Self-tapping screws are indispensable in the world of metalworking, prized for their ability to create their own threads while being easily installed into a material. These screws offer the convenience of securing metal pieces without requiring pre-drilled pilot holes, thereby streamlining the construction process. Understanding how to effectively use self-tapping screws in metal is key to ensuring robust and durable metal constructions.
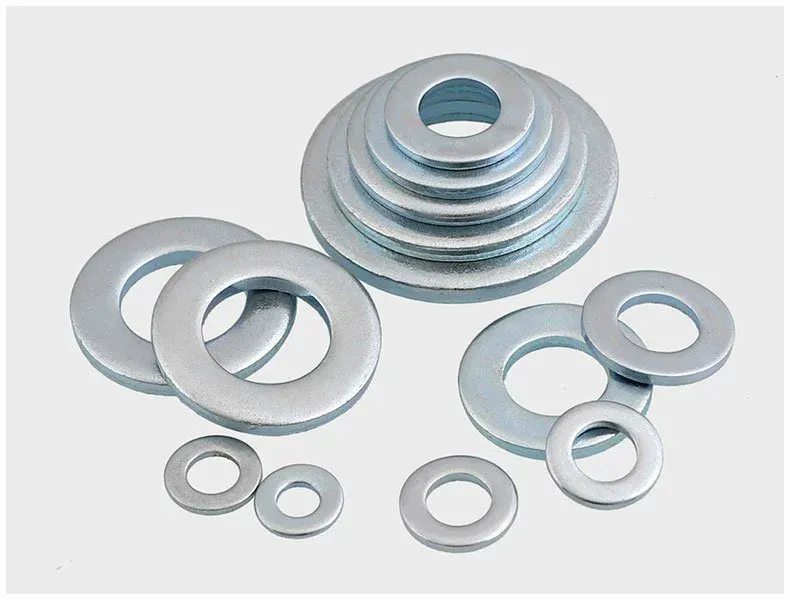
To begin with,
selecting the right type of self-tapping screw for metal is crucial. These screws come in a variety of shapes and sizes, each tailored for specific metal types and thicknesses. For instance, when working with softer metals like aluminum, choose screws with finer threads to minimize the risk of stripping. Conversely, harder metals like steel may require screws with coarser threads and robust points to ensure secure penetration.
Preparation is another essential step when using self-tapping screws on metal surfaces. Despite the self-tapping nature, it's often beneficial to mark the intended screw location with a center punch to prevent wandering, especially in harder metals. This step can be critical in maintaining the precision of your work, mainly where alignment is of paramount importance.
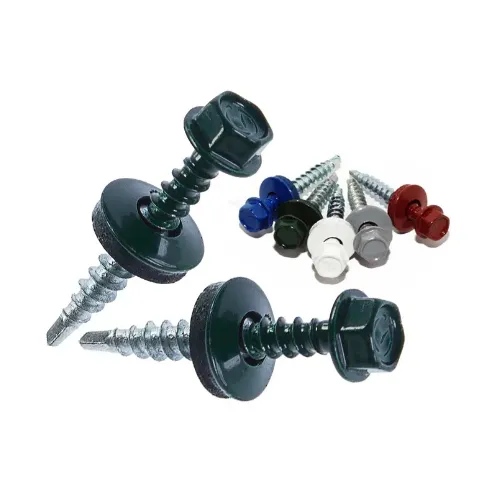
Moreover, when using self-tapping screws, the type of drill or driver bit you choose plays a significant role. Ensuring your tool delivers the appropriate level of torque is key; too much force can strip the threads or damage the screw, while too little may result in an insufficient hold. This involves using the correct drill settings, often between 1,200 and 1,800 revolutions per minute (rpm) for the most effective engagement with the metal. Torque-controlled drills are particularly advantageous for this application, enabling consistent force that reduces the risk of damaging either the screw or the metal material.
It's also important to consider the material thickness. Thin metal sheets offer limited engagement depth for the screw threads, so selecting screws specifically designed for such applications is recommended. These often feature sharper threads and drill tips that penetrate more easily. For thicker metal materials, longer screws with robust, sharper cutting edges are more appropriate to ensure a strong hold.
self tapping screw into metal
The use of lubrication can greatly enhance the efficiency and ease of driving self-tapping screws into metal. Lubricants such as light oils or specialized metal drilling compounds can reduce friction and heat, minimizing the risk of breaking the screw or damaging the surface. This practice is particularly recommended when working with stainless steel or high-tensile strength alloys where friction can be a considerable issue.
Attention should also be paid to the environmental conditions in which the metal assembly will be used. In corrosive environments, choosing self-tapping screws made of corrosion-resistant materials, such as stainless steel or those coated with anti-corrosive finishes, is essential. This ensures the longevity of the assembly and maintains the integrity of the screw over time, preventing rust or degradation that could compromise the structural strength.
Maintenance and inspection of assemblies constructed with self-tapping screws play a role in long-term reliability. Regular checks should be conducted to ensure that the screws have not loosened over time due to vibration or thermal expansion. This is particularly important in assemblies subject to dynamic loads or extreme temperatures.
For those in industrial and construction sectors, understanding the nuances of various self-tapping screw designs is part of professional expertise. For instance, screws with hex heads offer greater torque resistance, making them ideal for heavy-duty applications, while slotted or Phillips head screws might be used where ease of maintenance and replacement is favored.
In conclusion, the effective use of self-tapping screws in metalwork involves not only the proper selection of screw type and size but also meticulous attention to preparation, driving techniques, and environmental considerations. By integrating these best practices, one ensures a high standard of construction quality and long-lasting assembly performance. For anyone involved in the creation or maintenance of metal structures, mastering the use of self-tapping screws is a vital skill that combines technical knowledge with practical application, resulting in reliable and efficient work outcomes.