In the intricacies of mechanical engineering and assembly processes, the spring washer often takes center stage, despite its unassuming appearance. This small yet crucial component plays a vital role in ensuring the longevity and functionality of machinery. Understanding the purpose and application of spring washers can greatly enhance the efficiency and safety of various mechanical systems.
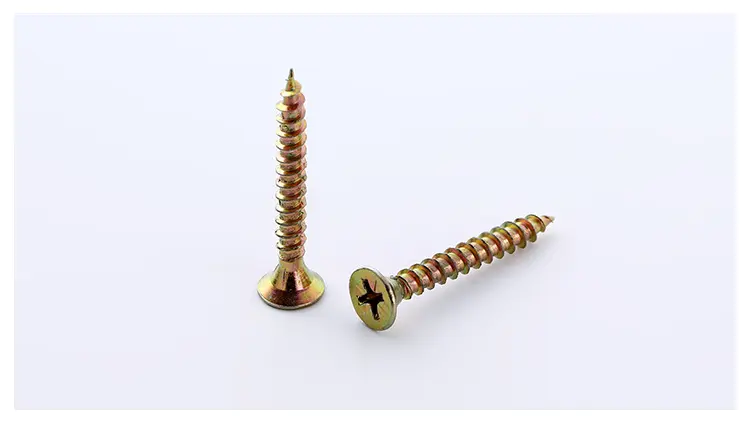
Spring washers, also known as disc springs or Belleville washers, are designed to provide a preload between two surfaces, typically in bolted joints. They are characterized by their conical shape, which allows them to exert a linear force when compressed. This unique design differentiates them from flat washers, which primarily serve to distribute load or prevent surface damage. The effectiveness of a spring washer lies in its ability to maintain tension and combat loosening caused by external forces such as vibration, thermal expansion, or dynamic loads.
One of the primary purposes of a spring washer is to prevent the unwinding or loosening of a bolt due to vibration. In industries where machinery operates at high speeds or is subjected to vibrations, such as automotive, aerospace, and industrial manufacturing, the reliability of fasteners is paramount. Loose bolts can lead to catastrophic failures, risking equipment, productivity, and human safety. Spring washers address these concerns by exerting a continuous force, ensuring that the bolt remains tight under various conditions.
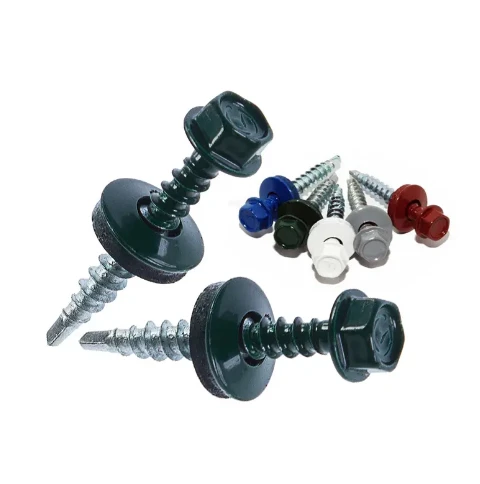
Another significant benefit of spring washers is their role in compensating for thermal expansion. Materials expand and contract with temperature changes, which can lead to gaps in fastened joints. Spring washers absorb these changes by contracting or expanding along with the material, maintaining the necessary tension to prevent loosening. This characteristic is particularly beneficial in situations where equipment experiences temperature fluctuations, such as engines or heating systems.
Furthermore, spring washers are instrumental in distributing load evenly across a surface. When a bolt is tightened, an uneven distribution of force can cause stress concentrations, leading to material fatigue or deformation. The conical shape of a spring washer helps in spreading the load evenly, reducing the risk of such damage and prolonging the life of both the fastener and the connected components.
purpose of spring washer
Mechanical experts have long advocated for the use of spring washers in critical applications due to their ability to enhance reliability. Their use spans from simple applications in household appliances to complex systems in spacecraft. The design and selection of an appropriate spring washer require a deep understanding of the mechanical environment, including load characteristics, environmental conditions, and material properties.
Precision in selecting the right spring washer is essential. Engineers must consider factors such as load capacity, deflection rate, and material compatibility. For instance, stainless steel spring washers are ideal for corrosive environments, while phosphor bronze variants offer superior electrical conductivity for electronic applications.
Authoritative entities and standards-setting organizations such as the American National Standards Institute (ANSI) and the International Organization for Standardization (ISO) provide guidelines and specifications to ensure the quality and performance of spring washers. Trusted manufacturers adhere to these standards, offering assurance of their products' reliability and consistency.
Moreover, the experience and expertise of professionals in sourcing and utilizing spring washers cannot be overstated. Their knowledge ensures the correct application of these components, contributing significantly to operational excellence and safety.
In conclusion, the spring washer, though small, serves a pivotal purpose in maintaining the integrity of mechanical assemblies. Its ability to prevent loosening, accommodate material expansion, and distribute load highlights its indispensable role across various industries. Knowledgeable application of spring washers, backed by adherence to international standards and expert guidance, guarantees enhanced performance and durability in mechanical systems. As technology and engineering practices evolve, the reliance on these modest components remains, underscoring their timeless value in the world of mechanics.