Selecting the appropriate size for a metric self-tapping screw hole is a critical consideration in many mechanical and construction projects. An incorrect size can lead to weak joints or even catastrophic failure of the assembly. Understanding how to determine the correct size hole for your self-tapping screw can save time, materials, and money.
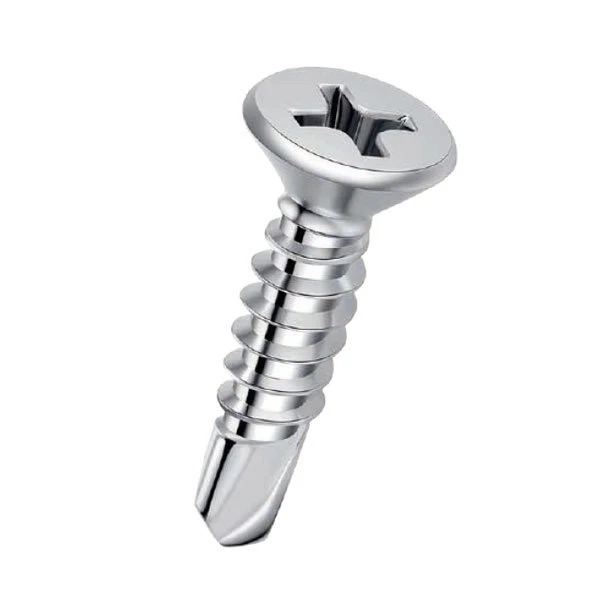
A metric self-tapping screw is a type of fastener designed to tap its own hole as it is driven into the material. This eliminates the need for a pilot hole, although a smaller guide hole is usually necessary to ensure the screw aligns properly with the material's grains and textures. This self-tapping ability is particularly beneficial for rapid assembly and when working with materials like metal, wood, and plastic.
The size of the hole is directly related to the size of the self-tapping screw. Firstly, manufacturers provide size designations in metric measurements, defined by the screw's diameter and thread pitch. The thread pitch refers to the distance between threads and is crucial in ensuring the screw maintains a grip on the material.
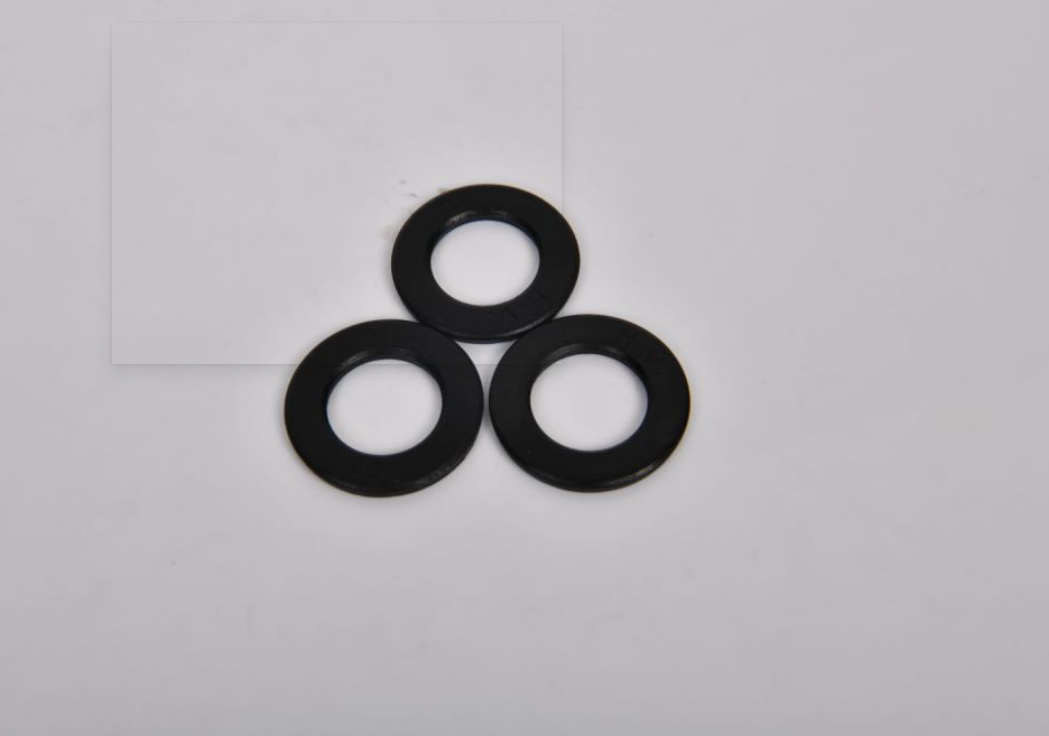
The rule of thumb for calculating the hole size for a metric self-tapping screw involves considering 85-95% of the screw’s diameter. This ensures that enough material remains for the threads of the screw to bite into, thus providing a strong hold. For example, if using an M3 self-tapping screw (3mm in diameter), the guide hole should be approximately 2.55mm to 2.85mm. This allows the screw to tap effectively without fracturing or splitting the material.
Empirical testing is a valuable step if guidelines are unclear or materials behave unpredictably. Different materials have varying responses to the pressure a self-tapping screw exerts. For softer materials like wood or soft plastics, you might lean towards a smaller diameter hole, around the 85% mark, to ensure a firm grip. Hard materials like aluminum or hard plastics could benefit from a larger initial hole closer to the 95% mark to aid the screw in cutting its threads without too much resistance, which might otherwise cause cracks or chips.
metric self tapping screw hole size
Another factor to consider is the screw's intended load capacity. For applications requiring higher load strength, ensuring the self-tapping screws are fully engaged in their respective holes is essential. As the depth of engagement increases, so does the holding power of the screw, making it less prone to stripping or pulling out. This requires a precise balance between the hole size and the screw diameter to optimize the grip.
Beyond theoretical calculations, practical considerations such as the tool used for driving the screw and the material's environmental conditions should not be overlooked. Using the correct torque settings on power tools prevents over-tightening, which can strip the threads and damage the seating material.
Industry standards and manufacturer guidelines are invaluable resources. Many manufacturers offer comprehensive charts that provide detailed recommendations for hole sizes based on material type and mechanical application. Adhering to these specifications not only can improve the efficacy of the assembly but also extend the lifespan and safety of the construction.
In fields like construction, automotive, and electronics where the reliability and strength of the build are non-negotiable, having a deep understanding of the nuances of hole size selection is indispensable. Consulting with material scientists or mechanical engineers can further increase the success rate of your installations. Awareness of evolving material technologies also plays a significant role in determining the best practices for using self-tapping screws.
Ultimately, the goal is to achieve a balance where the self-tapping process does not compromise the integrity of the material, instead reinforcing it. Knowing the right hole size for a metric self-tapping screw is not just about optimizing performance but also about enhancing safety, durability, and cost-efficiency in all your projects.