In the realm of fastening solutions, washers play an indispensable role in ensuring the security and longevity of connections. Spring washers and flat washers, featuring prominently in this category, are pivotal components within a myriad of applications. Their usage greatly enhances the functionality, safety, and durability of mechanical assemblies. A detailed exploration of these washers can provide critical insights for manufacturers, engineers, and DIY enthusiasts who strive for optimal performance.
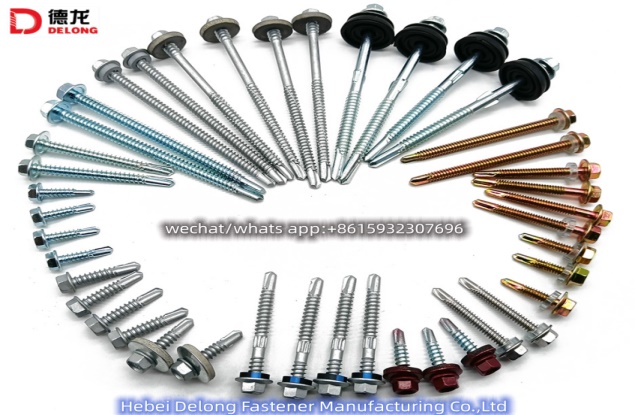
Spring washers, sometimes referred to as disc springs or Belleville washers, are engineered to provide a pre-loading force against the fastener head or nut. Their conical shape allows for deformation under load, which helps to prevent loosening caused by vibrations or dynamic loads. This essential characteristic makes them invaluable in automotive, aerospace, and industrial machinery applications where maintenance of tension is critical. In environments subjected to fluctuating forces, spring washers mitigate the risk of connection failures, thereby ensuring operational reliability and safety.
On the other hand, flat washers, the most ubiquitous type, serve to distribute the load of a threaded fastener, such as a screw or nut. By increasing the bearing surface area, flat washers protect the surface material from damage and reduce the chance of loosening due to surface expansion. Their role is vital in applications requiring uniform load distribution or where the surface integrity and material properties are of concern.

Both spring washers and flat washers excel in their areas of application but are often used in combination to complement each other’s strengths. For instance, in scenarios where vibration is present and load distribution is equally critical, stacking these washers can be a brilliant solution. The spring washer provides tension, while the flat washer ensures load distribution, offering a comprehensive fastening solution.
Understanding the nuances of material selection further reinforces the effectiveness of these washers. Spring washers crafted from high-tensile steel or stainless steel exhibit superior resistance to deformation, corrosion, and wear, thereby extending the lifecycle of the assembly. Similarly, flat washers made from materials compatible with their working environment – like brass, aluminum, or composite materials – enhance the longevity and functionality of the connection.
spring washer flat
The inclusion of washers, particularly spring and flat types, in a mechanical design is a testament to thoughtful engineering. Proper specification is crucial consideration of parameters such as washer size, material, thickness, and load capacity is vital for optimizing their function. Engineers and procurement specialists must collaborate closely to ensure washers meet specific operational requirements.
In practice, the consequences of incorrect washer selection can be dire. Misalignment, over-compression, or inadequate load distribution can lead to premature failure, necessitating costly repairs and downtime. Thus,
the choice of spring and flat washers should never be an afterthought. Prioritizing the quality and specification of these components is essential to maintaining the integrity and functionality of mechanical assemblies across industries.
For those seeking to deepen their expertise, reviewing case studies where washers played a crucial role in the success or failure of an assembly can be enlightening. Engaging with professional societies or industry forums dedicated to fastener technology can also provide ongoing education and updates on innovations in washer design and usage.
In conclusion, spring washers and flat washers stand out as fundamental elements in mechanical assemblies for their distinct yet complementary roles. By understanding their properties, applications, and the criteria for optimal selection, stakeholders can significantly enhance the performance, reliability, and safety of their projects. As the domain of fastening solutions continues to evolve, the precise application of these washers will remain a cornerstone of robust engineering practices, driving efficiency and innovation forward.