In the world of fasteners, screw manufacturers play a pivotal role in ensuring that the intricate machinery, towering skyscrapers, and even the smallest household gadgets function seamlessly. With decades of industry expertise, these manufacturers have optimally combined cutting-edge technology with time-tested techniques to produce screws that meet diverse application demands.
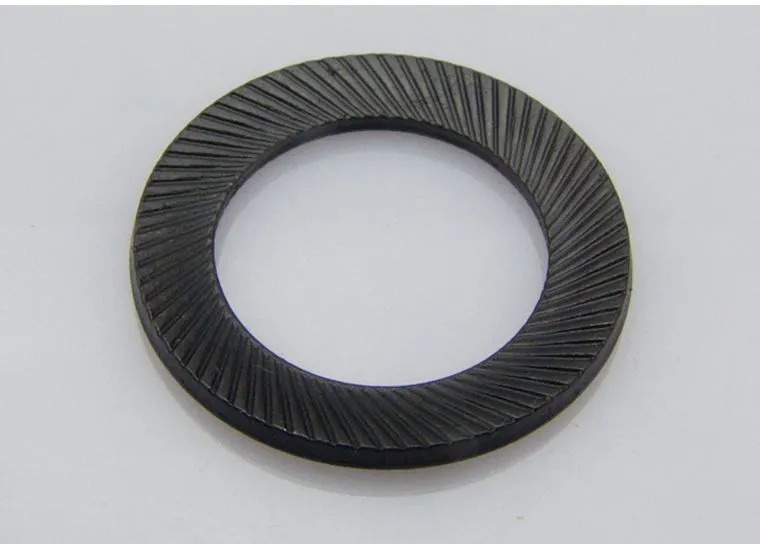
Screws, though seemingly simple, are the result of intricate engineering and design. Engineers and craftsmen in screw manufacturing facilities work diligently to ensure each screw meets rigorous quality standards. This level of precision not only demands expertise but a commitment to excellence that can be observed in every aspect of production—from material selection to the final product.
The selection of raw materials is the first cornerstone of producing a superior screw. High-quality steel, stainless steel, and other alloys are meticulously chosen based on the screw's intended application, ensuring the finished product can withstand environmental stresses like moisture, heat, and pressure. Manufacturers utilize advanced metallurgical testing to confirm that materials align with specified mechanical properties.
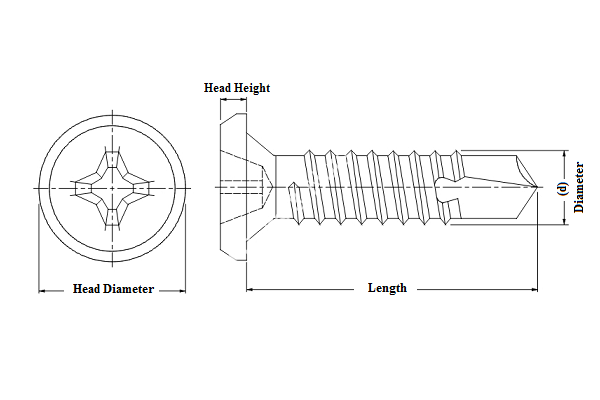
Precision engineering is at the heart of screw production. With automated, high-precision CNC (Computer Numerical Control) machines, manufacturers can design screws to exact dimensions, adhering to international standards such as ISO, DIN, and ANSI. This automated precision ensures uniformity across batches, a critical factor for industries that require reliable and consistent performance from their fasteners.
Manufacturers not only innovate in the realm of design but also invest in state-of-the-art manufacturing processes. Cold heading and threading are two primary methods used, each with specific advantages depending on the screw's required characteristics. Cold heading, for example, offers greater strength and durability, making it ideal for industrial applications. Meanwhile, advanced threading processes ensure optimal grip and fastening efficiency, reflecting the manufacturer’s expertise in pairing process with purpose.
screw manufacturer
Quality assurance is another domain where screw manufacturers demonstrate their authority in production.
Detailed inspections and rigorous testing are mandatory at every stage. This includes hardness tests, tensile strength assessments, and coating adherence checks, ensuring that each screw not only meets but exceeds customers' expectations. This commitment to quality reassures clients of the manufacturer's reliability and reinforces trust in their products.
Furthermore, screw manufacturers are increasingly focusing on sustainable production practices. By reducing waste, limiting emissions, and utilizing renewable energy, they are setting new benchmarks in environmentally responsible manufacturing. These efforts underscore their leadership in the industry by prioritizing the planet alongside their products.
For those seeking a trusted partner in the fastener market, selecting an experienced and reputed screw manufacturer is crucial. Recognizing the manufacturer’s expertise and commitment to quality not only guarantees high-performance screws but also ensures a seamless supply chain that is integral to any project's success. Opt for a manufacturer that exemplifies excellence, with a proven track record of innovation and trust—a partner who stands at the forefront of the fastener industry.
In conclusion, the production of screws is far more complex and demanding than it might initially appear. Successful screw manufacturers couple their profound industry experience with a meticulous focus on quality and sustainability to produce products that clients can trust. As a vital component of countless applications worldwide, their authority and professionalism set the standard for fastener manufacturing globally.