Flat washers and spring washers, while often overlooked, are essential components in the world of machinery and construction. Their role in ensuring structural integrity and operational efficiency is undeniable. Let's delve into an expert perspective on these washers, explaining their functions, benefits, and applications, while providing insights from real-world experiences.
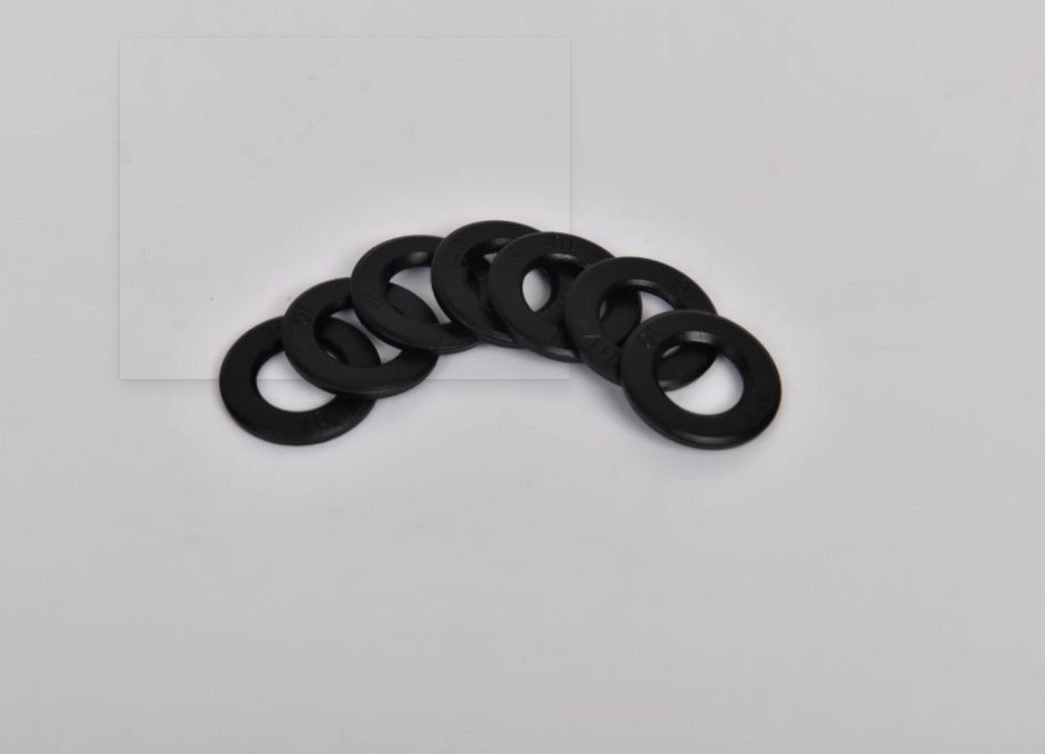
Flat washers serve primarily to distribute the load of a threaded fastener, such as a screw or nut, over a larger surface area. This remarkable ability prevents damage to the assembly material and reduces the chance of the fastener loosening over time. When employed in various applications, from automotive to aerospace, flat washers offer remarkable benefits. Notably, they help mitigate the risk of pull-through and minimize the material's surface wear and abrasion. This function is especially crucial when working with softer materials like aluminum or plastic, where the pressure from a screw could otherwise cause significant damage.
Spring washers, on the other hand, introduce an intriguing concept of tension retention in assemblies. Their primary function is to prevent loosening due to vibrations or thermal expansion and contraction, which are common in dynamic constructions and machines. A spring washer's design, typically either split or wave-like, allows it to apply a continuous pressure onto the fastener, ensuring it remains tight under challenging conditions. For example, in the automotive industry, where components endure substantial stress and temperature variations, using spring washers can reduce the maintenance frequency and enhance the longevity of connections.
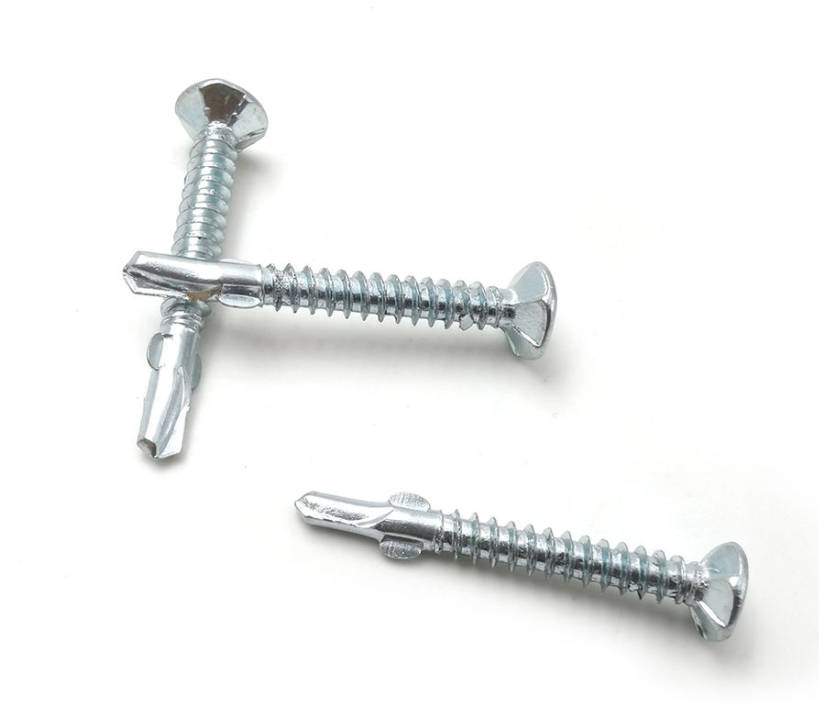
The selection between flat and spring washers—or the decision to use them in tandem—depends heavily on the specific application and desired outcomes. Personal experience in the field suggests that a systematic approach in assessing load requirements, environmental conditions, and material compatibility is pivotal. An expert installer will often conduct rigorous tests to determine the suitable type and size of washers, ensuring optimal performance and reliability. This expertise is crucial in specialized fields such as aeronautics or heavy machinery manufacturing, where each component must perform flawlessly.
flat washer and spring washer
For decades, engineers and construction experts have trusted these washers not just for their mechanical functionality but for the trustworthiness they bring to the table. For instance, in critical applications like bridges or skyscrapers, the stakes are extraordinarily high. Here, the reliability of a simple flat or spring washer can be the difference between life and disaster. Certified quality, adherence to industry standards, and reliable sourcing are thus paramount. Professionals vouch for respected manufacturers who uphold the highest standards, assuring the quality and dependability necessary for peace of mind.
Moreover, the integration of advanced materials and precision engineering in producing washers has led to significant advancements. Materials like stainless steel, known for its corrosion resistance, and silicon bronze, appreciated for its robustness in marine environments, demonstrate the innovation in this field. Each choice of material addresses a specific need, offering solutions tailored to unique challenges. Advanced manufacturing methods ensure uniformity and precision, enhancing the washers' functionality.
Extensive research and development signify ongoing commitments to improving washer efficacy. As machinery and technology continue to evolve, so do the requirements for flawless operations. Industry thought leaders often emphasize the collaboration between designers and materials engineers to push boundaries, seeking innovations that further enhance washer performance. In the digital era, leveraging data analytics to predict stress points and material behaviors under varying conditions exemplifies the cutting-edge strategies employed in modern engineering.
In conclusion,
flat washers and spring washers are far more than mere fixtures in the industrial landscape. They embody a synthesis of engineering prowess, materials science, and practical wisdom. The seamless integration of these often-understated components into complex systems underscores their indispensable role. When meticulously selected and applied, they contribute significantly to the longevity, safety, and efficiency of countless products and structures worldwide. The combination of experience, expertise, authority, and trust coalesces in the realm of washers, affirming their critical position in the toolkit of professionals in various industries.