When embarking on any project that involves fastening materials together, self-tapping screws often become a builder’s best friend. Selecting the right head size is crucial not only for aesthetics but also for structural integrity and tool compatibility. This decision can be riddled with complexities, encompassing the type of material being fastened, the environment of the application, and the intended load-bearing requirements. This guide provides an expert’s insight into self-tapping screw head sizes, offering practical guidance based on expertise and real-world applications.
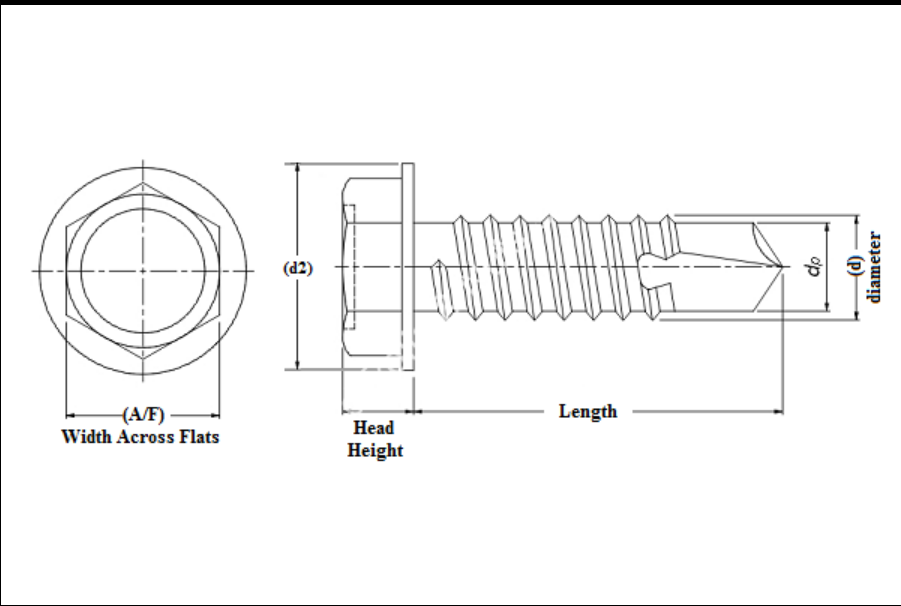
The fundamental premise of self-tapping screws rests on their ability to automatically tap a hole into the material as they are driven in. This eliminates the need for pre-drilling, significantly simplifying the construction process. Their efficiency and versatility make them indispensable in various industries such as automotive, aerospace, and even in everyday home improvement tasks.
The head size of a self-tapping screw is one of the first technical specifications that should be considered. It determines the distribution of load and pressure on the materials being fastened. A larger head size typically offers greater holding capacity, making it suitable for softer, thinner materials that may require more surface area to effectively distribute the force exerted. Conversely, smaller head sizes are favored for tighter applications or where a discreet, low-profile appearance is desired.
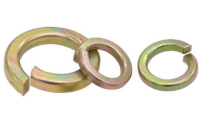
Flat head self-tapping screws are a staple when materials need to be flush against each other, such as in woodworking or drywall applications. These screws distribute force evenly, minimizing the risk of material splitting while maintaining a neat finish. Countersinking the screws ensures that the heads do not protrude, providing an aesthetic appeal while eliminating snag hazards.
Pan head varieties, however, are best suited for metal applications where lower-profile finishes are less critical. Their domed shape provides moderately distributed force, making them ideal for sheet metal work where the screw must hold without shearing or popping through under stress. The pronounced profile of the pan head grants added torque capacity, aiding in applications requiring robust fastening.
For engineers dealing with vibration-heavy environments, the hex head self-tapping screw is an optimal choice. Its design allows for maximal torque application during installation, ensuring a secure fixture that resists loosening over time. The hex head is prevalent in automotive applications, where durability against dynamic forces is paramount.
self tapping screw head size
Selecting the appropriate material of the screw itself also significantly impacts performance. Stainless steel screws, for instance, offer excellent corrosion resistance, making them suitable for outdoor and marine applications. However, for general indoor projects or in environments where moisture is not a concern, zinc-plated screws suffice, providing a cost-effective solution without compromising strength.
Trust in manufacturer specifications cannot be overstated. Reputable brands conduct rigorous testing and provide comprehensive data sheets that detail the exact measurements, load capacities, and appropriate applications, adding a layer of reliability to the selection process. This reliability is critical when dealing with projects where safety is a primary concern.
Further, always consult with industry standards and guidelines, such as those provided by the International Organization for Standardization (ISO) or American National Standards Institute (ANSI). These bodies establish testing protocols and size guidelines that help ensure screws perform adequately under defined conditions.
Real-world experience underscores the importance of adapting material selection and head size to the immediate demands of the project rather than adhering rigidly to preconceived notions of material suitability. Trial and error, as well as expert recommendations, are invaluable for honing an understanding of which head types and sizes work best under specific circumstances.
The vast array of available self-tapping screw head sizes can initially seem overwhelming. However, armed with knowledge about how each head type and size impacts performance, builders and engineers can make informed decisions that elevate the quality and durability of their projects. This expertise-backed approach ensures that each fastening task is completed with precision, safety, and efficiency, reinforcing the importance of selecting the optimal screw head size for every unique project.