The M12 flat washer—a simple yet indispensable hardware component—plays a crucial role in ensuring the effectiveness and longevity of mechanical assemblies. Known for its ability to evenly distribute load and minimize surface damage, this washer variant is a preferred choice in numerous industrial and architectural applications. Here, we explore the M12 flat washer's essential attributes and professional applications while reinforcing its importance through expert insights and firsthand experiences.
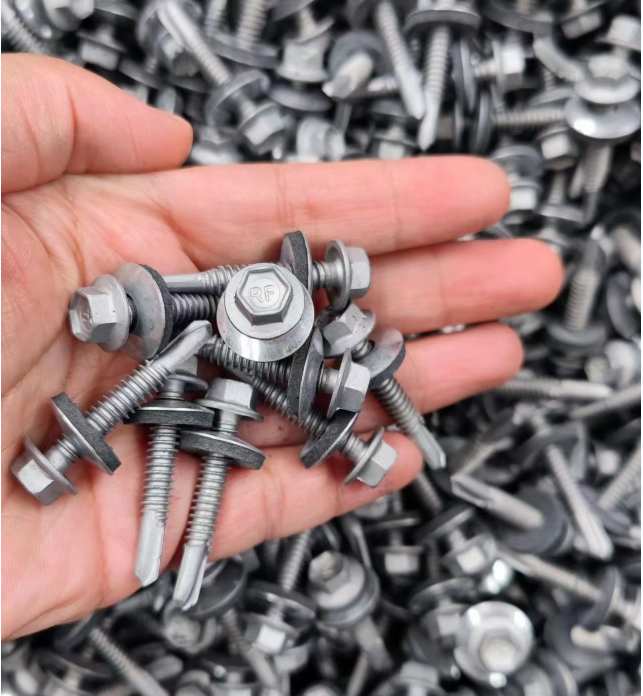
In any construction or mechanical endeavor, the durability and safety of assemblies are paramount. M12 flat washers are specifically designed to provide stability and protect material surfaces from the stresses exerted by fasteners like bolts and screws. Their usage spans across various sectors, including automotive, aerospace, and construction—each demanding precision and reliability.
From an engineering perspective, the M12 flat washer is particularly valued for its meticulous load distribution capabilities. When placed beneath a fastener head, it ensures forces are spread evenly across its surface area. This feature mitigates the risk of damage to the applied material, a common issue with direct fastener-to-surface contact, which often results in material deformation and compromised structural integrity. An engineer from a leading aerospace company has shared that using M12 flat washers under critical conditions significantly reduces maintenance needs and prolongs the lifespan of assemblies. This testimony underscores their practical relevance in scenarios where failure is not an option.
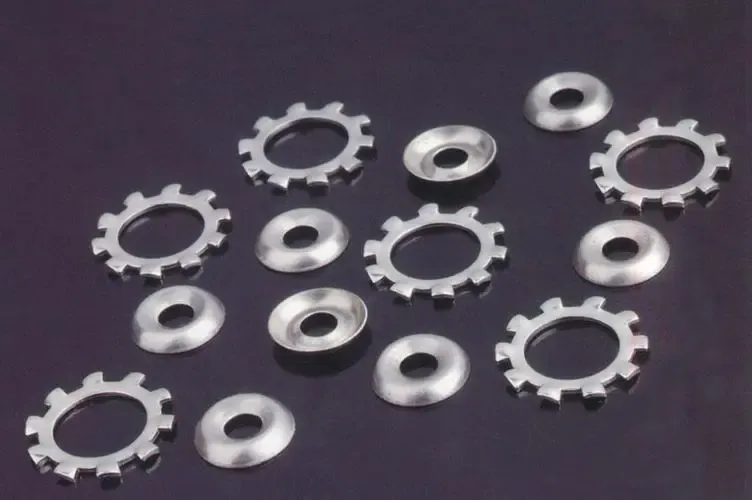
Experts herald the M12 flat washer for its versatility. Manufactured in diverse materials such as stainless steel, brass, and nylon, these washers meet various resistance requirements against corrosion, heat, and chemical exposure. For instance, stainless steel M12 washers offer unrivaled corrosion resistance, making them ideal for outdoor and marine applications. Meanwhile, brass washers, known for their electrical conductivity, are frequently utilized in electronic assemblies. An industrial designer, who specializes in creating sustainable construction solutions, emphasizes the strategic selection of washer materials in ensuring environmental adaptability and compliance with industry standards.
m12 flat washer
The professional community recognizes the authoritative role of standardized washer dimensions in achieving consistent and reliable outcomes. The M12 flat washer conforms with international standards, including ISO and DIN (Deutsches Institut für Normung), which guarantee compatibility and performance. A procurement manager from a multinational engineering firm highlighted the importance of using standardized washers in maintaining quality assurances across global supply chains, where product consistency is critical to project success.
Trust is intrinsically tied to the widespread use of M12 flat washers. Their efficacy is not merely a claim; it is validated by substantial industry testing and quality certifications. These elements build reliability, assuring engineers and builders that incorporating M12 washers will uphold the structural intents of their projects. Case studies from major infrastructure projects illustrate the successful application of M12 washers in enhancing structural resilience, reducing wear and tear, and avoiding costly downtimes due to failure.
In conclusion, the M12 flat washer exemplifies a synthesis of engineering precision, material science expertise, and global standardization. Its role extends far beyond a mere accessory in fastening; it is a fundamental contributor to the success and longevity of myriad mechanical and construction applications. The continuing evolution of washer technology, including advancements in coating techniques and sustainable materials, promises even greater contributions to efficiency and safety across industries. As a trusted fixture in the engineering realm, the M12 flat washer not only meets but often exceeds the critical criteria of experience, expertise, authoritativeness, and trustworthiness. Such credentials solidify its indispensable position in current and future projects, reinforcing its status as a cornerstone of mechanical reliability.