Choosing the right components in machinery and construction can be the difference between a successful project and unplanned downtime. While components like bolts and screws often gain the spotlight, the significance of a simple washer, particularly focusing on its flat side, is an underappreciated hero.
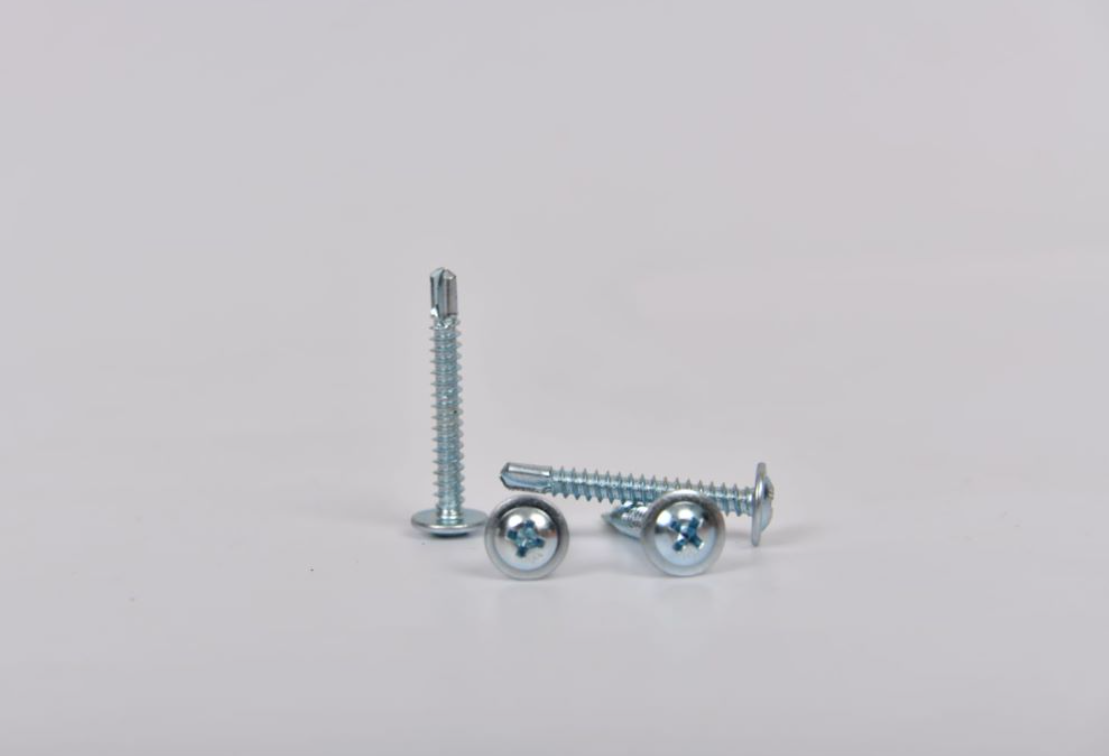
The washer's flat side plays a critical role. Primarily, it serves to evenly distribute the load of the threaded fastener with which it is used. This is crucial in ensuring that the integrity of the mating surfaces is maintained. The flat side ensures a consistent pressure spread, reducing the likelihood of damage to softer surfaces. This distribution is vital in high-stress applications where maintaining surface integrity can prevent costly repairs or replacements.
From a materials science perspective, the flat side of a washer is pivotal in mitigating the effects of vibration and corrosion. Its presence can significantly reduce loosening caused by vibration, a common issue in dynamic applications such as automotive or heavy machinery environments. High-performance materials, such as stainless steel or coated variants, are often used for their corrosion-resistant properties, ensuring long-term effectiveness in harsh environments.
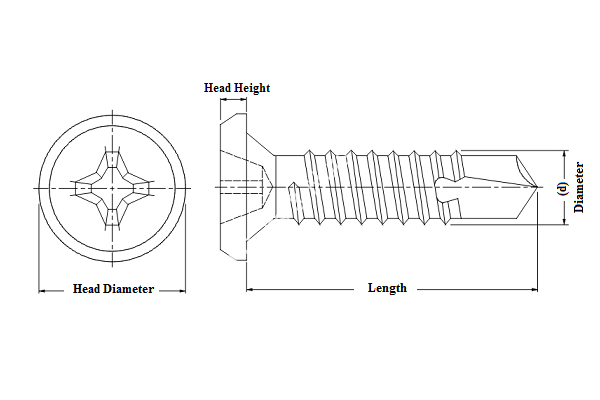
For industry professionals, understanding the specifics of washer selection enhances not only the lifespan of the mechanical assembly but also its performance consistency. When specifying components, choosing a washer with an adequately finished flat side is paramount. This may involve considering factors like coating type, thickness, and dimensional tolerances, which could influence the end product's suitability for specific applications.
The flat side’s dimensions and its surface finish also critically influence the tightening process. An uneven surface can lead to improper torque application, ultimately compromising the assembly’s integrity. Professionals understand that to achieve the desired torque and clamp load, utilizing a washer with a precision-engineered flat side becomes non-negotiable.
washer flat side
In industries driven by precision, such as aerospace or medical device manufacturing, reliance on these small but vital components underscores the importance of quality assurance inspections. Companies should maintain strict quality controls to ensure washers meet stringent criteria, thus safeguarding the application performance over time. Non-destructive testing methods, such as ultrasonic testing or X-ray, may be employed to verify component integrity without jeopardizing the washer’s effectiveness.
Expertise in identifying the right washer is a testament to a company’s commitment to reliability and quality. It also builds trust with clients who depend on these components for their products. Engineers and procurement professionals often recommend establishing strategic partnerships with reputable suppliers known for their stringent testing and high-quality materials, thereby ensuring that every washer performs its intended role flawlessly.
Ultimately, the choice to invest attention and resources into selecting the correct washer flat side demonstrates an enterprise's dedication to excellence. Such decisions resonate within the industry, reaffirming an organization’s reputation for meticulousness and dependability. Industry testimonials often highlight these behind-the-scenes choices, which, though invisible to the end user, are critical to operational success.
As technology continues to advance, the humble washer and its flat side will remain indispensable in our quest for precision engineering and durability. By appreciating its role and ensuring it meets peak standards, companies can reduce system failures, foster innovation, and maintain their competitive edge.