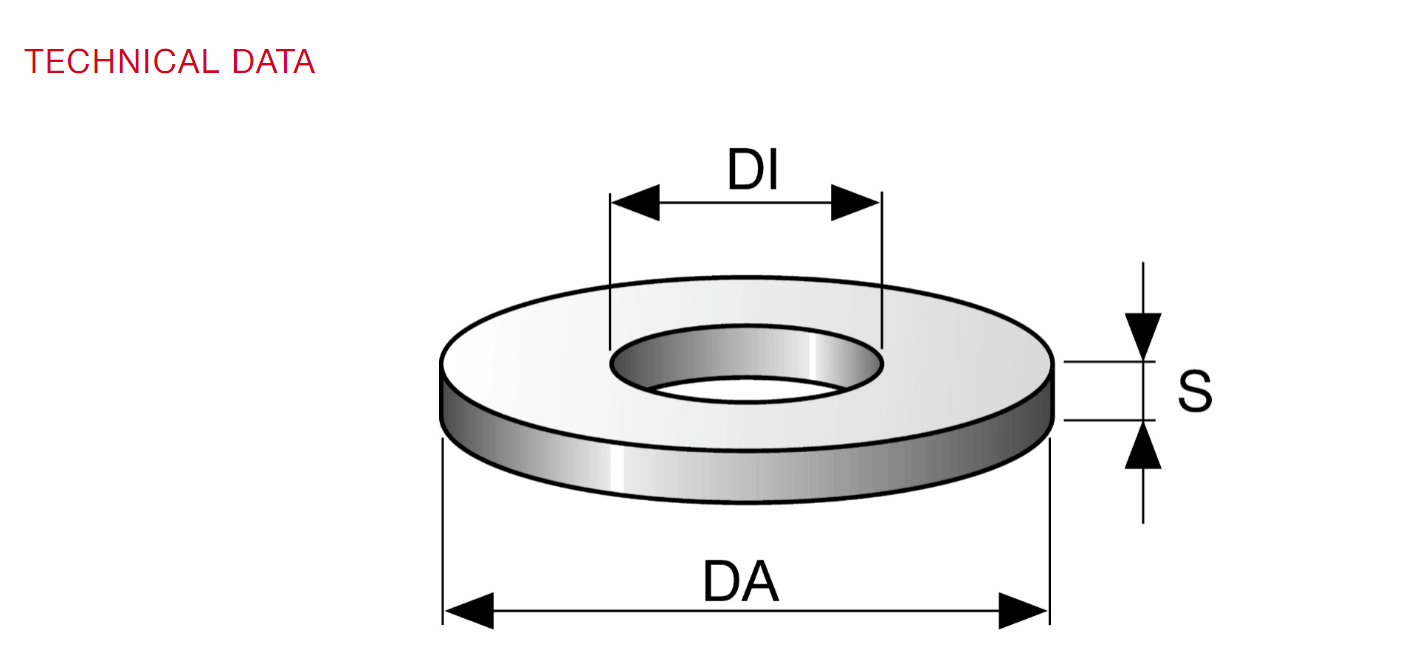
While both spring washers and flat washers are pivotal in securing fasteners, their combined use in certain scenarios can maximize safety and efficiency. A layered approach using a flat washer to spread the load and a spring washer to maintain tension can be particularly effective in high-vibration environments. This strategy has been employed in industries such as aerospace engineering, where even minor equipment failures can have catastrophic consequences. Extensive testing and trials underscore the efficacy of this combination, leading to broad acceptance among industry professionals.
spring washer and flat washer
When choosing between spring washers and flat washers, or deciding to use both, it's essential to consider the specific demands of the intended application. Factors such as environmental conditions, the nature of the materials being fastened, and the mechanical load must be considered. Corrosion resistance, for instance, can significantly impact material selection; stainless steel washers may be preferred in marine applications due to their ability to withstand saline conditions.
For industry professionals seeking to procure these components, understanding the legal and industry standards that govern washer production is crucial. International standards, such as those from the International Organization for Standardization (ISO) or the American Society for Testing and Materials (ASTM), provide guidelines on material composition, manufacturing processes, and performance metrics. Adherence to these standards ensures that washers perform as expected under specified conditions, maintaining both safety and compliance.
It's also important for buyers to engage with reputable suppliers who can provide comprehensive documentation and quality assurance certificates. Trustworthiness in the supply chain is vital, not just for meeting regulatory needs but also for ensuring the longevity and reliability of the final product. This highlights the importance of establishing partnerships with manufacturers or distributors known for their expertise and commitment to quality.
In conclusion, both spring washers and flat washers play indispensable roles across various industries due to their unique properties and practicality. By understanding their specific functions, potential applications, and relevant industry standards, engineers and procurement specialists can make decisions that boost performance and ensure safety. Whether used separately or together, these small yet powerful components underpin the integrity of countless machines and structures worldwide.