In the world of fasteners, choosing the right type of washer can make a significant difference in the stability and longevity of an assembly. Split lock washers and flat washers are two of the most commonly used types, each offering unique properties and benefits that cater to different applications. Understanding the difference between these washers and knowing when to use each can enhance both the performance and reliability of the fastened joint in any mechanical setup.
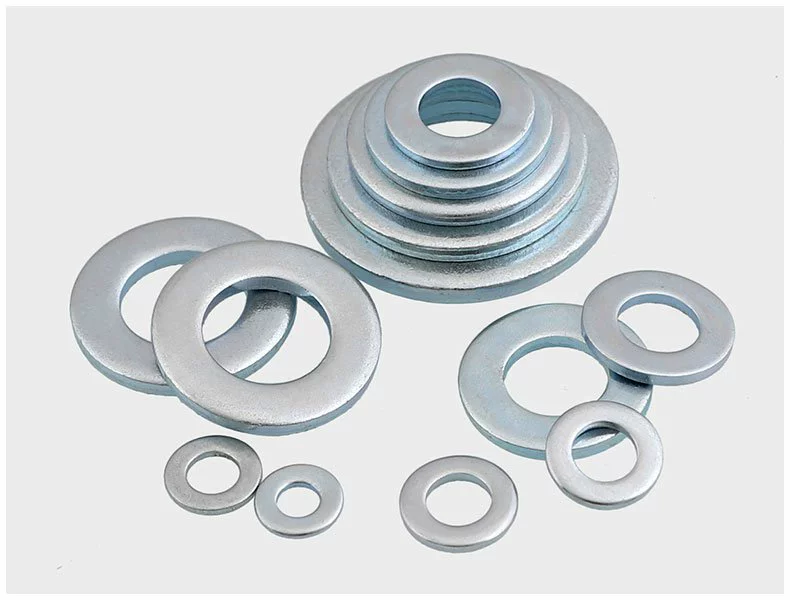
Split lock washers, often referred to as spring washers, are designed with a slight helical shape that allows them to act like a spring when compressed. This feature provides superior locking capabilities by creating a firm hold against the fastener's rotation during service conditions. When torque is applied to the nut or bolt, the split in the washer forces it to flatten slightly, increasing friction and reducing the chances of the fastener loosening due to vibrations or torque overload. These washers are ideal for dynamic environments where components are subject to constant vibration or movement such as in automotive engines and industrial machinery.
On the other hand, flat washers are simple, disc-shaped components with a central hole that fits over the shank of a bolt or screw. Their primary function is to distribute the load of the fastener over a larger area, reducing the risk of damage to the surface being fastened. Flat washers also provide a smoother and more even surface for the nut or bolt head, which can prevent marring and gouging of softer materials. This capability makes flat washers a preferred choice for applications where aesthetic considerations are vital or where materials with lower hardness are involved, such as in furniture assembly and electronic enclosures.

When deciding between a split lock washer and a flat washer for a particular application, several factors should be taken into account, including the environmental conditions and the specific requirements of the assembly. For applications where vibration resistance is crucial, and component loosening could result in catastrophic failure, split lock washers are the most suitable choice. These washers are particularly effective in scenarios where re-tightening fasteners is inconvenient or impractical.
split lock washer vs flat washer
Conversely, flat washers are preferable in scenarios where the main concern is protecting the surface of the material being fastened and ensuring even distribution of load. They are invaluable in assemblies where pressure applied by the fastener head or nut needs to be spread over a wide area to prevent embedment in the base material. Furthermore, for materials prone to corrosion or to chemical exposures, using stainless steel or other corrosion-resistant materials for flat washers can provide enhanced longevity, ensuring the structural integrity of the assembly is maintained over an extended period.
Professionals recognize that washers, though often small and overlooked components, play a pivotal role in the effectiveness and durability of a fastened joint. In particular industries like aerospace, automotive, and heavy machinery, the use of the wrong type of washer could potentially lead to system failures, highlighting the importance of informed decision-making in washer selection.
In summary,
when selecting between a split lock washer and a flat washer, it is vital to consider the specific demands of the application. While split lock washers offer exceptional locking strength ideal for high-vibration environments, flat washers deliver excellent load distribution and surface protection, crucial for maintaining the integrity of softer materials. By aligning the wash choice with the assembly's requirements, optimal performance, safety, and longevity are assured.