When it comes to fasteners in mechanical assemblies, the washer lock nut may not always be top of mind for everyone. However, for those deeply embedded in manufacturing, engineering, and DIY projects, its significance cannot be underestimated. Recognized for its ability to secure assemblies and prevent them from loosening over time, the washer lock nut is indeed a pivotal component in numerous applications.
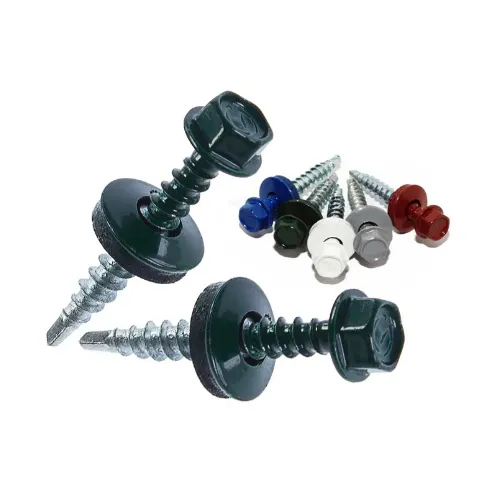
Early on in my engineering career, I encountered challenges that underscored the importance of using the appropriate fasteners. I was working on a project that required assembling components in an environment where continuous vibrations were inevitable. Initially, I opted for standard nuts, but after multiple setbacks including assembly failures, it became clear that a dedicated fastener was necessary. After in-depth research and discussions with senior experts, the washer lock nut emerged as the ideal solution.
This specific type of nut is designed with an integral washer-like base, which serves two primary functions. Firstly, it distributes the load over a larger surface area, significantly reducing the risk of damage to the assembled materials.
This makes it ideal for softer substrates where traditional nuts might cause wear or deformation. Secondly, its design inherently provides a locking mechanism—often through the use of a nylon insert or uniquely designed threading—which is vital for maintaining tension even amidst external forces like vibration or thermal expansion and contraction.
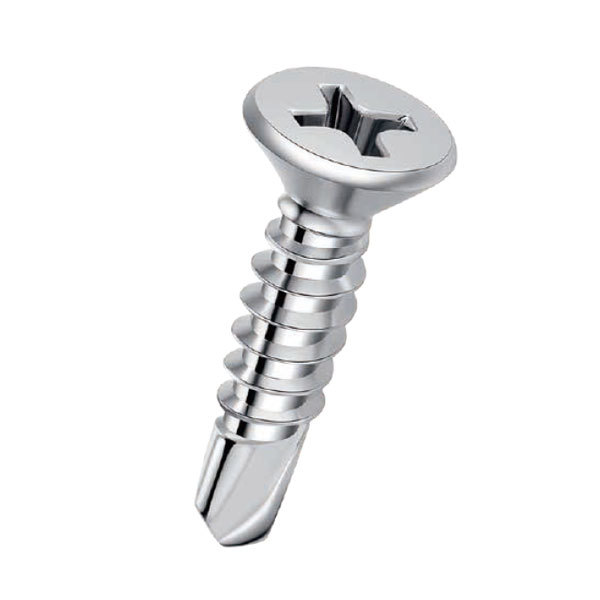
In professional practice, especially in fields like automotive engineering and aerospace, the washer lock nut's application is of paramount importance due to its reliability in critical operations. Its ability to maintain torque tension without the need for re-tightening makes it invaluable in ensuring safety and efficiency. Furthermore, it's the expertise in selecting the right grade, size, and material of the washer lock nut that distinguishes novice users from seasoned professionals. Stainless steel lock nuts are typically favored in environments where corrosion resistance is key, while zinc-plated variants are common in less demanding applications.
washer lock nut
From a materials science standpoint, the evolution of washer lock nuts has mirrored advances in metallurgy and polymer technology. Modern variations are now available with enhanced performance features, such as corrosion-resistant coatings and self-sealing properties, which further extend their longevity and effectiveness. Having seen firsthand the difference they make, it is no surprise that industries prioritize innovation in fastener technology to match the complex demands of contemporary engineering challenges.
Building trust around the use of washer lock nuts, particularly for critical applications, also extends to its sourcing. It is imperative to engage with reputable suppliers who adhere to global standards and can provide certification of their products' compliance. This not only assures the quality of the nuts themselves but also ensures they are a safe component of any assembly. Moreover, leveraging technical support from these suppliers can be invaluable, offering insights into optimal usage scenarios and installation best practices.
For those in legal or quality control roles, understanding the specifics surrounding the application and limitations of washer lock nuts plays a crucial role in maintaining compliance and upholding regulatory standards. Their expertise ensures that the right products are used for the right applications, minimizing risk and enhancing product integrity.
In conclusion, the washer lock nut is more than just a simple fastener; it is an engineering ally, crucial for the durability and security of many an assembly. Through a blend of practical experience, technical expertise, and authoritative sourcing, it stands as a testament to the complex but often unseen layers that contribute to successful manufacturing and engineering endeavors.