When it comes to ensuring the stability and effectiveness of components in any mechanical assembly, the choice between a lock washer and a flat washer plays a pivotal role. These small, often underestimated elements are essential in securing fasteners and preventing potential mishaps. Their significance in engineering and various industries emphasizes the importance of knowledge in their proper application and differences.
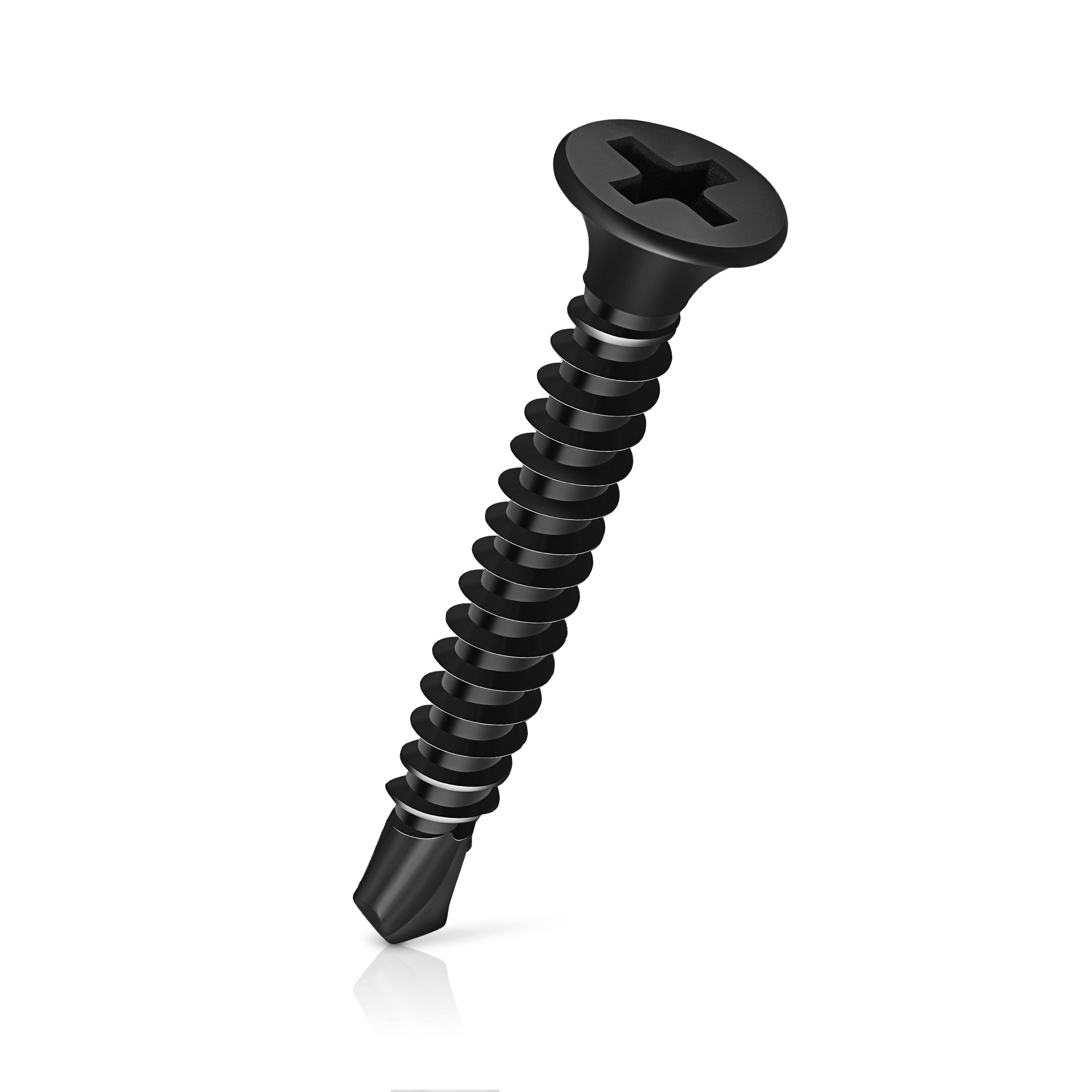
Lock washers are designed specifically to prevent nuts and bolts from rotating, slipping, or loosening due to vibration and torque. The predominant types of lock washers—such as split lock washers, tooth lock washers, and wedge lock washers—each have their distinctive applications. Split lock washers, characterized by their helical shape, apply a spring force against a fastener, ensuring it remains tight over time. On the other hand, tooth lock washers, equipped with small protruding teeth, provide a strong bite into the material and the fastener, offering a reliable lock against rotations. These washers are extensively used in scenarios where high-intensity vibrations are a concern, such as in automotive or machinery industries.
In contrast,
flat washers serve a primarily different purpose. They’re typically used to evenly distribute the force of a nut or bolt across a surface, reducing damage and wear. This is essential in preserving the integrity of softer materials which might otherwise deform under pressure. By providing a consistent and level bearing surface for the fastener, flat washers are invaluable in maintaining the structural balance of assemblies. Their use is crucial in preventing the surface from being damaged or from warping under pressure, which can lead to significant complications in system performance over time.
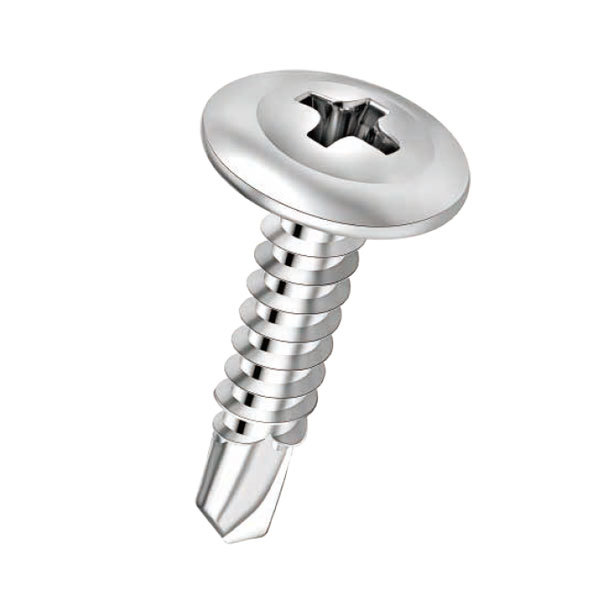
Numerous industry experts underscore the significance of washers in prolonging the lifespan of mechanical joints. A common recommendation is to assess the nature of the project meticulously before deciding between lock washers and flat washers. For installations expected to endure highs stress or movement, such as machinery exposed to continuous vibration, lock washers are indispensable. However, if the aim is merely to protect the surface and ensure a tight seal, as in plumbing projects, flat washers are often more appropriate.
lock washer flat washer
Moreover, the material of the washer is a critical consideration. Stainless steel, for instance, offers remarkable resistance to corrosion and is favored in marine environments, while plastic washers may be chosen for their non-conductive properties in electronic applications. Understanding the nuances of washer materials is essential in extending the performance life of the fastener systems and ultimately the machinery itself.
Businesses and project managers who invest the time in understanding these small yet critical components can significantly optimize their operational efficiencies and minimize maintenance costs. The precision in selecting the right type of washer is a testament to meticulous expertise that can substantially influence project outcomes. Industry advancements are consistently being made in enhancing the design and material of washers to cater to evolving engineering demands, underscoring their foundational importance in assembly and construction.
Those overseeing projects should leverage authoritative sources and consult with seasoned engineers to ensure the selected washers meet their specific needs. Earning trust through informed decision-making in the choice of components like washers not only demonstrates professionalism but also illustrates a commitment to quality and reliability. With technological advancements and innovative designs on the horizon, staying informed on the latest developments in washer technology ensures sustained success and operational integrity.