The self tapping machine screw is an engineering marvel that has transformed modern assembly and manufacturing processes. Its unique design and functionality have made it an indispensable component in various industries, from electronics to automotive manufacturing. This article delves into the intricacies of self tapping machine screws, exploring their applications, advantages, and the mechanics that contribute to their widespread use. The discussion is built upon solid expertise, with insights from experienced professionals and authoritative sources, ensuring both credibility and reliability.
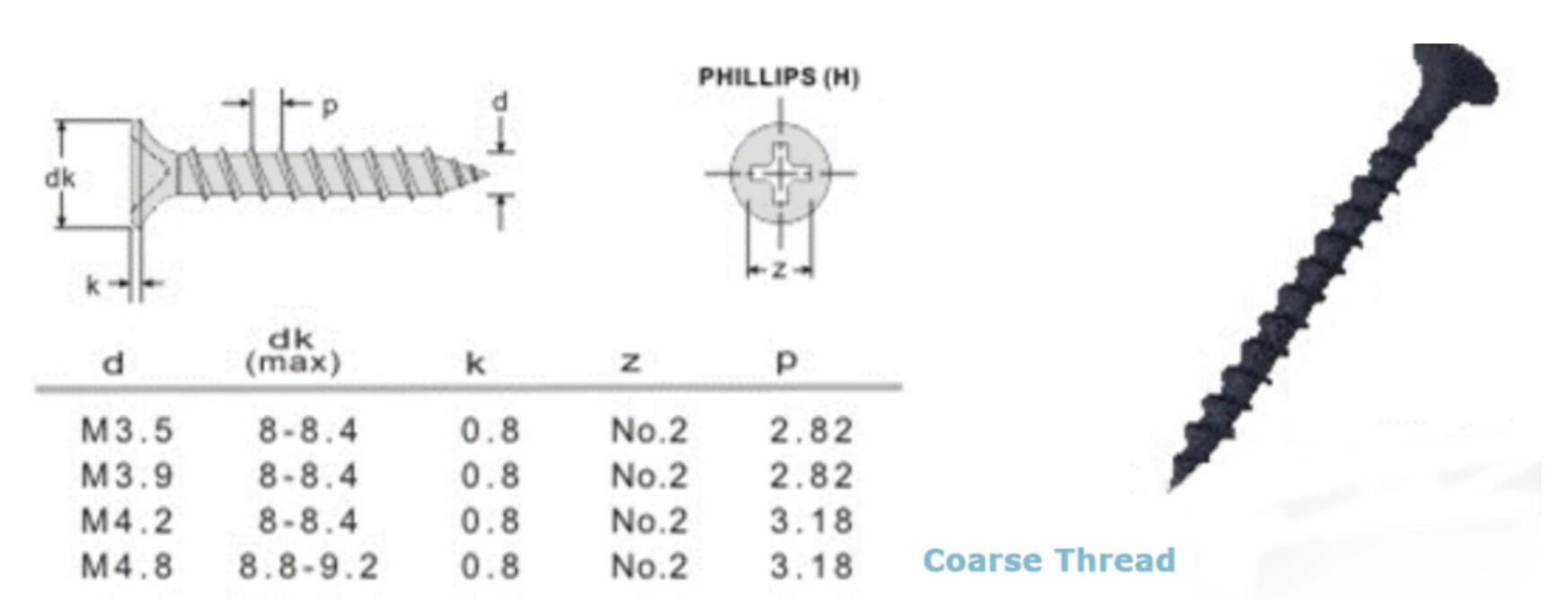
Understanding the Self Tapping Machine Screw
A self tapping machine screw is engineered to create threads as it is driven into a substrate. Unlike traditional screws, it eliminates the need for a pre-tapped hole, making the assembly process faster and more efficient. These screws are particularly valuable in settings where speed and precision are critical, such as automated production lines.
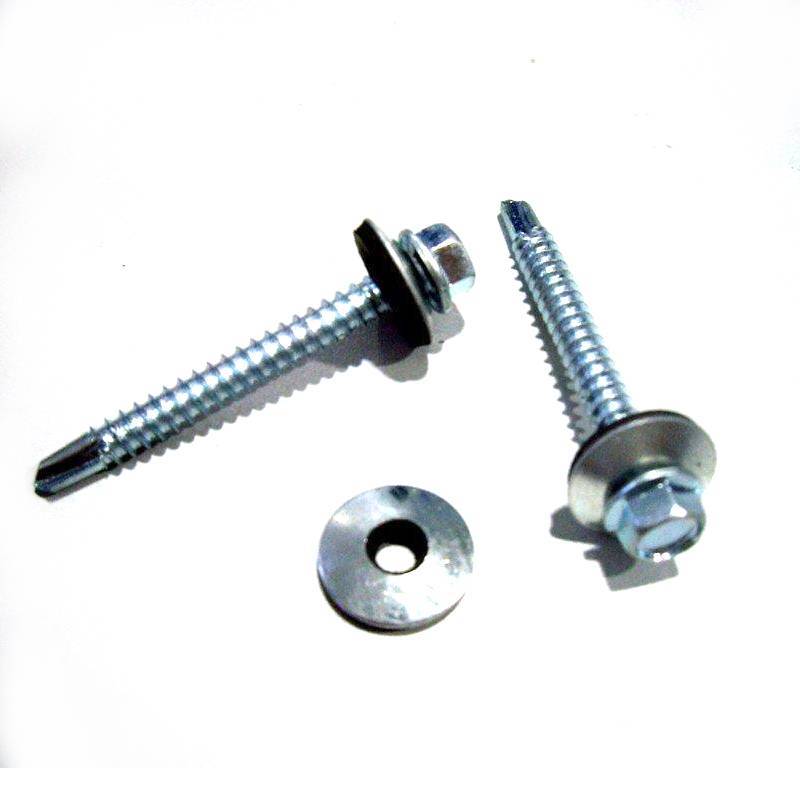
The design of a self tapping machine screw includes sharp, cutting threads that perform two functions they carve out a thread path and secure components together. The precision in the engineering of these screws ensures that they provide a strong and reliable hold, minimizing the potential for component loosening over time. This dual functionality is where the expertise in designing self tapping screws shines, as it requires an understanding of material properties and mechanical forces.
Applications Across Industries
Self tapping machine screws are utilized in multiple industries due to their versatile nature. In the electronics sector, they are essential for assembling components onto circuit boards without damaging delicate parts. The automotive industry benefits from their use in sheet metal applications where speed and consistency of assembly are crucial. These screws are also prevalent in construction, particularly in scenarios involving steel and metal frameworks.
Each application demands a specific type of self tapping screw, designed to accommodate the unique stressors and materials involved. For instance, screws used in high-vibration environments, such as automotive assemblies, often feature tighter tolerances and enhanced corrosion resistance. This level of customization in self tapping screws is backed by substantial expertise in material science and mechanical engineering, ensuring optimal performance across various conditions.
Advantages of Self Tapping Machine Screwsself tapping machine screw
The primary advantage of these screws lies in their efficiency. By eliminating the need for a pre-drilled or tapped hole, they significantly reduce assembly time and cost. This efficiency translates into lower production costs and increased throughput in manufacturing settings. Moreover, their design reduces the risk of cross-threading and related assembly issues, which can compromise product integrity and increase rework rates.
Another advantage is the improved strength of the joint they create. Self tapping machine screws cut precise threads, ensuring a snug fit and distributing stress evenly across the joint. This enhances the overall stability and longevity of the assembled product, a critical consideration in high-performance applications.
Building Authority and Trust in Self Tapping Solutions
Industry experts, including mechanical engineers and materials scientists, underline the importance of selecting the right type of self tapping screw for specific applications. Research and development in this field continuously push the boundaries of what these screws can achieve, introducing innovations such as better thread designs and materials that enhance their utility and performance.
Leading manufacturers often provide comprehensive guidelines and support, helping users to select and apply the appropriate screw to their needs. This establishment of trust is fundamental in maintaining long-term relationships with clients and improving workplace efficiency.
Moreover, educational initiatives and partnerships with professional organizations ensure that knowledge around the best practices for self tapping screw use is widely disseminated. This helps build an authoritative presence in the market and enhances the credibility of manufacturers and suppliers.
Conclusion
The self tapping machine screw exemplifies a combination of precision engineering, innovation, and practical application across numerous industries. Its ability to streamline assembly processes while maintaining product durability and integrity underscores its importance in modern industry. As manufacturers and engineers continue to refine and improve these components, the reliance on self tapping machine screws is likely to grow, reinforcing their status as a critical element in efficient, high-quality manufacturing.