Tooth lock washers are essential components in many industrial applications, providing secure fastening solutions that prevent loosening due to vibrations or torque. With the demand for these washers increasing, it's crucial to understand their functionality, applications, and benefits.
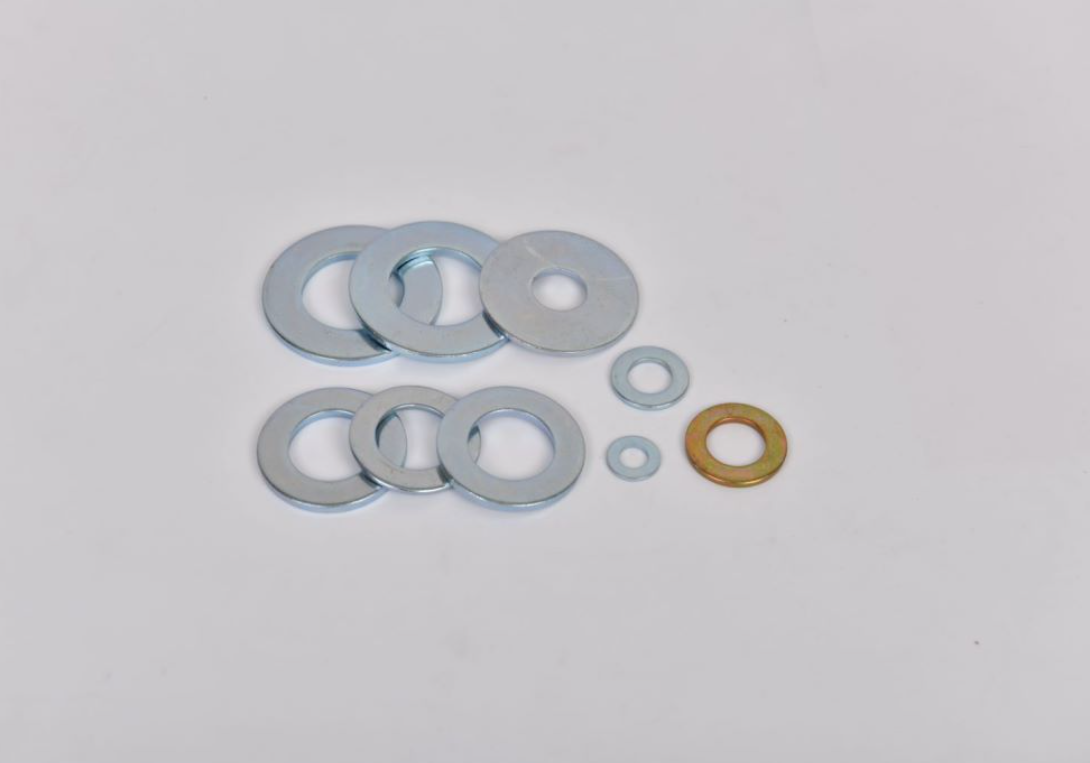
Drawing on years of experience in mechanical engineering, tooth lock washers have consistently delivered results when it comes to maintaining the integrity of assemblies. Their unique design, which includes teeth or serrations on one or both sides, allows them to create a locking effect through gripping and friction. This design ensures that when a bolt or nut is tightened against the washer, the teeth dig into the surface of the connecting parts, effectively preventing any rotational movement.
For those in industries where machinery operates under constant vibration, such as automotive manufacturing and heavy equipment production, tooth lock washers are non-negotiable. Their ability to maintain tight joints without the need for frequent maintenance makes them invaluable.
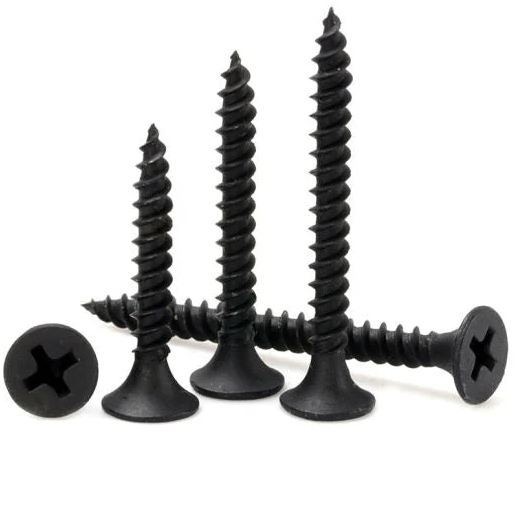
One of their most exemplary applications is in the automotive sector. Cars and trucks benefit from these washers due to their ability to withstand road vibrations, temperature changes, and mechanical stresses. Without them, components like engines, transmissions, and suspension systems would require constant checks and adjustments, leading to increased downtime and maintenance costs.
Considering their importance, selecting the right material for tooth lock washers is vital. Most are made from hardened steel or stainless steel, offering excellent strength and corrosion resistance. Applications exposed to saline environments, such as marine engineering, often rely on stainless steel variants to counteract potential rust and corrosion damage.
tooth lock washer
From a quality control perspective, tooth lock washers should undergo rigorous testing to meet industry standards, such as those set by ASTM or ISO. This ensures their performance under specified loads and tensions. Additionally, manufacturers often provide certifications and compliance sheets upon request, allowing users to verify their authenticity and suitability for use in sensitive machinery or where safety is paramount.
Using these washers properly also extends their lifespan and effectiveness. It's imperative that during installation, the correct torque specifications are adhered to. Over-tightening can damage the washer and underlying components, while under-tightening can result in ineffective locking, nullifying the washer's fundamental purpose.
In terms of expertise, engineers and mechanics often consult fastening experts to determine the best type of tooth lock washer for specific applications. Personalized advice might be necessary for custom or particularly demanding projects where failure is not an option.
In conclusion, the reliance on tooth lock washers across various industries underscores their effectiveness and reliability. As someone who prioritizes the extended functionality and safety of machinery, choosing the right washer and installing it correctly is paramount. Their role in fortifying the structure of machines is unparalleled, marking them as small components with significant impacts. Adopting high-quality tooth lock washers not only enhances operational efficiency but also assures safety and longevity, garnering trust from all stakeholders involved.