Choosing between a fender washer and a flat washer might seem like a minor decision in a larger project, but it can significantly impact the durability and effectiveness of your work. Each type of washer has distinct characteristics that make it suitable for specific applications. Understanding these differences ensures that you make informed choices, enhancing the quality and longevity of your construction, automotive, or DIY projects.
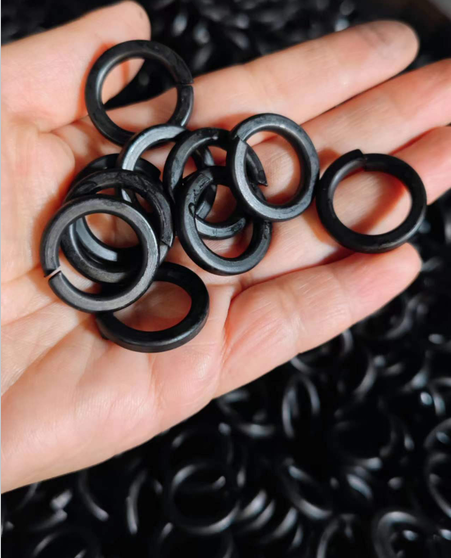
Fender washers are characterized by a larger outer diameter compared to their inner hole size. This design is specifically engineered to distribute load over a larger surface area. In practical use, fender washers are incredibly advantageous when working with soft materials or oversized holes, where there's a risk of material deformation or pull-through. For instance, in automotive bodywork or when securing thin metal sheets, fender washers provide the necessary support and stability. Their broad surface area prevents the fastener from sinking into or tearing the material, which could otherwise lead to premature structural failure.
On the other hand, flat washers are more universally used for their simplicity and wide availability. They primarily serve to increase the size of a screw or bolt's bearing surface, offering improved load distribution. This feature is critical in scenarios where even load distribution can prevent damage to the installation surface. In environments requiring a tight seal between the fastener and the surface, flat washers are preferred due to their uniform thickness and compatibility with a broad spectrum of fastener types.
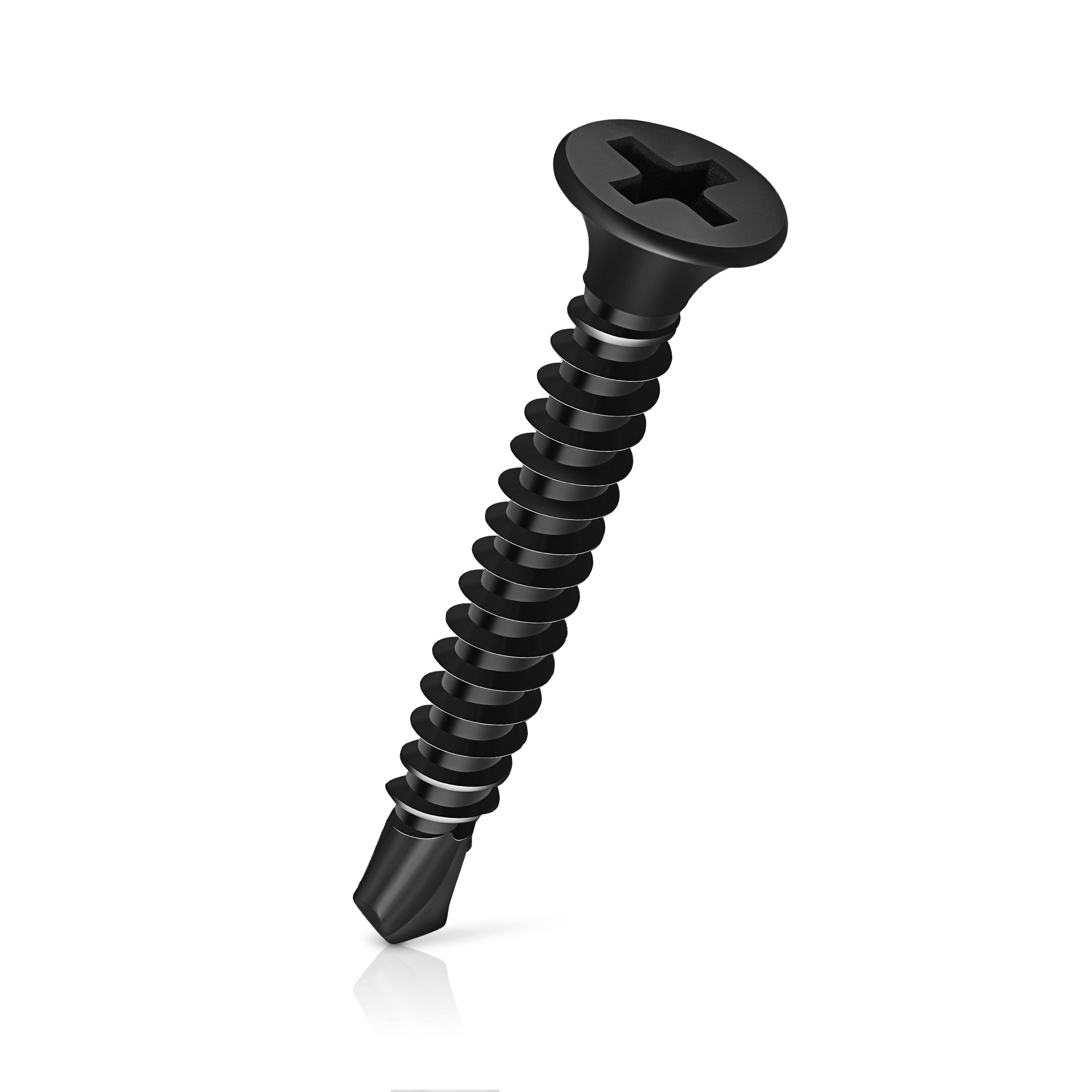
When approaching projects involving variable or extreme conditions, such as outdoor constructions or machine assemblies, the choice between a fender washer and a flat washer must be made with consideration. Fender washers excel in providing extra stability in environments where materials experience significant stress or pressure. In contrast, flat washers offer versatility and are cost-effective for general-purpose applications where load distribution and protection against surface damage are the primary concerns.
fender washer vs flat washer
For professionals seeking to enhance their work's credibility and effectiveness, leaning on industry standards and technical specifications can be beneficial. A project requiring precise load distribution may benefit from consulting engineering guidelines, which often specify when to use each washer type. These documents lend authority and trustworthiness to your work, ensuring each component functions optimally and extend the project's lifecycle.
Choosing the appropriate washer type involves not just evaluating the immediate application but also considering future implications. The misuse of washers might lead to unexpected maintenance issues or structural failures, undermining the trust in professional work. Therefore, adhering to best practices and informed selections demonstrates professionalism and expertise.
Always consider manufacturers that adhere to ISO standards, as they guarantee product reliability and consistency. Moreover, engaging with industry forums and professional workshops can provide insights into modern trends and innovations within the field, keeping you at the forefront of technical knowledge and application. This commitment not only boosts personal expertise but also ensures that clients receive high-quality, reliable results, reinforcing trust and authority in your professional brand.
In conclusion, the nuanced choice between fender washers and flat washers could define the integrity and success of a project, reflecting the professional's attention to detail and commitment to excellence. Understanding their unique benefits and applications will guide you to make decisions that uphold the values of quality and reliability in all undertakings.