Self-Tapping Masonry Screws A Comprehensive Manufacturer's Guide
In the realm of construction and masonry work, self-tapping screws are a versatile and indispensable tool. These screws, designed with a thread that cuts its own path into the material, offer a quick and efficient solution for attaching various components to masonry surfaces. This article aims to provide a comprehensive guide for manufacturers, detailing the intricacies of self-tapping masonry screw production and highlighting the key considerations that must be taken into account.
**Material Selection**
The first and foremost aspect of self-tapping masonry screw manufacturing is the choice of material. Stainless steel is the most popular choice due to its corrosion resistance and durability, making it ideal for outdoor applications. However, other materials such as carbon steel or brass can also be used depending on the specific requirements of the product. The material should be selected based on factors such as the intended use, environmental conditions, and cost constraints.
**Thread Design**
The thread design of self-tapping masonry screws is crucial for their performance. The thread should have a sharp and aggressive cutting edge to facilitate easy penetration into the masonry material. The pitch and depth of the thread should also be optimized to ensure maximum holding power without causing the screw to strip out. Additionally, the thread should be designed to prevent debris from clogging the screw during installation.
**Head Design**
The head design of self-tapping masonry screws plays a significant role in their usability. A flat head with a Phillips or square drive recess is commonly used as it provides a large contact area for driving tools and reduces the risk of cam-out A flat head with a Phillips or square drive recess is commonly used as it provides a large contact area for driving tools and reduces the risk of cam-out
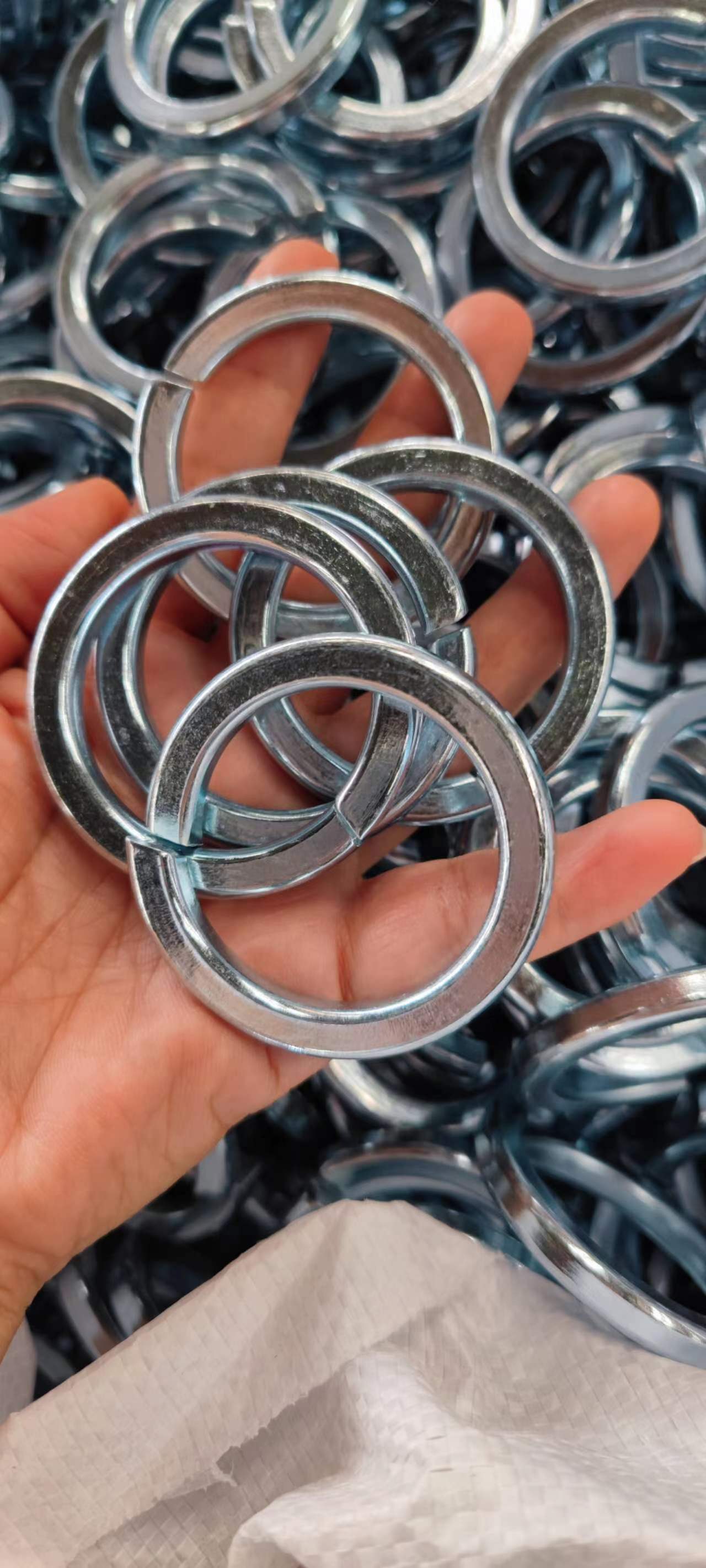
A flat head with a Phillips or square drive recess is commonly used as it provides a large contact area for driving tools and reduces the risk of cam-out A flat head with a Phillips or square drive recess is commonly used as it provides a large contact area for driving tools and reduces the risk of cam-out
self tapping masonry screw manufacturers. Other head styles such as hex or socket head screws may also be used depending on the specific requirements of the application. The head should be designed to withstand high torque loads without stripping or damaging the surrounding material.
**Manufacturing Process**
The manufacturing process for self-tapping masonry screws typically involves several steps, including cutting the raw material, forming the threads, cutting the head, and applying any necessary coatings or finishes. Advanced machinery and precision tools are essential for achieving the required level of quality and consistency in the final product. Automated processes such as screw machining or cold heading can increase productivity and reduce costs associated with manual labor.
**Quality Control**
Quality control is a critical aspect of self-tapping masonry screw manufacturing. Regular testing and inspection of raw materials, finished products, and production processes are necessary to ensure compliance with industry standards and customer requirements. Non-destructive testing methods such as x-ray or ultrasonic testing can help identify potential defects or inconsistencies early in the production process.
In conclusion, self-tapping masonry screws are a versatile and valuable addition to any manufacturer's product line. By carefully considering material selection, thread design, head design, manufacturing process, and quality control, manufacturers can produce high-quality screws that meet the demanding requirements of the construction industry.