When selecting a reliable fastener component, finger spring washers provide a unique combination of stability and flexibility, integral to numerous engineering applications. These washers are not mere components; they are the keystones in ensuring the longevity and efficiency of automotive, aerospace, and industrial machinery. With years of experience in the fastener industry, understanding the multi-faceted advantages of finger spring washers can significantly improve machinery performance and reliability.

Finger spring washers are crafted to provide axial preload and adaptive elasticity. This unique design enables effective load distribution, which is crucial in preventing loosening due to vibrations or dynamic loads. The finger-like projections act like miniature springs, absorbing shocks and maintaining consistent tension, ensuring fasteners remain tight even in high-stress environments. This dynamic load management reduces the risk of mechanical failure, making these washers essential in critical applications.
The expertise in deploying finger spring washers lies in selecting the appropriate material and design to match the specific demands of your application. These washers are typically made from high-grade stainless steel, carbon steel, or specialized alloys, offering exceptional resistance to corrosion and wear. Choosing the right material ensures that the washer can handle extreme temperatures and environmental conditions, enhancing the machinery's overall lifespan.
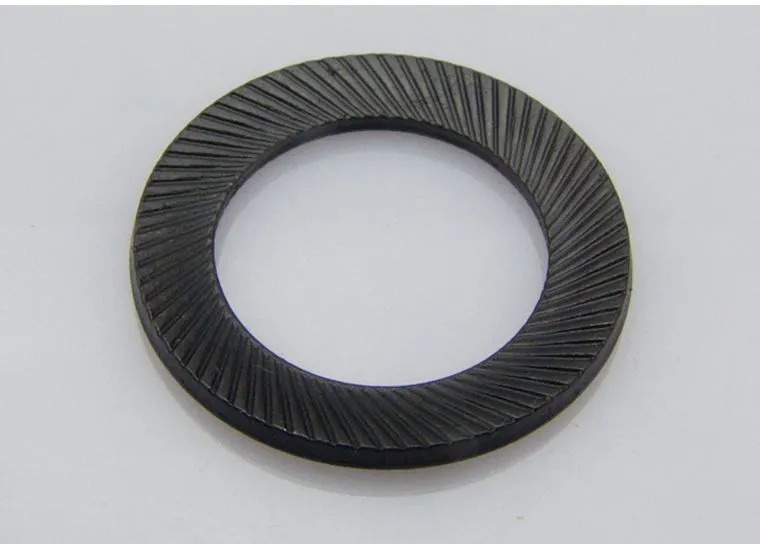
In terms of authoritativeness, finger spring washers are often recommended by industry leaders to address issues related to joint integrity and connection stability. Their application is essential in sectors where mechanical reliability cannot be compromised. For instance, in the aerospace industry, where safety and precision are paramount, finger spring washers play a vital role in maintaining structural integrity under various stress conditions. Their ability to maintain consistent tension without degrading under extreme conditions marks them as necessary components in safety-critical applications.
finger spring washer
Trustworthiness in the use of finger spring washers is further enhanced by rigorous testing and adherence to international standards. When these washers are manufactured, they undergo thorough quality assurance processes, ensuring that each unit meets stringent performance criteria. This reliability underlines their widespread acceptance across industries requiring high reliability and performance.
Real-world experience highlights the versatility of finger spring washers. In automotive applications, they are often used in brake systems, transmission assemblies, and suspension components, where they minimize noise, manage dynamic load, and maintain bolt tension despite intensive vibrations and mechanical stress. By deploying finger spring washers, engineers can effectively reduce maintenance costs and extend service intervals, highlights that resonate with businesses seeking cost-effective and durable solutions.
Furthermore, a well-optimized SEO strategy will include comprehensive guides on installation practices, industry-specific applications, and comparison with other fasteners. Providing detailed images, diagrams, and videos can also enhance user engagement, offering a more profound understanding of these components while improving search engine rankings.
In conclusion, finger spring washers, through their design efficacy, material selection, and industry validation, stand as indispensable elements in modern engineering. Their role extends beyond simple washers to components that promise to bolster efficiency and resilience in machinery. For engineers, manufacturers, and businesses keen on maximizing machinery performance and minimizing risks, understanding the application and advantages of finger spring washers is both a technical and strategic asset.