A spring washer and a flat washer are essential components in the vast realm of fastening systems, each playing a unique role in ensuring structural integrity and reliability. Understanding their differences, applications, and the nuances of ordering these components can greatly enhance any construction or manufacturing process.
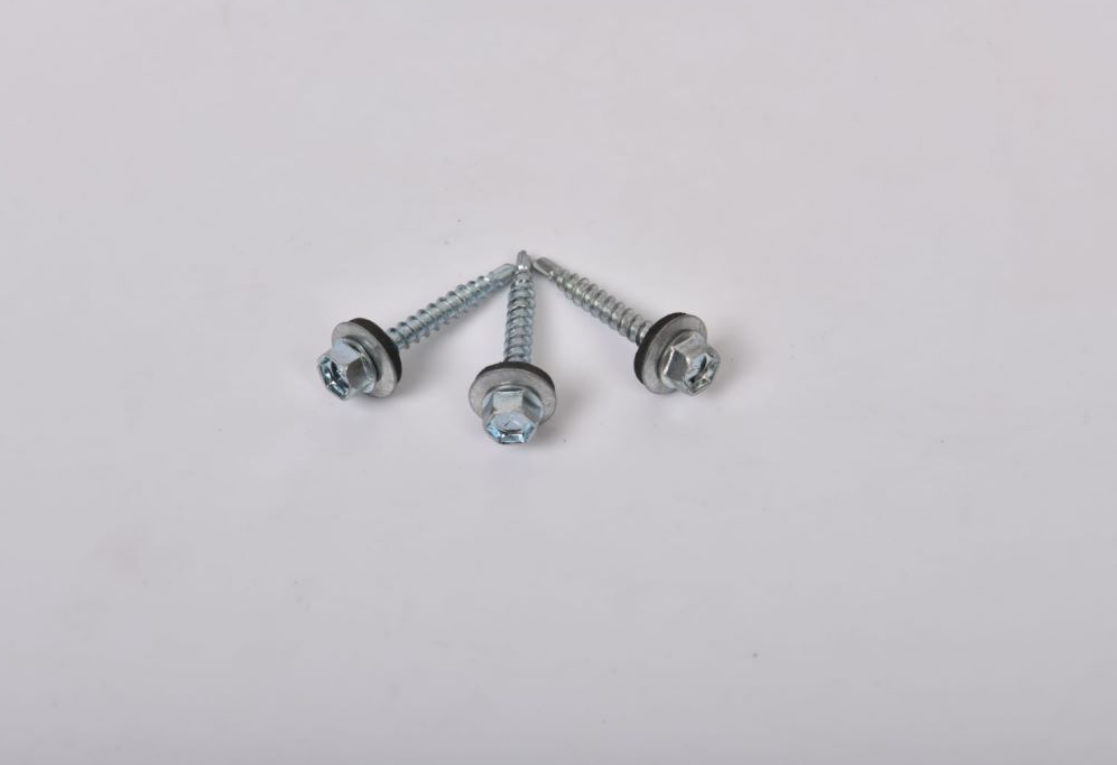
The Role of Spring Washers
Spring washers are designed to provide a preload between the bolt and the substrate, ensuring that vibrations or dynamic loads do not lead to a loosening of the fastener. These washers are typically employed in situations where minor tightening is required due to movement or vibration. Their distinctive ‘spring-like’ design allows them to compress and expand slightly, maintaining tension on the bolted joint. This characteristic makes them indispensable in automotive, aerospace, and heavy machinery industries, where maintaining joint integrity under stress is paramount.
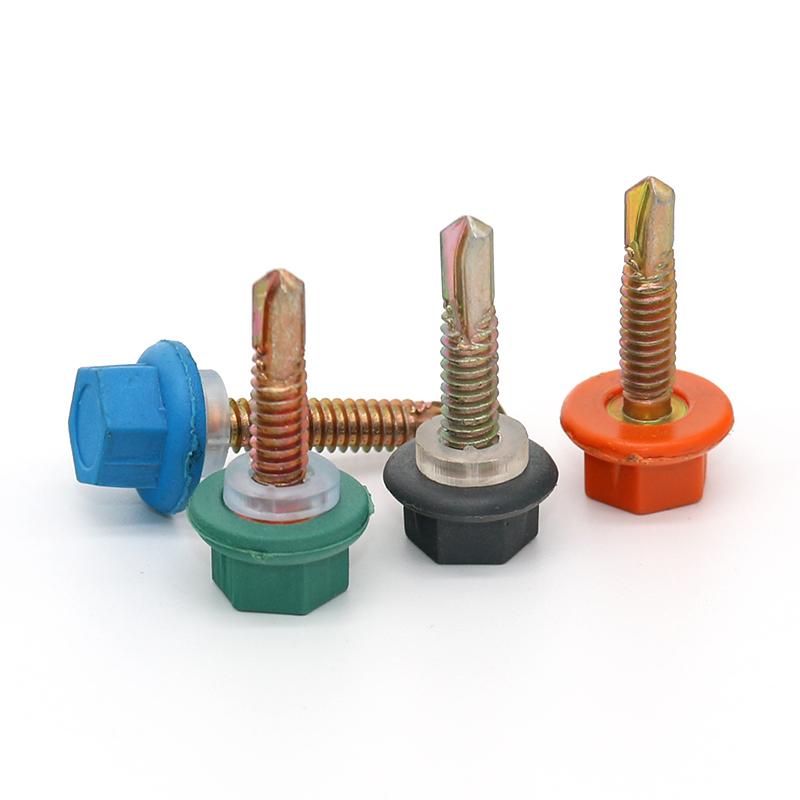
Understanding Flat Washers
Flat washers, on the other hand, serve a different purpose. These washers distribute the load of the threaded fastener, like a screw or a nut, reducing surface wear and avoiding indentation in the material being fastened. Flattened and smooth, they create a large surface area that protects the substrate by providing a barrier. This is especially important where the materials might be soft, such as aluminum or wood, and are susceptible to damage. Their use is prevalent in woodworking, plumbing, and aerospace applications where safeguarding surfaces from paint or surface coating damages is critical.
Expertise in Selection and Application
Selecting between a spring washer and a flat washer hinges on understanding application requirements. If repeated cyclic loads or thermal expansion is a factor, a spring washer may be preferable. Conversely, if the goal is to protect the surface or stabilize a fastening assembly, flat washers provide a simpler solution. Experts recommend consulting with professionals or engineers who specialize in material sciences and mechanical applications to ensure the specific washer type selected enhances rather than hinders the overall functionality and longevity of the assembly.
Insights into Ordering and Quality Considerations
spring washer and flat washer order
When ordering spring and flat washers, attention must be paid to material choice because it impacts washer efficiency.
Spring washers typically come in carbon steel, stainless steel, or phosphor bronze. The choice of material influences resistance to corrosion, fatigue, and wear. Stainless steel is favored for its anti-corrosive properties, while carbon steel provides exceptional tensile strength at a lower price. Phosphor bronze is excellent for electrical conductivity and is often used in electronics.
Flat washers are often made from similar materials, and selecting the right one can prevent galvanic corrosion. It is essential to match washer material with the bolt or fastener material where possible. When ordering, dimensions such as the inner and outer diameter and thickness must be precise to guarantee a snug fit.
Ensuring Authoritativeness and Trustworthiness
Ordering these washers from reputable manufacturers or distributors ensures that the components meet industry safety and quality standards. Look for companies that certify their products against ISO or ASME standards to guarantee material quality and performance reliability. Trustworthy suppliers often provide detailed product data sheets, certifications, and professional advice on application best practices.
Harnessing the Full Potential of Washers
For those eager to leverage the full potential of both spring and flat washers, integrating them appropriately into your assembly can enhance operational security. In complex assemblies, employing both types of washers might be necessary to achieve specific performance characteristics, tailored to the demands of the operational environment.
Investing time in understanding the small mechanical components like washers can significantly impact the overall efficiency and safety of mechanical assemblies. It reinforces the notion that even the simplest components are vital, adding layers of security and function that are indispensable in modern-day engineering and manufacturing practices. As your journey into the selection and utilization of washers progresses, always prioritize quality and application-appropriate solutions to ensure successful project outcomes.