When it comes to working with self-tapping screws in metric sizes, particularly when dealing with plastic materials, attention to detail is paramount. Through extensive experience in engineering and product development, understanding the interplay between the screw design, material properties, and hole sizing is crucial for achieving optimal performance and reliability.
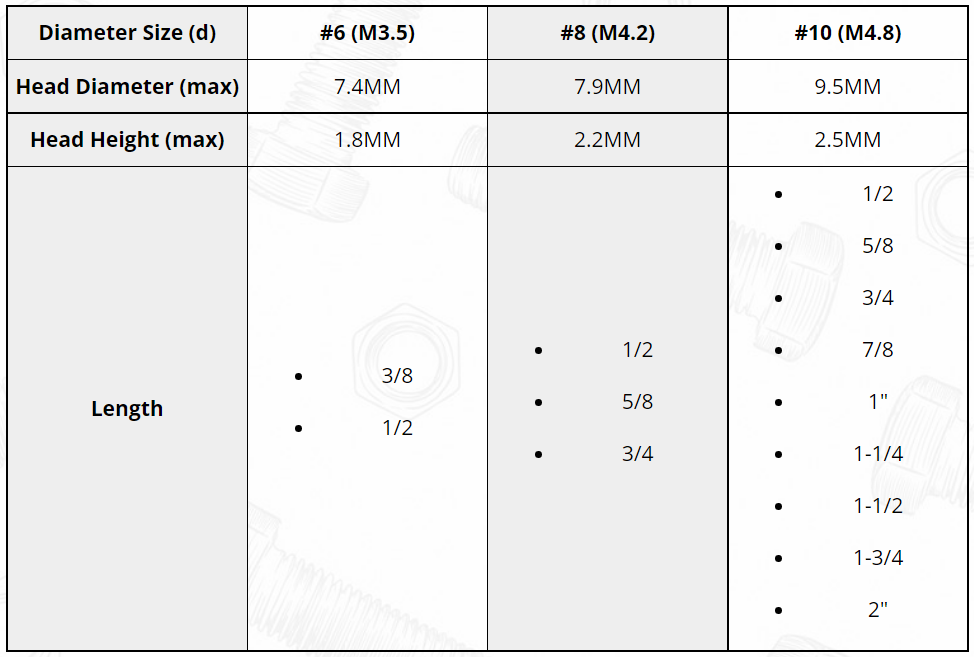
Self-tapping screws are designed to form their own threads in materials like plastic, which means their selection must be done with precision. The correct hole size is critical because it directly affects the screw's grip strength, the integrity of the plastic material, and the overall durability of the assembly. Factors such as the type of plastic, the environmental conditions, and the mechanical requirements of the application must be considered.
For those in engineering and manufacturing, understanding the types of plastics being used is the first step. Plastics can be broadly categorized into thermoplastics and thermosets, each having unique characteristics. Thermoplastics, such as polycarbonate and ABS, tend to be softer and tend to flow more than thermosets, which are more brittle. These inherent qualities significantly impact the screw's performance and the size of the hole it requires.
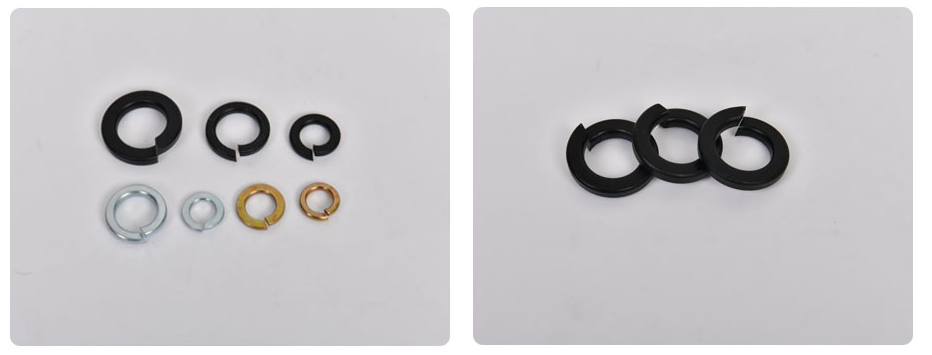
For instance, in softer thermoplastics, the hole size must be smaller relative to the screw diameter to ensure sufficient material is left to form the thread. A general rule of thumb for determining the pilot hole size for self-tapping screws in plastic is to use a diameter that is 70-80% of the screw's major diameter. However, this range can vary based on the specific material properties. For example, in more brittle plastics, or those with glass fillers, a slightly larger pilot hole may help prevent cracking or splitting during the screwing process.
Moreover, experientially, consult the manufacturer's specifications of the screws, as these often provide tested and recommended ranges for pilot hole sizes tailored to maximize performance. Each manufacturer may have specific guidelines based on their product testing, making their advice valuable especially when working with high-performance or critical applications.
self tapping screw hole size metric plastic
While the diameter is crucial, the depth of the hole is equally important. The hole should be deep enough to accommodate the full length of the screw while accounting for some space beyond the screw tip; this helps in absorbing any minor misalignments during the assembly process. Additionally, consider the nature of the threads on the self-tapping screw; some screws are designed with a sharper thread profile that allows for easier carving of the plastic, where hole size needs may differ slightly compared to screws with more rounded threads.
When discussing environmental conditions, keep in mind that plastics may expand or contract with temperature fluctuations, and some chemicals can either soften or harden the material. This necessitates periodic checks and adjustments in the pilot hole size to adapt to such environmental impacts to maintain the strength and stability of the joint.
In terms of expertise, engineers often utilize finite element analysis (FEA) to simulate the insertion of self-tapping screws into plastic components. This approach allows for optimizing hole sizes by virtually observing how different variables affect assembly performance. Testing is often bolstered by physical trials where samples are subjected to stress tests to validate the computational models.
Finally, trustworthiness in assembling with self-tapping screws into plastic demands rigorous quality control. Each batch of screws and plastic components should be inspected to ensure conformity to the desired specifications. By maintaining accurate and thorough documentation and using quality assurance techniques, the reliability and trust in the assembly process are fortified.
In conclusion, the interplay of material properties, screw specification, and environmental factors must all be synchronized to determine the perfect metric self-tapping screw hole size in plastic applications. Adopting a methodical approach that blends empirical data with advanced simulation technology can greatly enhance the reliability and performance of self-tapping screw applications in plastic products.