Understanding the appropriate size for self-tapping screw holes demands a harmonious blend of precision, expertise, and attention to material specifics. Whether you're a professional craftsman, an engineer, or an enthusiastic DIYer, it's crucial to grasp the essential rules and standards in order to ensure the longevity and integrity of your projects. This exploration covers the pivotal elements of determining the size for self-tapping screw holes, tailored to deliver a durable and stable assembly.
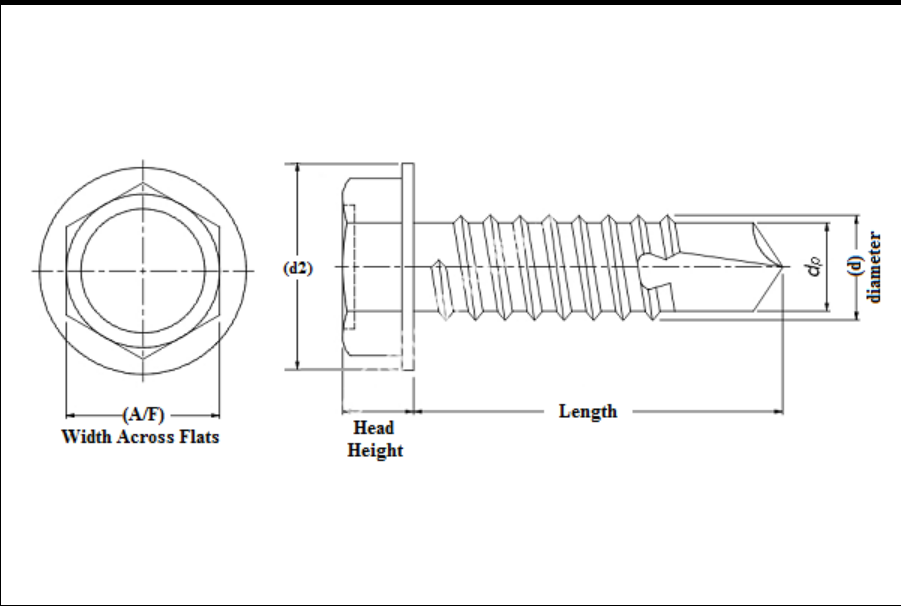
Self-tapping screws are designed to form threads as they enter the material, making them ideal for applications where speed and efficiency are crucial. However, their effectiveness is significantly reduced if the pilot holes are inaccurately sized. A hole that's too small might lead to material damage or stripping, while one that's too large could result in a loose fit, compromising the joint.
Firstly, understanding the type of material you're working with is fundamental. The hardness and density of materials such as metal, wood, or plastic will greatly influence the optimal hole diameter. For metal, the size is typically 85-95% of the screw's major diameter to ensure enough material is displaced for threading without excessive stress. For wood and softer materials, the ideal pilot hole size is generally about 70-90% of the screw's diameter, providing a balance that allows the screw to carve an appropriately deep thread while maintaining grip.
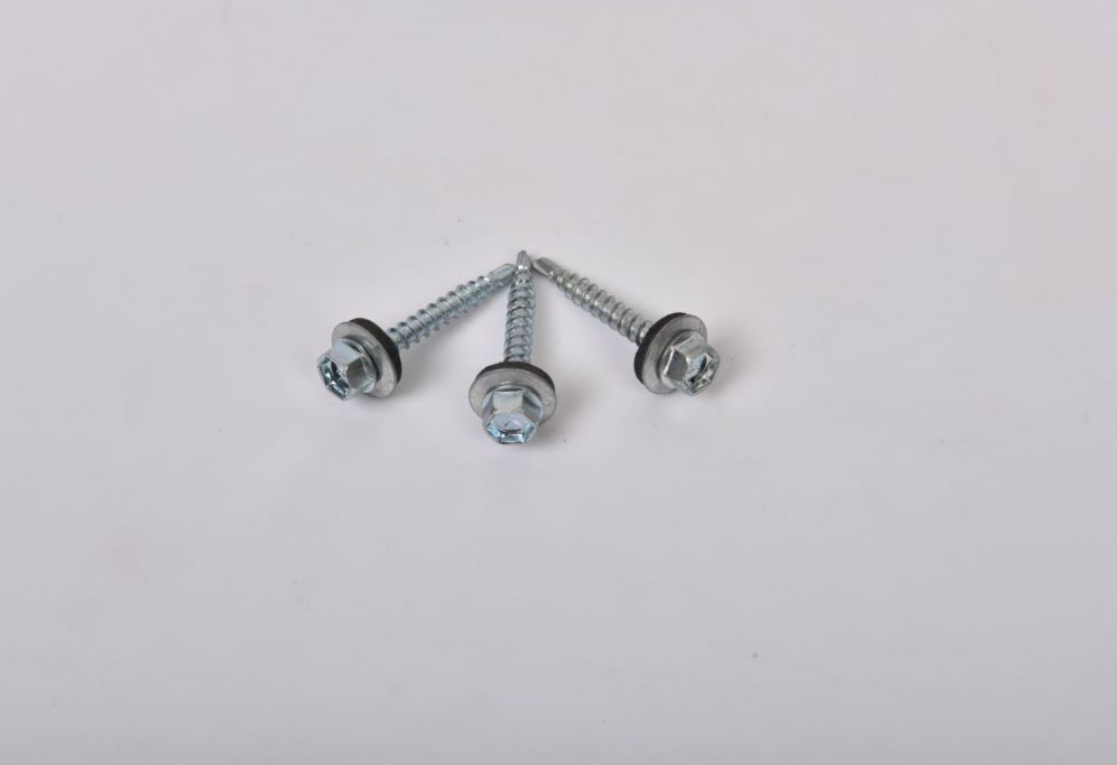
Next,
gauge the screw's thread design and taper. Self-tapping screws come with different thread patterns--some are engineered for soft materials and feature wider, deeper threads, while others are suitable for hard materials with finer threads. The screw’s point design also contributes to how smoothly the screw will penetrate the material and whether it will require a pre-drilled pilot hole.
Professional expertise recommends always testing on a scrap piece of the same material to fine-tune the pilot hole size. This practice not only helps in preventing costly mistakes but also provides valuable insights on the interaction between the screw and the material in real-world conditions.
4 self tapping screw hole size
When addressing the potential complications related to self-tapping screws and their respective hole sizes, consider the environment and external stresses. Should the final application face constant vibration or structural loading, selecting a larger pilot hole may reduce stress on the surrounding material and avert premature wear or failure.
In terms of tooling, using the correct drill bit is of paramount importance. Precision drill bits, perfectly matched to the recommended pilot hole size, ensure a clean cut and reduce the risk of distorting the material. Proper tool maintenance, including keeping drill bits sharp and utilizing a steady drilling technique, is necessary to achieve the best results.
Finally, validate your understanding and execution with detailed guidelines and references from authoritative sources such as manufacturers' technical documentation or engineering standards such as those from the American National Standards Institute (ANSI) or International Organization for Standardization (ISO). These references provide specific metrics for various screw sizes and materials, enhancing your trust in the process and outcome.
Mastering self-tapping screw hole sizes involves not just theoretical knowledge but also practical know-how, including assessing the mechanical properties of materials, scripting assembly parameters, and acknowledging real-world testing to uphold the structural integrity and longevity of your projects.