When considering the precise size for self-tapping screw holes, understanding the nuances involved is crucial for both DIY enthusiasts and professional contractors. Self-tapping screws offer the advantage of creating threads in materials, hence the importance of ensuring the correct hole size for optimal performance. By following the guidance of seasoned professionals, one can navigate these considerations effectively.
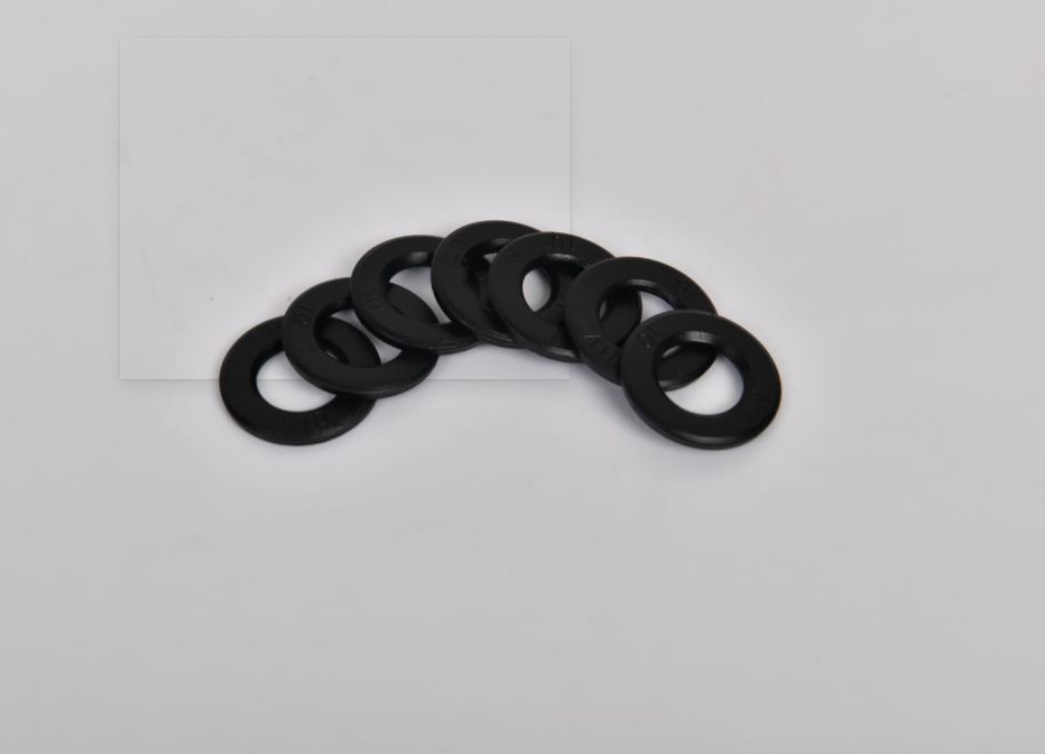
First,
delve into the mechanics of self-tapping screws. These screws are characterized by their ability to cut their own thread as they penetrate the material. This feature calls for an accurately sized pilot hole, which provides a pathway for the screw to follow while preventing unnecessary splitting and material stress. The general rule is that the pilot hole should be slightly smaller than the screw diameter, allowing the screw to grip the material adequately while minimizing structural compromise.
The material type is a significant determinant in choosing the appropriate pilot hole size. In softer materials such as plastics or softwoods, a pilot hole that is about 70-80% of the screw’s major diameter often suffices. This ensures the material isn't overly stressed while providing enough resistance for the screw to form a thread. However, for harder materials, such as hardwoods or metals, the pilot hole should be closer to 85-90% of the screw diameter. The increased hardness necessitates a more significant pilot hole to prevent cracking or excessive force during installation.
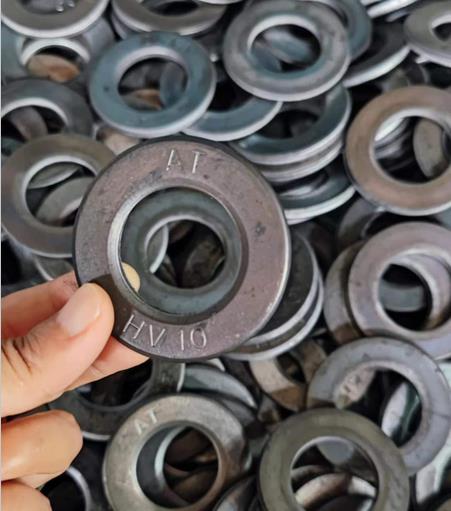
Beyond the material considerations, the intended application of the assembled product influences the choice of screw and hole size. For instance, in constructing load-bearing structures, ensuring a snug fit is paramount to maintain the integrity of the assembly. Here, additional considerations such as screw length, head type, and shaft design come into play, often guided by industry standards or engineering specifications.
Equally important is understanding the design and structure of the self-tapping screws themselves. They come in different types—such as thread-forming and thread-cutting. Thread-forming screws displace material around the pilot hole, demanding precise calculations to avoid material distortion. Conversely, thread-cutting screws remove material to form a thread, which means the pilot hole may slightly differ in size compared to thread-forming screws. This complexity underscores the importance of consulting detailed manufacturer datasheets or seasoned experts who can provide insights based on specific screw models and applications.
self tapping screw hole size
Professionals also emphasize the significance of quality tools in screw installation. Using well-maintained drills and bits ensures clean cuts and prevents the pilot hole from deforming, which could affect the holding power of the screw. This aspect highlights the broader narrative that tool quality, along with appropriate screw and hole sizing, contribute to successful installations—especially in commercial and industrial settings where precision is non-negotiable.
Scientific understanding of material properties and stress mechanisms reinforces the authoritative knowledge required in this domain. Engaging with academic literature and industrial reports provides insights into the theoretical aspects of self-tapping screw usage, enabling an informed approach to practical applications. This foundation of expertise supports not just optimal installations but also innovation in screw design and application techniques.
Finally, trustworthiness is built through adherence to recommended safety practices and standards. Ensuring that installations comply with regulations and guidelines affirms the reliability of the completed projects. It’s essential to document processes, use certified components, and, if necessary, consult with structural engineers to confirm that installations meet required safety and performance criteria.
In conclusion, the intricacies of determining the correct self-tapping screw hole size encompass a range of factors from material type and mechanical properties to application specificity and industry guidelines. Through knowledgeable application of these principles, one ensures both the structural integrity and longevity of assemblies, reflecting the expertise and trust that differentiate amateurs from seasoned professionals in the field of construction and manufacturing.