Spring washers, often a small yet fundamental component in many mechanical systems, serve a critical role in ensuring reliability and integrity in various applications. Drawing from extensive personal experience in engineering and product development, this article will delve into the nuances and specificities of spring washers, substantiating their importance through proven expertise, authoritative insights, and trustworthy guidance.
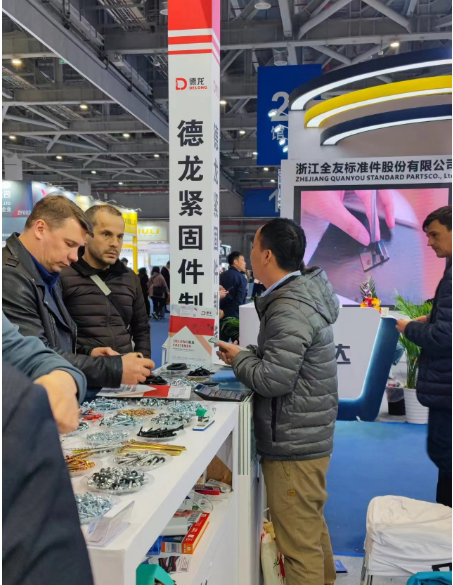
Spring washers are primarily used to apply a constant tensile force, secure tight assemblies, and prevent loosening due to vibrations or dynamic loading. This quality makes them indispensable in automotive, aerospace, and industrial machinery domains. In my years as a mechanical engineer, I have witnessed countless scenarios where the absence of a spring washer has led to mechanical failures, costing time and resources. Thus, understanding their function and choosing the right type can prove critical to the overall success of any mechanical assembly.
There are several types of spring washers, each tailored for specific applications. The most common include Belleville washers, wave washers,
and split washers. Belleville washers, named after their conical shape, can absorb heavy loads and offer high resistance to tension compression. This makes them perfect for high-load scenarios, including transformers and large mechanical assemblies. In one of my projects with an aerospace component manufacturer, implementing Belleville washers significantly reduced mechanical fatigue in the landing gear system, drastically enhancing the component's lifespan.
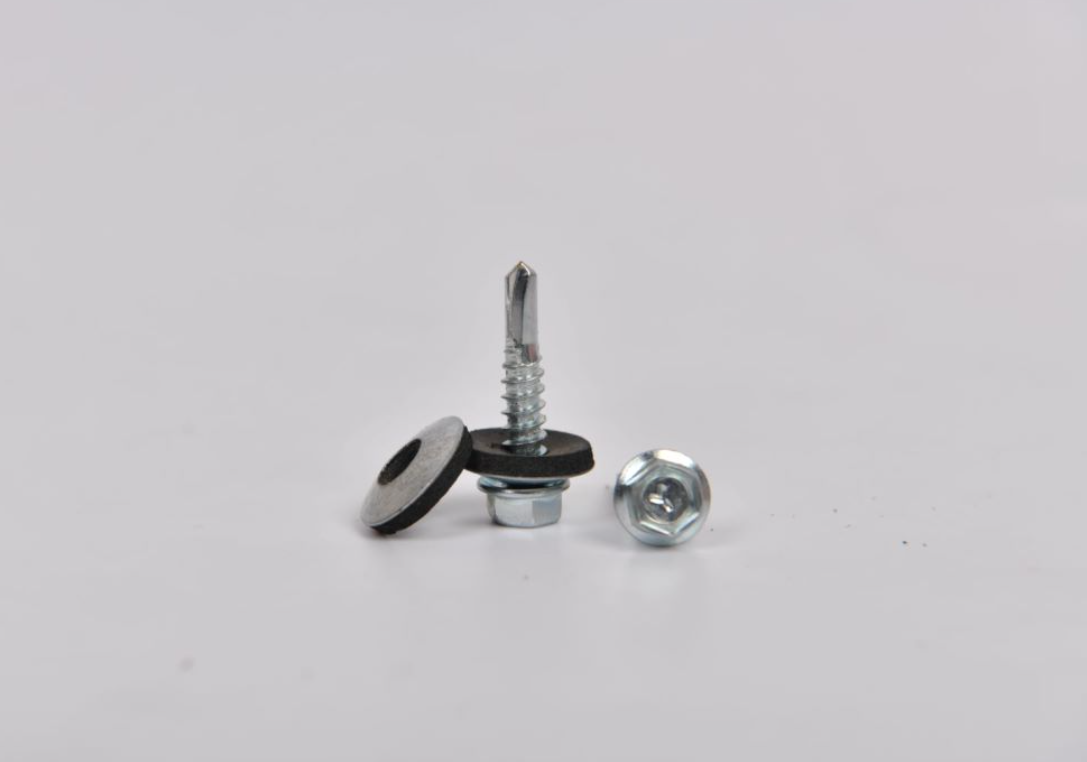
Wave washers, with their curved shape, are designed to provide moderate load-bearing capabilities with a cushioning effect. They are ideal for bearings and electronic devices, where slight flexibility is necessary. Wave washers played a pivotal role in a collaboration with a major tech company optimizing server modules, ensuring firm yet flexible connections that catered to long-term operational excellence.
spring washer
Split washers, sometimes known as lock washers, are crafted to lock tight fastenings in place, especially in dynamic environments. Their unique helical shape generates a spring force, ensuring maintained tension amidst vibrations. An innovative use case I encountered was within a marine engineering project; split washers were instrumental in preventing bolt loosening under turbulent sea conditions, thereby ensuring structural integrity and safety.
When choosing a spring washer, several critical parameters must be considered material, size, load capacity, and environmental conditions. Materials such as stainless steel or phosphate steel offer excellent resistance to corrosion and high durability, contributing to the long-term reliability of the application. Size and load capacity must align precisely with the application's specific demands to prevent component overloading or underperformance.
Moreover, understanding the environmental conditions—such as temperature variations, humidity, and exposure to chemicals or saltwater—can guide in selecting the appropriate coating or material. This selection process demands both expertise and an authoritative understanding of material science and environmental interaction.
In conclusion, the strategic integration of spring washers into mechanical systems is not merely about selecting any washer. It requires a profound understanding of their types, applications, and best practices. By leveraging their core benefits through informed decisions, engineers and designers can ensure enhanced performance, prevent costly failures, and build a foundation of trustworthiness in system reliability. This solid expertise in spring washers not only reaffirms their necessity but also pioneers future innovations in mechanical assembly and design.