Single coil spring washers, also known as single coil lock washers, are an integral component in bolted assemblies where vibration-induced loosening is a concern. Originating from a simple yet highly effective design, they feature a helical shape that exerts a spring force upon installation. This force increases friction between the bolt thread and nut or tapped hole, providing resistance against rotations that could cause the assembly to loosen over time.
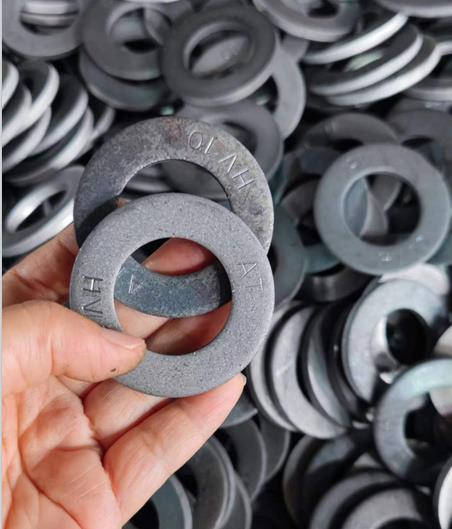
One of the most notable applications of single coil spring washers is in the automotive industry. Vehicles regularly encounter conditions that generate significant vibrational forces; hence, maintaining the tightness of critical components is paramount for safety and reliability. Experienced automotive engineers rely on these washers in diverse assemblies, from securing engine components to fastening elements within the suspension system, ensuring both enhanced performance and longevity of the vehicle.
In addition to automotive uses, single coil spring washers are also crucial in aerospace applications where precision and reliability are of utmost importance. Aerospace engineers often face challenges related to substantial temperature fluctuations and intense vibrations that can compromise the integrity of fastener assemblies.
Single coil spring washers are selected for their proficiency in maintaining clamping force under these extreme conditions. The quality control standards in aerospace are exceptionally stringent; thus, single coil spring washers employed in this sector are typically manufactured from high-grade materials such as stainless steel or alloy steel, demonstrating their robustness and durability.
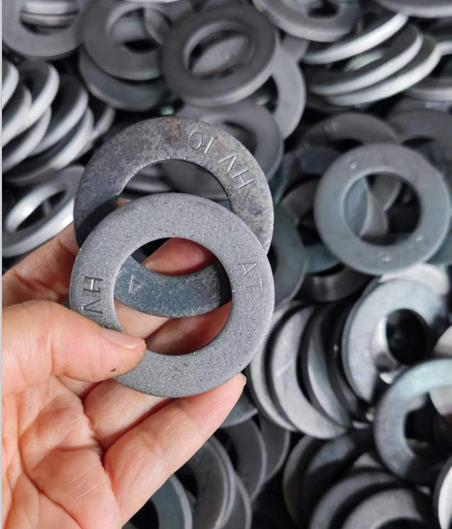
From an engineering perspective, the design of the single coil spring washer is particularly efficient. The helical shape not only provides the necessary spring action but also distributes the load more evenly across the fastened surfaces. This distribution reduces the likelihood of stress concentrations that could potentially lead to joint failure. Experts in mechanical design appreciate these washers for their simplicity and effectiveness in applications where dimensional constraints are a consideration. They facilitate a balance between maintaining necessary joint tightness and allowing for tolerances in manufacturing processes.
single coil spring washer
Professional installers and maintenance technicians often laud the ease of installation associated with single coil spring washers. They are straightforward to integrate into assembly processes, often requiring no specialized tools beyond standard torque wrenches to ensure proper installation. This characteristic makes them particularly appealing in maintenance scenarios where prompt and efficient service is crucial. High trustworthiness with minimal need for re-tightening translates to a cost-effective solution across industries.
Despite their many advantages, the choice of material for single coil spring washers must be carefully considered to match the application's environmental conditions. For instance, in corrosive environments or where exposure to moisture is prevalent, stainless steel versions provide superior corrosion resistance, significantly extending the life of the fastened assembly. Similarly, when dealing with electrical assemblies, phosphor bronze or other non-ferrous materials might be preferred to prevent electrical conductivity interference.
It is this adaptability and proven reliability that continue to elevate the stature of single coil spring washers in construction and manufacturing industries worldwide. As a best practice, engineers must consider the material compatibility, environmental conditions, and mechanical requirements of each specific application to optimize the performance and longevity of the spring washer in use.
In summary, single coil spring washers provide a trusted solution for maintaining joint integrity in various challenging environments. Their simple yet effective design ensures reliability while their material diversity allows them to be tailored for specific industrial requirements, making them a staple in precision engineering. As industries progress, the continuous innovation and improvement of these washers are expected to further solidify their role as an essential component in secure fastening solutions, demonstrating enduring expertise and trustworthiness in engineering applications.