For those involved in construction, automotive repairs, or DIY projects, understanding the nuances of hardware components is crucial. One such component, often underestimated yet integral to numerous applications, is the USS flat washer. While seemingly simple, selecting the correct washer size is paramount to ensuring structural integrity and optimal functionality. Here, we delve into the USS flat washer size chart, shedding light on its importance, specifications, and the meticulous considerations that accompany its use.
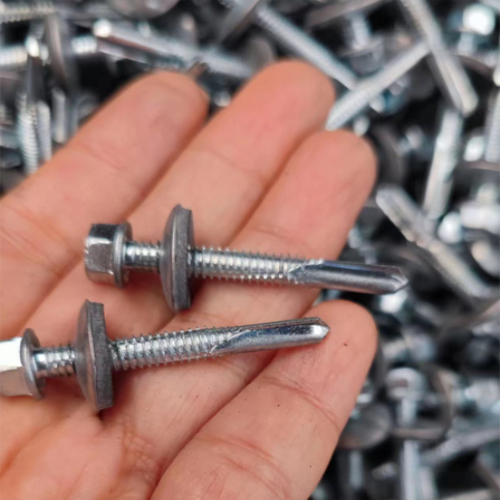
Understanding the USS (United States Standard) flat washer size chart begins with recognizing its role in distributing load. Washers serve as buffers, preventing damage to surfaces under stress from nuts and bolts. They also help in reducing friction during tightening, compensation for a hole that is too large, and sometimes even act as spacers. The uniformity provided by USS standards ensures that the washers meet specific dimensions, facilitating their use across various applications with predictable performance and reliability.
When navigating a USS flat washer size chart, attention to diameter measurements is key. These charts typically include the inner diameter, outer diameter, and thickness. The inner diameter, a critical value, must accommodate the bolt size it accompanies; commonly found sizes range from 6 to large diameters such as 1 1/2 inches. For instance, a 1/2 inch bolt demands a compatible USS washer that conforms to this measurement. This precision ensures a snug fit, minimizing slippage and enhancing the connection's durability.
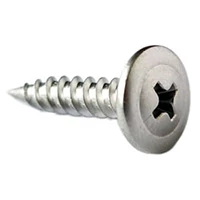
The outer diameter, while often overlooked, plays an equally important role. It must be sufficient to distribute the load effectively, preventing warping or deformation of the surface material. Generally, the larger the washer, the greater the load distribution, which is vital for softer or more malleable surfaces. Thickness, denoting the washer’s reliability under pressure, further influences how well the washer performs under compression. Typical USS washers exhibit a thickness range ensuring they can withstand various environmental and mechanical stresses without failure.
uss flat washer size chart
Beyond physical specifications, material selection weighs heavily in the evaluation process. Common USS washers are manufactured from materials such as stainless steel, zinc-plated steel, and brass. Each material choice carries specific benefits stainless steel offers excellent resistance to corrosion, making it suitable for outdoor or moist environments; zinc-plated variants are cost-effective with decent corrosion resistance for general applications; whereas brass adds anti-magnetic properties alongside corrosion resistance, ideal for electrical applications.
Implementing the correct USS flat washer size extends beyond matching numbers. Considerations must also include environmental conditions, intended load capacity, and potential galvanic corrosion scenarios when metals interact. For instance, while using a stainless steel washer on an aluminum surface, attention must be paid to potential electrochemical reactions that may induce corrosion. Awareness and understanding of these factors bolster one's ability to choose the most appropriate washer, ensuring long-term reliability and safety.
In the ever-evolving world of hardware components, staying informed about industry standards and advancements is imperative. Engaging with trusted manufacturers and suppliers can provide the latest updates and innovations within the field. Their expertise not only aids in making informed decisions but also cultivates a deeper understanding of the broader implications these small components have on projects large and small.
In conclusion, embracing the depth of the USS flat washer size chart is more than a technical exercise. It is a practice rooted in precision, reliability, and strategic decision-making. As interactions with washers, bolts, and nuts are an integral part of many mechanical systems, the knowledge woven into these seemingly minor choices can significantly influence project success. Ensuring a comprehensive approach to selection will drive performance and durability, reflecting a commitment to quality and excellence across diverse applications.