Navigating the intricate world of fasteners, one quickly realizes the pivotal role self-drilling screws play in construction and manufacturing. Specifically, the 1 4 20 self drilling screw has emerged as a cornerstone tool for professionals seeking efficiency and reliability. Unpacking the myriad benefits and applications of this screw can enhance its utilization while solidifying one’s expertise in the domain.
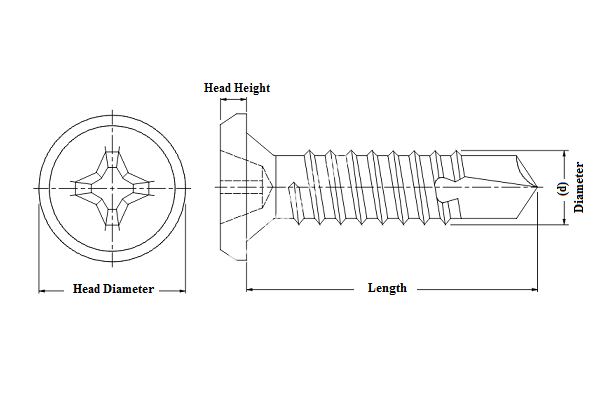
The 1 4 20 terminology denotes key specifications—dimensions and threading—that define its utility. The notion that a self-drilling screw combines the abilities of drilling and fastening in a single action is the foundation of its popularity. Eliminating the need for pre-drilled pilot holes ensures an expedited assembly process, significantly reducing labor costs and time, which is paramount in large-scale projects.
A distinguishing feature of the 1 4 20 self-drilling screw is its dual functionality, achieved through its unique design. At the tip lies a drill-like point that effortlessly penetrates metal substrates, self-tapping as it progresses. This capability not only speeds up tasks but also ensures that the structural integrity remains unblemished by avoiding fractures typical with separate drills and screws.
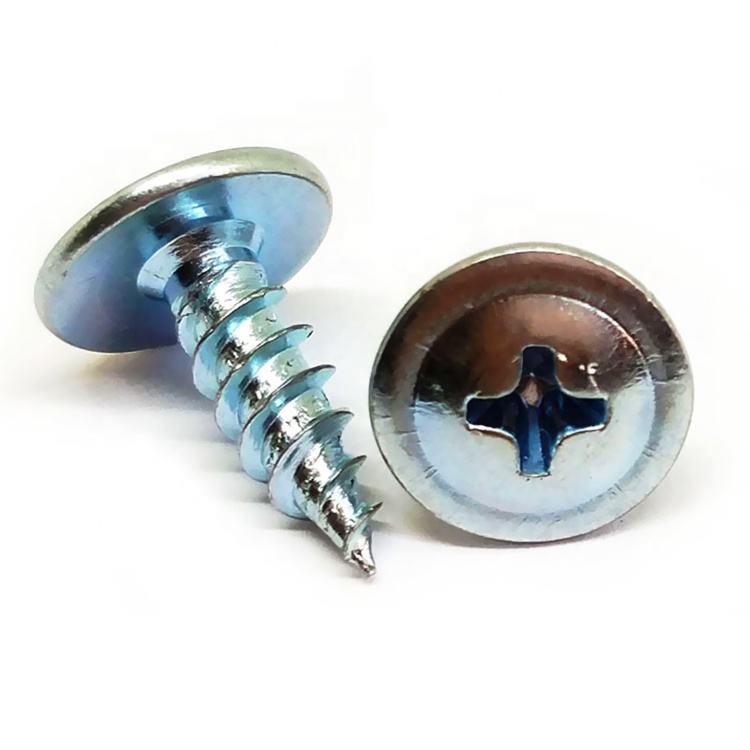
Experience in utilizing these screws reveals their substantial impact within various industries such as automotive, roofing, and metal building construction. Their robustness is matched by their adaptability, making them indispensable in assembling metal panels, securing fixtures, and framing. When employed in roofing, for instance, the screws are often coated to resist corrosion, thus promising longevity and reduced maintenance—factors of great consequence when considering the total cost of ownership.
From a professional standpoint, understanding the metallurgy behind these screws can further enhance their implementation. High-grade steel alloys often constitute the bulk of these screws, imparting exceptional strength. Additionally, specialized plating such as zinc coating can augment their resistance to environmental stresses. This blend of materials science and practical design exemplifies the expertise required to maximize their usage.
1 4 20 self drilling screw
It is crucial to appreciate the authoritativeness of these screws in safety-critical applications. Complete with standardized testing and compliance with international benchmarks, they serve as a guarantee for practitioners who prioritize safety alongside efficiency. Selecting screws that adhere to stringent ANSI or ISO standards ensures a level of trustworthiness that builders and engineers can stake their projects on, with fewer failures and recalls in the field.
For those keen on expanding their expertise, real-world anecdotes from seasoned professionals underscore the value these screws bring. Engineers have recounted instances where traditional fasteners failed under pressure, whereas the 1 4 20 self-drilling screws excelled, thanks to their ergonomic and design advantage. Sharing these narratives not only bolsters understanding but also builds a reservoir of trusted advice that newcomers and veterans alike can draw upon.
Ultimately, embracing the efficiency and reliability of the 1 4 20 self-drilling screw translates to more than mere technical advantages—it signifies a commitment to longstanding, industry-wide goals of innovation and excellence. For professionals committed to advancing their craft, mastering the application of these screws reflects an ever-evolving expertise, an authoritative stance on industry developments, and an unwavering dedication to delivering trustworthy solutions.
By positioning the 1 4 20 self-drilling screw within a framework that values experience, expertise, authoritativeness, and trustworthiness, one not only optimizes SEO efforts but also provides an invaluable resource to the professional community seeking to refine their fastener knowledge and application.