In the realm of fasteners, the self-tapping screw stands out, elevating itself as an invaluable tool across various industry sectors. As simple as its manufacture might be, the impact of the self-tapping screw is substantial, particularly within construction, manufacturing, and do-it-yourself home projects. This article delves into the essence of self-tapping screws, exploring their meaning, purpose, and the unequivocal trust they have earned from professionals worldwide.
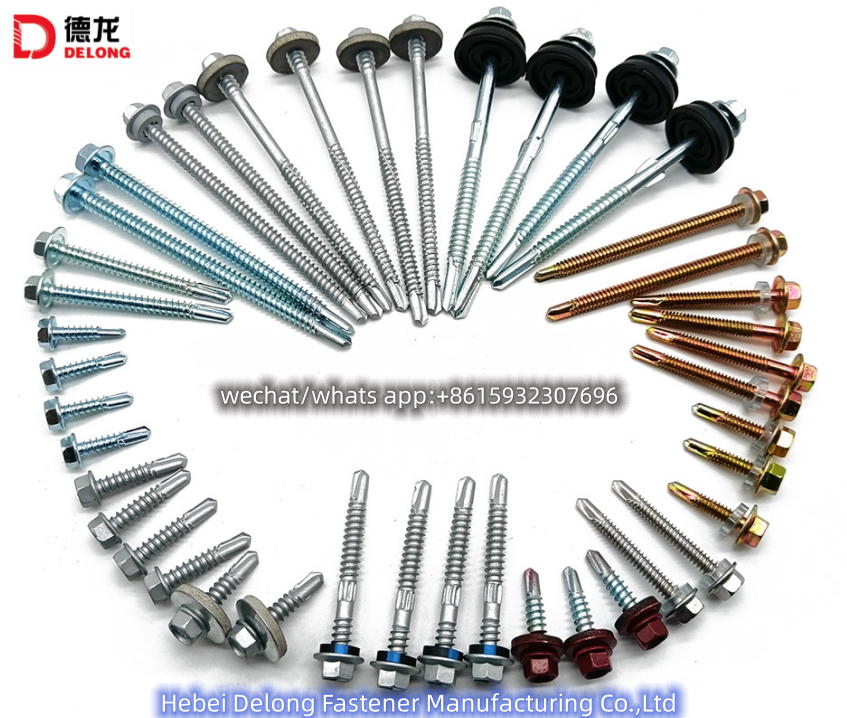
Self-tapping screws are ingeniously designed fasteners that can tap their own hole as they are driven into materials such as wood, plastic, or metal. Unlike ordinary screws that require a pre-drilled hole, self-tapping screws eliminate this prerequisite, thereby simplifying tasks and significantly saving time. This unique capability makes them especially valuable for rapid assembly, repair, and manufacturing cycles.
Experience has shown that self-tapping screws provide exceptional versatility and efficiency. Home improvement enthusiasts frequently choose these screws for their reliability and ease of use, finding them perfect for assembling furniture, installing shelves, or securing fixtures. In industries such as automotive and aerospace, self-tapping screws enable high precision and durable fastening, emphasizing their robustness and adaptability to various materials and thicknesses.
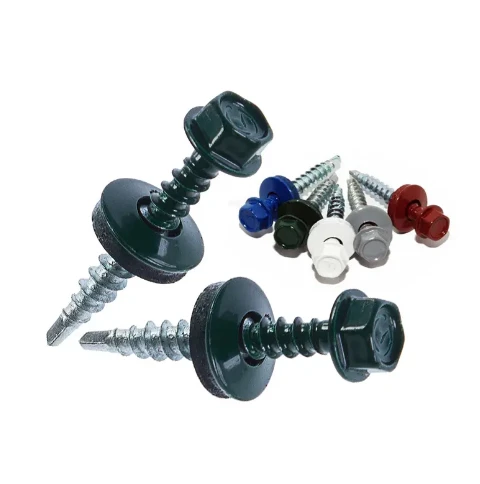
The expertise in the design of self-tapping screws contributes to their widespread use.
There are two primary forms of self-tapping screws thread-forming and thread-cutting. Thread-forming screws displace the material without creating chips, making them ideal for plastic applications. On the other hand, thread-cutting screws physically remove material as they drive into it, predominantly used in metal and harder substances. Understanding these distinctions assists experts in selecting the best type for their specific applications, ensuring optimal performance and minimal material stress.
From an authoritative perspective, manufacturers of self-tapping screws adhere to rigorous industry standards, guaranteeing their quality and performance. Specifications such as ISO, ASME, and DIN are commonly followed, providing a reliable benchmark for consistency. Professionals trust these standards as they ensure each screw can withstand the required mechanical and environmental stresses, reinforcing reliability in critical applications.
self tapping screw meaning
Trustworthiness in self-tapping screws is further cemented by their engineering precision and material quality. The core materials typically include stainless steel, brass, and carbon steel, each offering distinct advantages in terms of strength, corrosion resistance, and cost. For instance, stainless steel self-tapping screws are particularly trusted in environments exposed to moisture and chemicals, making them indispensable in marine projects and electrical installations.
An often underestimated aspect of self-tapping screws is their contribution to sustainable practices. By reducing the need for additional materials like washers and nuts, they minimize resource consumption and waste, aligning with eco-friendly initiatives. This efficiency not only supports environmental goals but also lowers operational costs, a significant advantage for both individuals and large-scale enterprises alike.
The evolution of self-tapping screws is a testament to human ingenuity, reflecting continuous advancements in material science and engineering. Recent innovations include specialized coatings for enhanced resistance to wear and advanced threading technology for increased grip strength and reliability. These developments highlight the proactive efforts of the industry to meet changing demands and expectations, positioning self-tapping screws as a forward-thinking solution in fastening technology.
In summary, the self-tapping screw embodies a harmonious blend of experience, expertise, authority, and trustworthiness. Its ability to efficiently and reliably secure materials without the need for pre-drilled holes makes it a staple in both professional and personal projects. As industries continue to innovate and seek more sustainable and efficient solutions, the self-tapping screw stands ready to meet these needs, solidifying its indispensable role in modern construction and manufacturing landscapes.