Structural flat washers, often overlooked in the realm of construction and assembly projects, play a pivotal role in various industries by enhancing both the integrity and longevity of structural assemblies. These seemingly simple components are anything but trivial, and their selection and application require a nuanced understanding that draws from engineering expertise and practical experience.
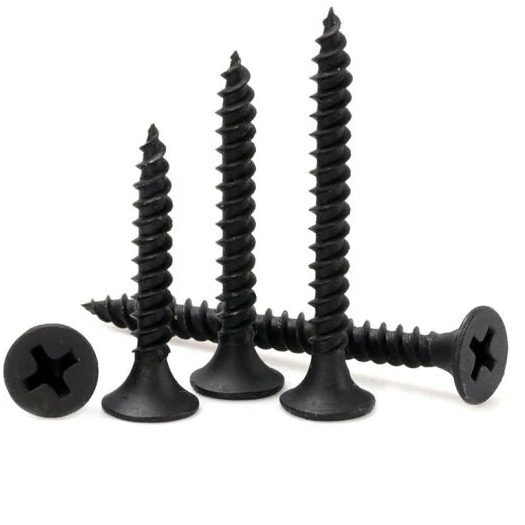
These washers are designed to evenly distribute the load of a threaded fastener, such as a bolt or nut, reducing the stress exerted on the joined materials.
This not only prevents damage and wear but also mitigates the potential for material deformation. The choice of material for a structural flat washer can significantly impact the efficacy of its application. Engineers and construction professionals tend to prefer washers made from stainless steel, owing to its high resistance to corrosion and ability to withstand harsh environmental conditions. This durability makes them ideal for marine, outdoor, and industrial applications where exposure to moisture and varying temperatures are commonplace.
Expertise in the domain of structural flat washers involves a comprehensive understanding of the interplay between the fastener system and the materials being joined. The correct sizing of a washer is crucial; it must complement the bolt size to optimize the distribution of force. Too small a washer may fail to protect the integrity of the hole, while an oversized washer can result in unnecessary material and weight cost, an important consideration in projects where weight is critical.
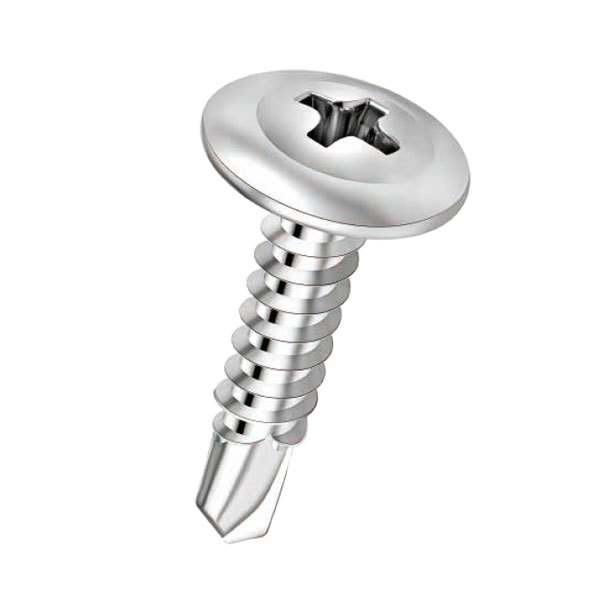
Furthermore, it is essential for engineers to be aware of the manufacturing standards governing these components. Compliance with ISO and ANSI standards ensures that structural flat washers possess the necessary mechanical properties, such as tensile strength and thermal resistance, to perform reliably under specified conditions. Engineers who have hands-on experience with building codes and industry standards can provide valuable insights into selecting washers that adhere to the relevant regulations, thus promoting safety and reliability in structural design.
structural flat washer
The authoritative use of structural flat washers extends to their role in vibration damping. When applied correctly, they can effectively reduce the transmission of vibrations between assembled parts, which is particularly advantageous in machinery that operates at high speeds or in environments where noise reduction is paramount. This application also underscores the importance of material selection, as rubberized or composite washers might be preferable for maximizing damping effects.
Increased trustworthiness in the supply of structural flat washers comes from engaging with reputable manufacturers who adhere to rigorous quality assurance protocols. Such manufacturers provide detailed product specifications, testing results, and material certifications, which are invaluable to project managers and procurement specialists aiming to make informed purchasing decisions. The integrity of a construction project often hinges on these seemingly minor components performing their role impeccably.
Real-world applications and case studies further illustrate the significance of structural flat washers. Consider their use in the aerospace industry, where each component must meet stringent safety standards. Here, engineers rely on their expertise in both materials and mechanical design to select washers that contribute to the overall structural integrity of an aircraft, ensuring safe and efficient operation. Similarly, in the automotive industry, structural flat washers are integral to assemblies where load distribution and vibration reduction are critical to vehicular performance and durability.
In conclusion, mastering the use of structural flat washers demands a balanced approach that marries practical experience with professional expertise. By understanding their material properties, sizing, application standards, and role in vibrational control, professionals can enhance the performance and safety of their structural projects. Whether deployed in high-stakes industries like aerospace and automotive or in everyday construction, these components are indispensable to achieving engineering excellence.