Self-tapping screw sockets stand as a testament to modern engineering innovation, embodying a perfect fusion of design simplicity and functionality. For industries ranging from construction to electronics, these unique components have revolutionized the way assemblies are constructed, offering both versatility and efficiency. Understanding the intricacies of self-tapping screw sockets involves a deep dive into their structure, usability, and material science, all of which contribute to their widespread adoption and trust in various applications.
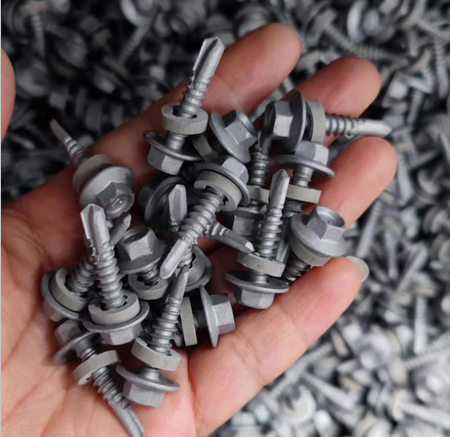
At the crux of self-tapping screw socket technology is their ability to form their own threads in materials such as plastic, metal, and wood. This self-tapping feature eliminates the need for pre-drilled holes, simplifying the assembly process and reducing the time required for installation. The sockets are designed with a tapering profile, which aids in cutting into the material and forming a compatible thread path. This characteristic is particularly beneficial in sectors where precision and speed are paramount, such as in the automotive and aerospace industries.
The expertise behind the manufacturing of self-tapping screw sockets lies in the choice of materials and the precision engineering involved. These sockets are typically crafted from high-grade stainless steel or carbon steel, materials chosen for their strength, durability, and resistance to corrosive forces. The manufacturing process involves heat treatment and surface hardening techniques, which enhance the socket's ability to withstand torque and shear forces, making them reliable under varying conditions.
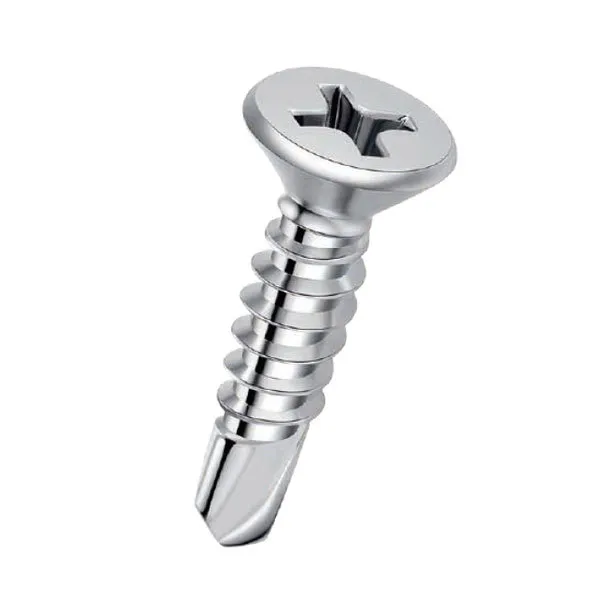
Moreover, the credibility of self-tapping screw sockets is evidenced by rigorous quality testing measures. Before reaching the market, these components undergo extensive testing for stress, fatigue, and endurance to ensure they meet industry-specific standards. Such authoritative testing not only certifies their performance but also provides users with assurance regarding their dependability, making them a trusted component in critical applications.
self tapping screw socket
Practical experience with self-tapping screw sockets highlights their versatility. In residential construction, they streamline the process of installing window frames and cabinetry, where reducing labor time without compromising on joint strength is crucial. Similarly, in electronic devices, where miniaturization is a trend, these sockets are instrumental, allowing for secure assembly of compact components. The user-friendliness of self-tapping screw sockets is enhanced by a wide range of sizes and designs available in the market, catering to diverse requirements.
Despite their numerous benefits, the implementation of self-tapping screw sockets requires careful consideration. Users must ensure compatibility with the material intended for use, as excessive force during installation can lead to material distortion or socket failure. Additionally, while the absence of pre-drilled holes saves time, precise alignment remains critical to maintain the integrity of the assembly.
The technology behind self-tapping screw sockets continues to evolve, adapting to emerging material science advancements and industry needs. Innovations such as coatings that provide increased corrosion resistance and lubricants that reduce installation torque further enhance their applicability and reliability.
In conclusion, self-tapping screw sockets are an exemplary product, utilizing engineering acumen to provide a solution that combines efficiency, reliability, and ease of use. Their widespread acceptance across various industries underscores their effectiveness, making them an indispensable component in modern assembly practices. As industries continue to push the boundaries of what is possible, the role of self-tapping screw sockets as a pivotal element in efficient and robust assemblies is set to grow, driven by ongoing advancements and a relentless pursuit of excellence.