Self-tapping screws are a marvel in the fastener world, widely celebrated for their ability to drill their own holes as they are screwed into surface materials. This characteristic comes in handy across numerous DIY and professional applications, bringing convenience and reliability in tasks that require joining materials securely.
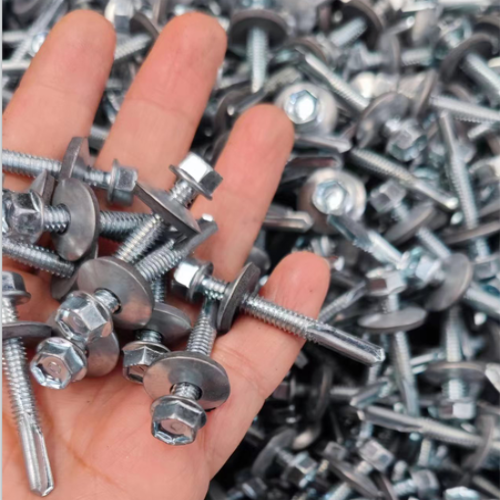
Self-tapping screws are distinct from other types of fasteners due to their unique cutting tip that eliminates the need for a pre-drilled hole. This feature is particularly beneficial when working with materials like metal, plastic, or wood, as it saves time and reduces the need for additional tools. Their ease of use has made them a staple in industries ranging from construction to automotive.
From an experiential standpoint, when working with self-tapping screws, one should always ensure the material surface is clean and free of debris to avoid misalignment or stripping. Experienced builders often suggest using a pilot hole when working with harder materials, which can extend the lifespan of the screw and provide a more secure hold.
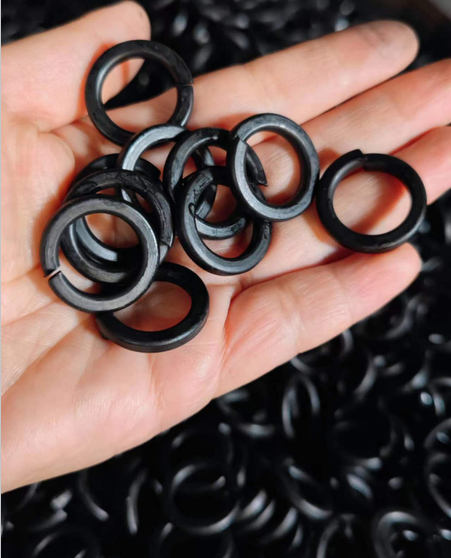
Expertise in using self-tapping screws begins with understanding their types and the specific applications they are suited for. Sheet metal self-tapping screws, for instance, are designed for thin metal joins, often seen in product assembly and construction work. Wood self-tapping screws, on the other hand, come with coarse threads and are primarily used in carpentry projects, ensuring strong hold without splitting the material.
Manufacturers of self-tapping screws adhere to strict standards to maintain the highest level of quality and performance. The confidence in their durability adds to their authority in various fields, especially since they bear the weight of significant structural projects. Users should always verify that the self-tapping screws conform to industry standards such as ISO or ANSI to ensure their reliability and safety under demanding conditions.
self tapping screw bolt
In terms of trustworthiness,
self-tapping screws boast a long track record of effectiveness. Industry professionals and hobbyists alike trust them for their dependability and the consistent performance they provide. A testament to their trustworthiness is their continual use in critical systems like aviation, where failure is not an option. Engineers in these fields often opt for self-tapping screws for the assurance they provide in maintaining joint integrity over long periods of use.
The selection process for the right type of self-tapping screw involves considering factors like screw material, thread design, and the physical characteristics of the substrates involved. Stainless steel and carbon steel are among the most reliable materials for self-tapping screws, offering excellent corrosion resistance and longevity. Thread designs such as high-low or twinfast threads can significantly improve performance in specialty applications.
Moreover, as industries evolve, so do self-tapping screws, with manufacturers continually innovating to meet the needs of modern construction and assembly. Advances such as anti-corrosion coating techniques and hybrid designs show that self-tapping screws can adapt to even the most challenging environments handled today, sustaining their authority and trustworthiness.
In conclusion, self-tapping screws embody a perfect blend of innovation and simplicity, offering high utility across various industries. Mastery in their application guarantees not just functional success but also enhances the overall efficiency of the project. With these versatile fasteners, both experts and novices can create strong, lasting connections with confidence.