Choosing the right washer for your assembly is crucial in ensuring the longevity and reliability of mechanical connections.
Two commonly used washers are the flat washer and the spring washer, each serving distinct functions in a variety of applications. Understanding their roles, benefits, and optimal use cases can significantly enhance the performance of your assembly projects.
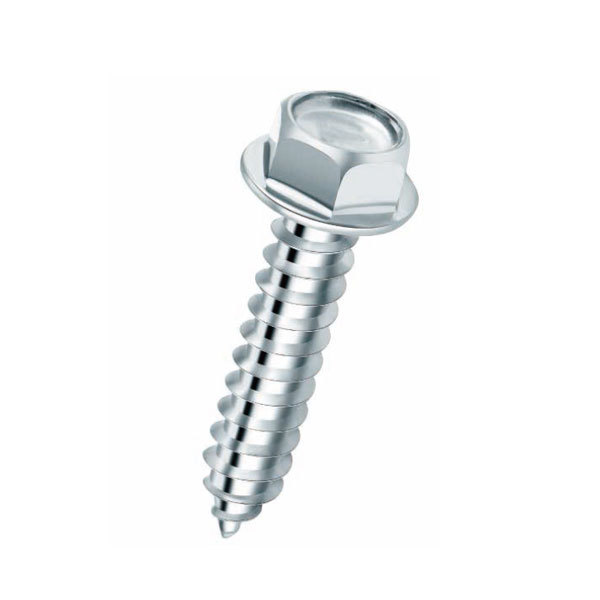
Flat washers, often referred to simply as plain washers, are designed to distribute the load of a threaded fastener, such as a screw or nut. The primary function of a flat washer is to reduce the likelihood of damage to the material being fastened. By increasing the bearing surface area, flat washers reduce friction, preventing fastener loosening and uneven wear. Made from various materials like steel, stainless steel, or even plastic, flat washers are chosen based on the environmental factors they need to withstand, such as exposure to moisture, chemicals, or extreme temperatures. This adaptability makes flat washers an essential component in industries ranging from automotive to construction.
On the other hand, spring washers, which include popular types like the split lock washer, offer a different set of benefits aimed at maintaining tension. The spring washer is ingeniously crafted to provide axial flexibility, thereby compensating for slight alignment errors and reducing the risk of loosening due to vibration or dynamic loads. This characteristic is especially valuable in automotive and aerospace applications where mechanical stability under variable conditions is paramount.
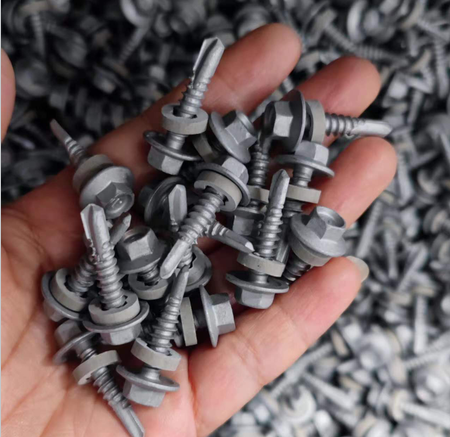
Despite their distinct functionalities, it’s not uncommon to see flat washers and spring washers used in conjunction for added security. The flat washer sits flush against the surface, safeguarding the material, while the spring washer maintains tension and prevents the fastener from loosening. However, when selecting washers, it is crucial to consider the specific demands of your application. For example, environments with a high degree of vibration might prioritize the use of spring washers for their locking capability, while applications requiring even load distribution may benefit more from flat washers.
flat washer and spring washer
Material selection also plays a pivotal role in the performance of both flat and spring washers. High-carbon steel provides excellent strength for both types, but when corrosion resistance is needed, opting for stainless steel or coated variants can extend the lifespan of the fasteners. For non-metallic applications, nylon flat washers offer non-conductive properties, enhancing safety in electrical installations.
To make informed decisions, understanding the engineering aspects behind each washer type can leverage expertise in optimizing mechanical assemblies. Flat washers, due to their simplicity, are straightforward but should be chosen with thickness and diameter in mind to ensure compatibility and effectiveness. Meanwhile, selecting the right spring washer involves considering the spring tension required, which is influenced by the gauge and coil design of the washer.
Incorporating this knowledge enhances the authoritative approach to selecting washers, building trust in your mechanical assemblies' reliability and performance. Maintenance considerations also inform washer selection, as easily accessible and replaceable components can simplify long-term upkeep, reducing downtime and costs associated with assembly disassembly.
In conclusion, the choice between flat washers and spring washers—or the decision to combine both—should be informed by the specific mechanical requirements of your application. Mastering their use not only reduces the risk of equipment failure but also enhances the efficiency and safety of machinery. With a nuanced understanding of these essential components, one can optimize their use across a multitude of settings, boosting the credibility of your engineering expertise and establishing trust in the durability and reliability of your projects.