The realm of fasteners is vast and varied, yet the self-tapping screw stands out due to its unique ability to create its own thread as it is driven into a material. This characteristic makes it indispensable in numerous applications, ranging from home improvement projects to industrial manufacturing processes.
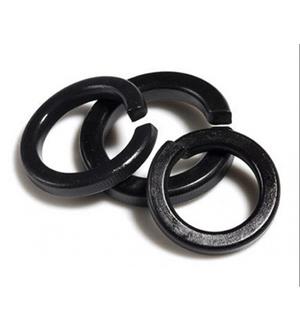
In practice, the self-tapping screw is favored for its incredible convenience and efficiency. Imagine working on a project that involves fastening two components together.
With a self-tapping screw, there is no need for a separate tapping or hole-threading operation. This reduces tool requirements, shortens preparation time, and minimizes potential errors during assembly. The screws are available in different types, including two categories thread-forming and thread-cutting, each suited for specific materials and uses.
Professionals across industries often share their expertise on using self-tapping screws effectively. For instance, when joining metal sheets, a thread-cutting screw is preferred for its ability to carve out precise threads, which are less likely to corrode over time. Similarly, for connecting plastic components, a thread-forming screw can prevent cracking by exerting even pressure as it embeds itself into the material.
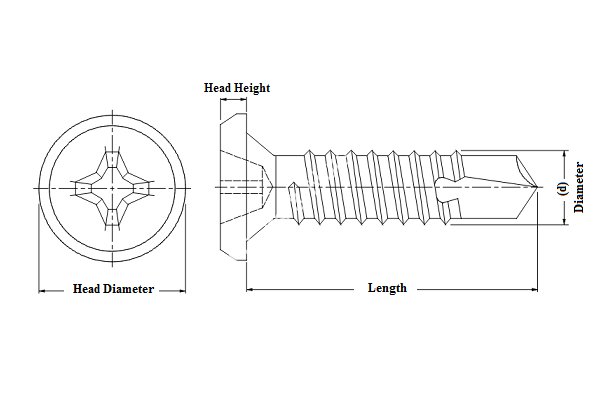
Despite their simple appearance, self-tapping screws embody significant engineering intelligence. Their design includes sharp, ridged threads and a pointed tip, aiding in efficient penetration and secure holding power. This intricate design is the result of years of research and development by manufacturers, ensuring they meet industry standards for safety, durability, and performance.
It's crucial for users to be aware of the diversity of materials and sizes when selecting self-tapping screws to best fit their requirements. These fasteners can be made from stainless steel, brass, or carbon steel, each material offering distinct advantages. For example, stainless steel screws are favored for their high resistance to rust and corrosion, making them ideal for outdoor applications or environments with high moisture content.
self tapping screw drawing
Trust in the quality of these fasteners can be reinforced by reviewing the certifications and manufacturing standards they comply with, such as ISO and ASTM. A reputable supplier will ensure their products meet these stringent standards, thus guaranteeing a high level of trustworthiness and reliability for your projects.
The advent of the digital era has further enhanced the accessibility of self-tapping screws. Several online platforms provide detailed catalogs and technical advice, simplifying the selection process. However, seasoned professionals, such as engineers and construction experts, often emphasize the importance of consulting technical datasheets and seeking expert advice to make informed choices.
Trusted brands in the fastener industry provide comprehensive guides and customer support to aid in selecting the appropriate screw for any application. Additionally, educational videos and tutorials online provide practical insights and hands-on methods to maximize the effectiveness and longevity of these screws.
Moreover, implementing the latest technological advancements in fastener production, such as surface treatments and heat-coating processes, can significantly enhance the performance of self-tapping screws. These innovations contribute to their durability and functional reliability, ensuring they meet the sophisticated demands of evolving construction and manufacturing landscapes.
Ultimately, the utility of self-tapping screws is marked by their adaptability, efficiency, and reliable performance across various settings. For anyone undertaking a project requiring secure fastening solutions, these screws demonstrate noteworthy efficiency and flexibility unmatched by other fastening methods. Whether you are an industry professional or a DIY enthusiast, understanding the application and benefits of self-tapping screws can significantly influence the success of your projects.