Selecting the appropriate self-tapping screw sizes is crucial for ensuring the durability and reliability of your construction or DIY project. These screws are designed to tap their own holes as they are driven into materials like metal, wood, or plastic. Understanding the nuances of self-tapping screw sizes involves an intersection of technical knowledge, practical experience, and a keen eye for detail.
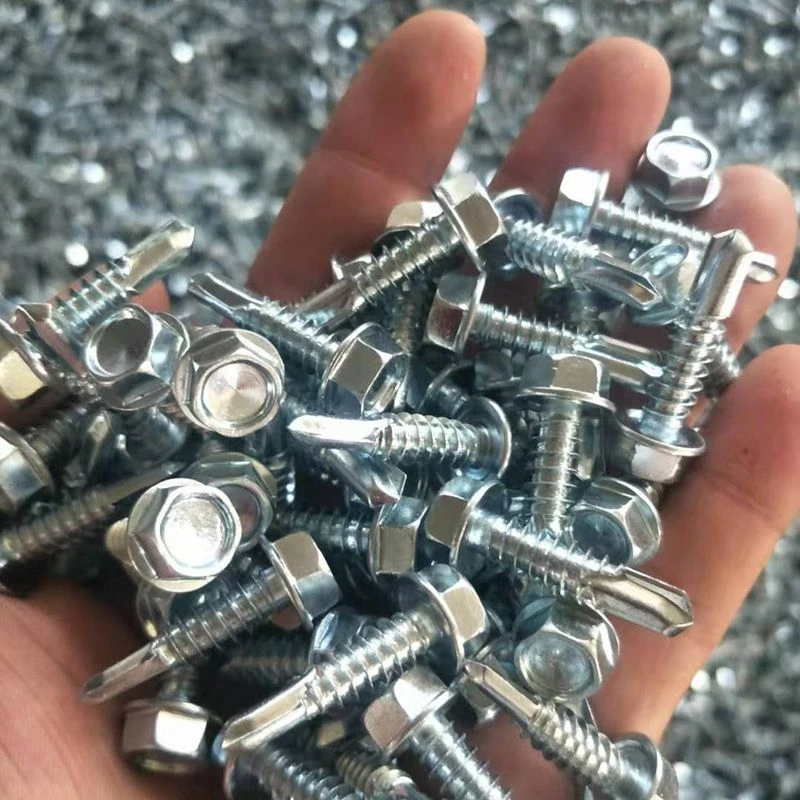
When assessing self-tapping screw sizes, the first consideration should be the application. Are you fastening into metal, wood, or plastic? Each material requires a specific screw type to optimize the grip and avoid damage. For instance, metal applications often require screws with a finer thread pitch to reduce stress on the surrounding materials, whereas wood screws typically possess a coarser thread for better grip.
The length of the screw is another critical element. Length must be matched carefully to the thickness of the materials being joined. A screw too short might not secure the materials sufficiently, leading to weak joints that could fail under stress. Conversely, an overly long screw can protrude through the material or damage hidden structures. As a rule of thumb, in wood projects, the screw should penetrate at least half of the bottom layering material.
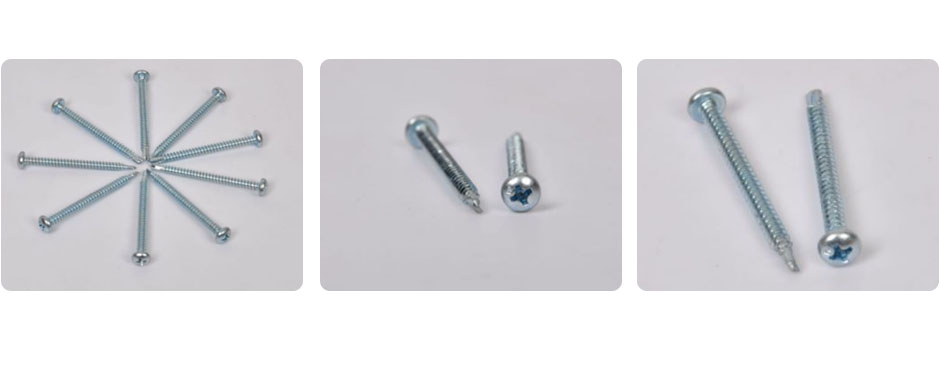
Diameter, or the screw gauge, is equally important. It is expressed in numbers; a higher gauge signifies a thicker screw, which can handle more load. However, the chosen diameter should balance strength and the risk of splitting the material. For example, a 8 screw, common in many applications, offers a good balance for general purposes, but more delicate projects might require a 6 to avoid splitting finer materials.
self tapping screw sizes
Further adding to the complexity is the head design, which plays a vital role in both the functional and aesthetic outcomes of the fastening process. Options such as pan head, flat head, and round head each serve distinct purposes. A flat head screw can be countersunk into the material for a flush finish, which is beneficial in creating smooth surfaces free from protrusions. Conversely, a round or pan head may be preferred when the appearance of the screw head is part of the design or when the material isn’t suitable for countersinking.
Proper selection of self-tapping screws also necessitates expertise in the material’s load requirements and environmental conditions. Corrosive environments demand screws made from stainless steel or specially coated to withstand rust and corrosion over time. Experience reveals that matching screw composition to the environmental conditions ensures longevity and optimal performance of the fastened components.
Trustworthiness of self-tapping screw selections can be fostered by consulting official industry guidelines and resources such as manufacturer specifications and construction codes. These references offer authoritative information that sets a standard for selection based on empirical research and historical data.
Ultimately, expertise in choosing the right self-tapping screw sizes elevates the craftsmanship of the project, enhancing structural integrity and aesthetic appeal. By combining technical insights with practical experience, one can reliably select screws that adequately meet the demands of specific applications, thus gaining the confidence of stakeholders and peers alike in the quality and durability of one's work.