When evaluating the dimensions of the M4 spring washer, it is crucial to consider several factors that can significantly impact its functionality in various applications. Spring washers are often overlooked compared to their hardware counterparts, but their role in providing tension and reducing loosening due to vibrations is paramount. An M4 spring washer is typically paired with an M4 bolt or screw, predominantly in mechanical and structural applications, ensuring a firm and reliable connection.
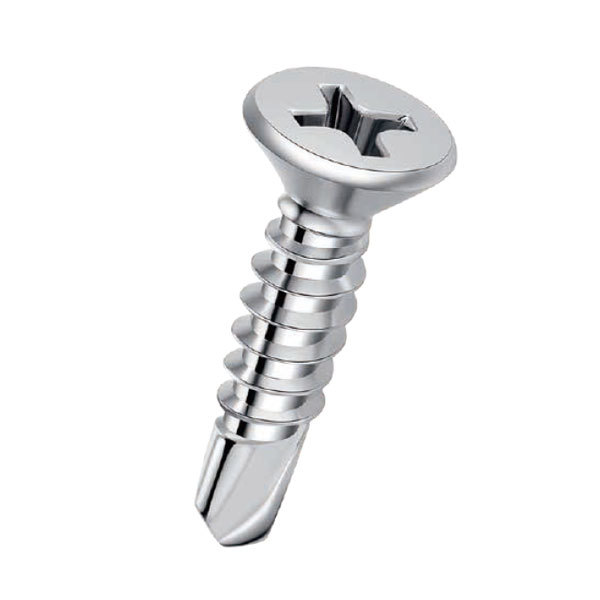
The nominal size of an M4 spring washer refers to the inner diameter, which is designed to fit seamlessly around a 4mm shaft.
Understanding the variances in dimensions among manufacturers can optimize its utility. Using the correct dimension ensures maximal load distribution and prevents hardware failure, thus enhancing performance and longevity.
For those unfamiliar with the technical breakdown, consider the following standard dimensions of an M4 washer the inner diameter generally measures around 4.3mm, allowing for ease of installation and slight room for adjustment without compromising integrity. Outer diameters, typically fluctuating between 7.6mm and 8.4mm, provide a generous surface area to distribute load and negate stress concentration around the bolt stem, which is paramount in maintaining the integrity of the assembled structure.
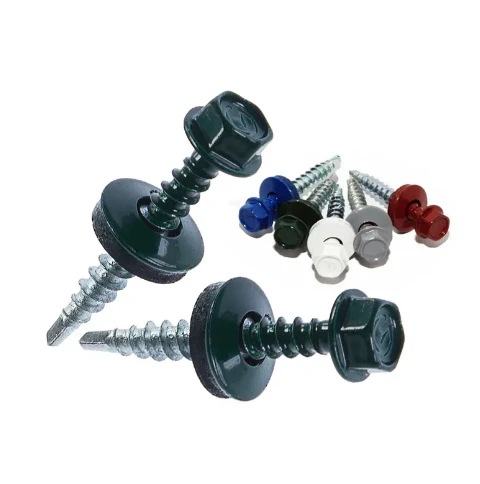
One of the defining features of a spring washer is its helical structure, specifically designed to offer axial flexibility – this is central to its function as it provides a spring effect, maintaining tension and mitigating the risks of spontaneous loosening under dynamic loads. Although the helical structure might vary slightly in height – a subtlety often detailed in engineering schematics – the standard M4 spring washer complies with international standards such as DIN 127 or equivalent.
The thickness of the washer also plays an essential role in its performance. With an optimal thickness ranging from 0.7mm to 1.0mm, it can effectively absorb load without added bulk, which aligns with engineering specifications requiring minimal deviation from calculated design loads. It is essential that these washers are able to compress sufficiently while returning to their original form, a characteristic closely tied to the material from which the washer is constructed.
m4 spring washer dimensions
Material choice profoundly affects the washer’s durability and effectiveness. Stainless steel is frequently chosen for its robust corrosion resistance and high tensile strength, making it suitable for diverse environments, including those with fluctuating temperature and exposure to moisture or chemicals. Stainless steel variants, including A2 and A4 grades, are prevalent options depending on specific environmental and structural requirements.
Furthermore, additional treatments such as phosphating, galvanization, or passivation can be applied to these washers, further enhancing their resistance to environmental degradation and extending their operational lifespan. Such treatments are particularly advantageous in preventing galling and seizing in high-tension applications, adding a layer of reliability and safety that is often necessary in critical installations.
Incorporating real-world testing into your evaluation to further authenticate its performance is prudent. Simulating environmental and mechanical stresses can validate the anticipated longevity and functionality of the washer. This practice also builds trust and authority with clients and stakeholders for whom reliable data-driven decisions are vital.
To ensure credibility and accuracy, consulting with hardware specialists or engineers when selecting an M4 spring washer is advantageous. Expert insight into the appropriate dimensions, materials, and treatment options based on application-specific requirements can elevate the overall efficacy of your mechanical assemblies.
Finally, it is worth noting that an optimal balance between cost-efficiency and performance should guide the choice of M4 spring washers. Investing in high-quality washers, albeit slightly more costly upfront, can avert potential failures and the associated costs of repair or replacement in the long term, demonstrating a prudent approach to mechanical design.