In the world of mechanical assemblies, the proper installation of lock washers is a critical element that often goes unnoticed. These small components play a pivotal role in ensuring the structural integrity of countless mechanical applications. Lock washers are designed to prevent nuts and bolts from slipping or loosening due to vibration or torque. Understanding how to properly install these washers involves technical knowledge and practical experience, which are essential to achieving optimal performance in any assembly.
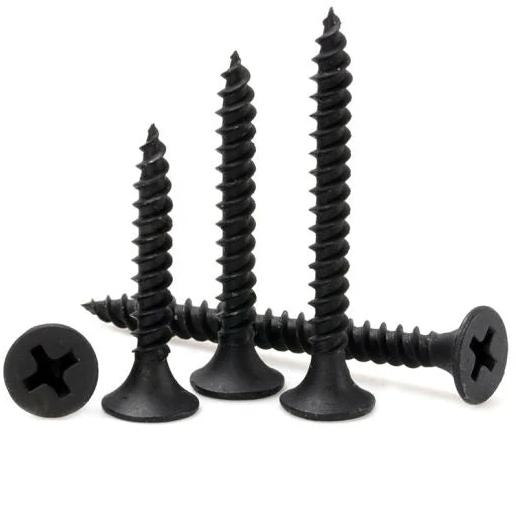
Selecting the right lock washer is the first step to successful installation. Lock washers come in various types, including split, tooth, and flat washers, each serving different purposes based on the type of material and assembly conditions. Split lock washers, for example, are commonly used in applications where vibrations are at play, as they provide a spring action that holds fasteners tight. Tooth lock washers, on the other hand, have inner or outer teeth that bite into the surface, making them ideal for softer materials. Identifying the correct type for your specific project is crucial to ensure maximum stability and reliability.
Before installation, the surface and threads of both the bolt and the nut must be clean and free from rust or debris. Surface contaminants can compromise the bond between the lock washer and the material, diminishing its ability to perform effectively. Additionally, using a lubricant might be necessary to ease the movement but should be used sparingly to avoid undermining the friction that lock washers rely on.
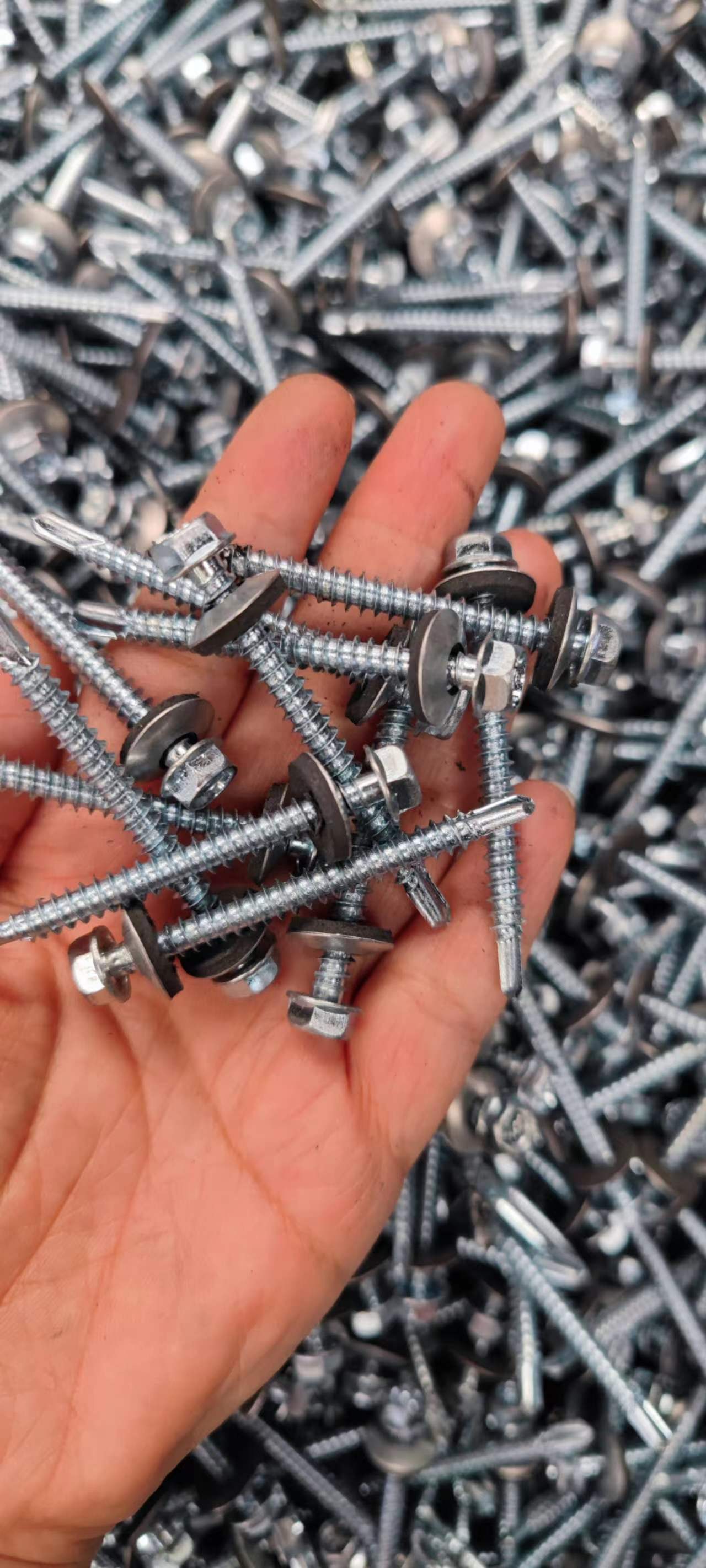
Aligning the washer correctly is another essential factor. For split lock washers, they should be placed directly beneath the nut, engaging the fastener fully to provide the counter-pressure needed to resist loosening forces. In contrast, tooth lock washers should have their teeth facing the material to maximize grip. When using these in electrical applications, the orientation becomes even more critical, as the washer may also need to provide a grounding path.
proper lock washer installation
While installing lock washers, the torque applied to the bolt and nut should be carefully controlled. Over-tightening can flatten or break the washer, while under-tightening might lead to a loose connection that fails under vibration or external force. It’s essential to consult the manufacturer’s specifications for the recommended torque settings, a practice that showcases the importance of combining industry standards with practical expertise.
After the installation, performing a quality check ensures that the washers are seated correctly and the assembly is secure. This procedure is not merely a formality but a crucial step in ensuring safety, especially in critical applications such as aerospace or automotive industries where failures can have catastrophic consequences. Regular maintenance checks should also be planned to inspect the condition of the lock washers and the tightness of the assembly, which are indicators of ongoing efficacy.
In recent years, advancements in technology have led to the development of lock washers with enhanced properties. Innovations such as washers with integrated sensors to monitor tension and vibrational forces in real-time are increasingly gaining popularity. These intelligent washers provide valuable data that can be analyzed to preemptively address issues, an example of how technology drives the evolution of such minute yet significant components.
Ultimately, the proper installation of lock washers requires a blend of expertise, experience, and adherence to best practices. By focusing on these elements, one can ensure that mechanical assemblies remain reliable and secure over their operational lifespan. As industries continue to demand higher levels of precision and performance, the importance of understanding and mastering the art of lock washer installation becomes ever more significant in guaranteeing the dependability and longevity of critical mechanical systems.