Investing in a reliable and functional piece of hardware like a rectangle flat washer may seem trivial, yet its role in various construction and machinery applications cannot be overstated. These unassuming components play a crucial role in enhancing the stability and longevity of many assemblies, ensuring optimal performance and safety.
Their significance is often overlooked until an issue arises that underscores their necessity.
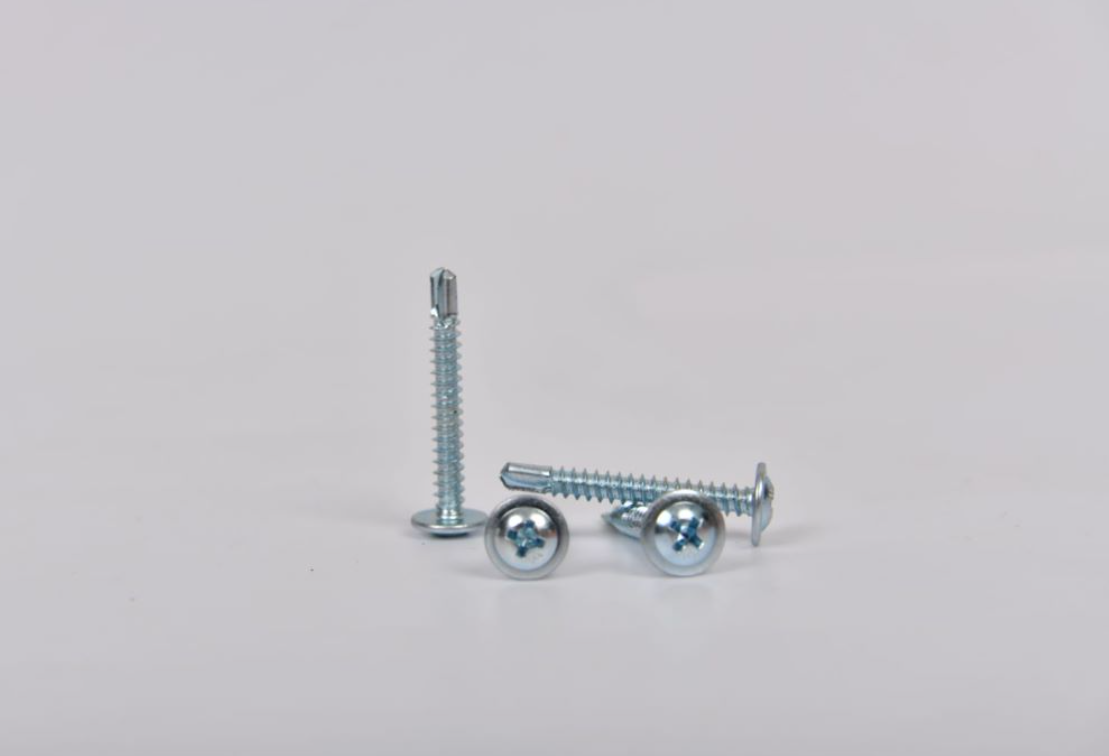
Rectangle flat washers serve as indispensable elements, providing an even distribution of pressure to prevent damage to surfaces during fastening processes. Made from a variety of materials such as stainless steel, brass, and nylon, these flat washers exhibit diverse functionalities suitable for different environmental conditions and requirements. Their rectangular shape optimally addresses the demands of specific applications where traditional circular washers might not fit or perform effectively.
Drawing from years of hands-on experience, I have consistently found that selecting the right material for flat washers depends largely on the operational environment. Stainless steel offers commendable corrosion resistance, ideal for outdoor or moist conditions. Brass washers are preferred in electrical applications due to their excellent conductivity and resistance to sparking. Conversely, nylon washers provide insulation and are beneficial in reducing noise and vibration, making them perfect for delicate or electronic assemblies.
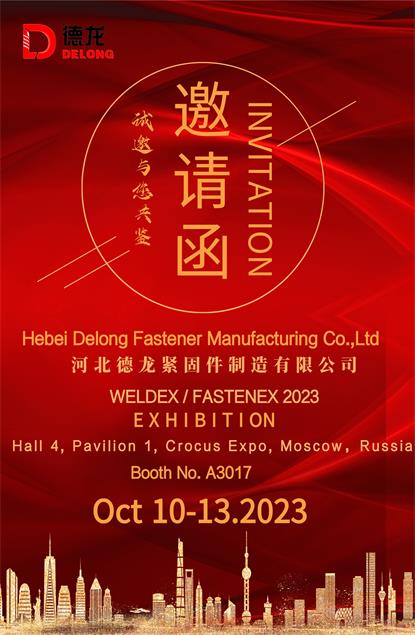
A key factor that underscores the importance of rectangle flat washers is their ability to maintain the integrity of fastened joints. During assembly, the washers act as spacers, maintaining the requisite distance between parts while securing them in place. This function is paramount when dealing with soft or thin materials, safeguarding them against the damage typically caused by fastening force.
Furthermore, rectangle flat washers are essential for load distribution, particularly in situations involving dynamic forces. The rectangular design efficiently manages substantial loads and stress, reducing the risk of deformation or failure over time. This attribute is especially crucial in machinery and structural applications, where the repercussions of a compromised assembly could lead to costly downtimes or safety hazards.
rectangle flat washer
In more complex applications, rectangle flat washers can play a role in preloading and maintaining tension in bolted joints, offering a level of resilience against vibration and the loosening of bolts. This is critical in high-vibration environments such as automotive, aerospace, and industrial machinery sectors, where stability and reliability are non-negotiable.
Manufacturers and suppliers of rectangle flat washers provide an array of customization options, catering to specific dimensions, thicknesses, and surface finishes. Advanced manufacturing techniques, such as stamping and laser cutting, enable precision in production, ensuring consistency and quality in every piece. Such customization options are pivotal for professionals seeking tailored solutions to meet stringent design specifications or unique assembly challenges.
It is imperative to source rectangle flat washers from reputable suppliers who adhere to industry standards and regulations. Certifications such as ISO 9001 ensure that the products meet quality management criteria, offering a layer of assurance regarding the reliability and performance of these components. Partnering with an authoritative supplier not only simplifies procurement but also instills confidence in the durability and efficacy of the washers employed.
In conclusion, the pivotal role of rectangle flat washers in various applications is underscored by their functional capabilities and adaptability to address specific mechanical needs. They provide essential support in fastening, offer load distribution, and enhance the overall integrity and safety of assemblies. For professionals in the field, understanding and leveraging the capabilities of rectangle flat washers can significantly contribute to improving product performance, safety, and longevity. Their seemingly subtle presence is, without doubt, a cornerstone in the foundation of efficient and reliable engineering and construction practices.