M8 self-drilling screws, commonly known as self-tappers, are indispensable in both professional and DIY construction projects due to their unique ability to drill their own pilot holes as they are driven into materials. With an emphasis on functionality, efficiency, and reliability, these screws stand out in various applications, from industrial construction to home renovations.
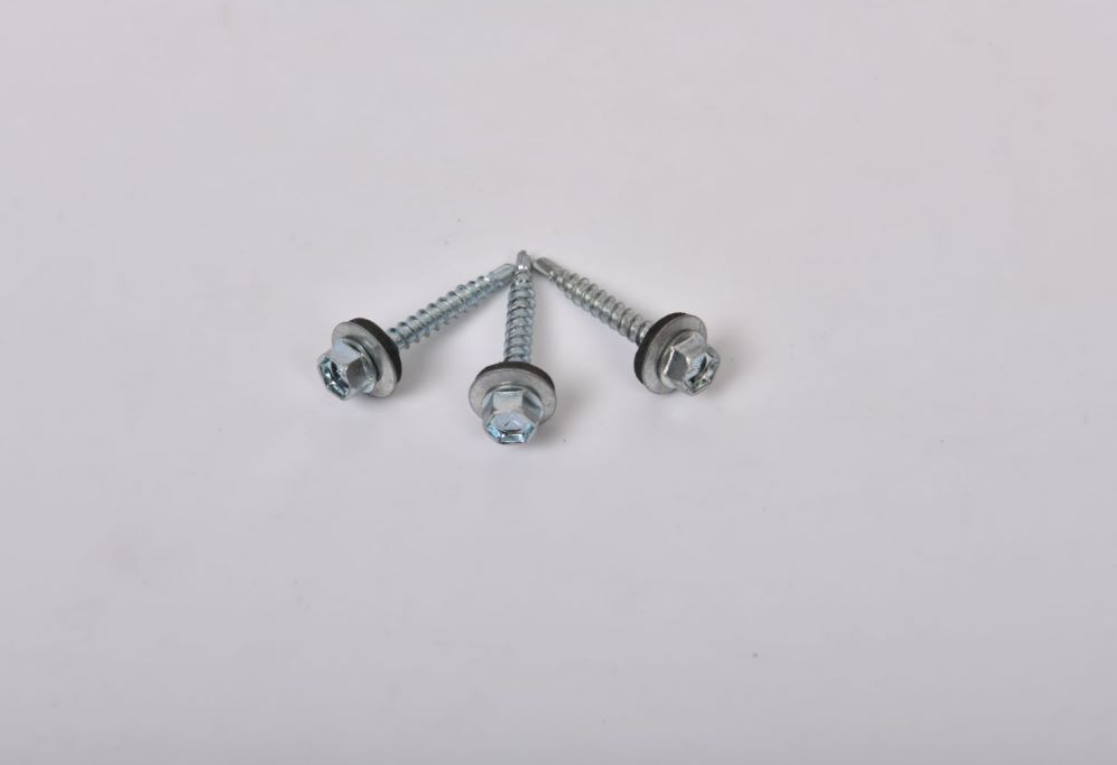
In the realm of hardware,
the design of the M8 self-drilling screw exemplifies precision engineering. These screws feature a drill-shaped point that gives them their defining ability to penetrate surfaces such as metals, wood, and plastic without the need for a pre-drilled hole. This functionality not only saves time but also minimizes the likelihood of material damage—a common setback when dealing with pre-drilling.
One of the most compelling advantages of using M8 self-drilling screws is their contribution to the integrity and strength of the assembly. When these screws are driven into metal, for example, they form tight, lasting bonds that are resistant to loosening due to vibrations. This characteristic is crucial in automotive and aerospace applications, where maintaining structural integrity is paramount.
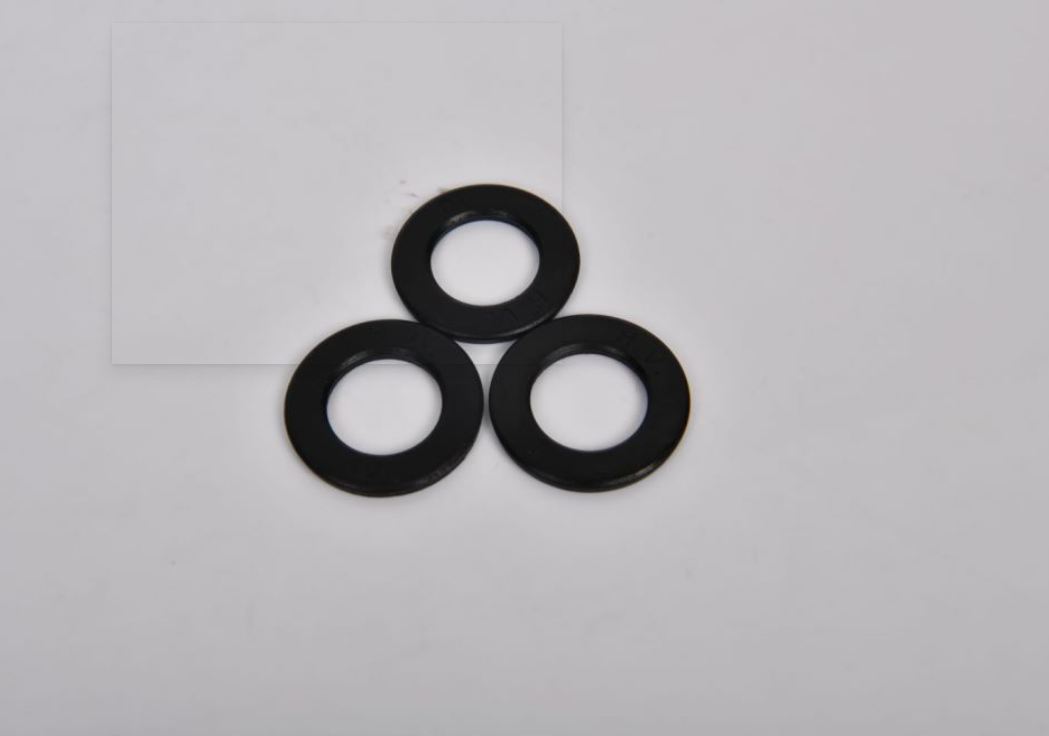
Further corroborating the reliability of M8 self-drilling screws is their construct of high-grade materials. Typically manufactured from hardened steel, sometimes coated with zinc or other corrosion-resistant materials, these screws boast a long lifespan even in environments prone to rust and wear. This resistance extends their use to outdoor projects and installations exposed to the elements.
From the perspective of professionals who have worked extensively with M8 self-drilling screws, their efficiency in rapid installations is unmatched. Contractors and engineers alike appreciate the reduction in tool necessities—eliminating the need for separate drill bits not only simplifies the process but also streamlines the workflow significantly. As such, projects are completed faster and with fewer resources, optimizing labor costs and resource allocation.
m8 self drilling screw
Another remarkable element is the wide range of applications where M8 self-drilling screws are employed. In construction, they are used to fasten together frames and panels and attach cladding and roofing systems that require robust anchoring. The automotive industry relies on them for assembling parts that demand high precision and strength. Even in the realm of renewable energy, these screws are pivotal in securely assembling and maintaining solar panel systems, where precision and durability are non-negotiable.
The expertise surrounding M8 self-drilling screws extends into the robust testing and quality assurance processes they undergo before hitting the market. Manufacturers often adhere to stringent standards to ensure that each piece meets both safety and performance requirements. This standardization not only guarantees effectiveness but also aligns with the industry's reliability protocols—giving engineers and builders confidence in their tools of choice.
As for trustworthiness, manufacturers of these screws often provide certifications and detailed specifications, allowing users to make informed decisions based on factual data. This transparency, coupled with widespread availability through trusted suppliers, means that consumers can access M8 self-drilling screws as required without concerns about quality inconsistency.
In conclusion, as construction technology evolves, M8 self-drilling screws remain at the forefront due to their distinct attributes. The expertise encapsulated in their design, backed by rigorous quality assurance and verified by industry professionals, underpins their status as a staple in construction and assembly ventures. Their ability to bridge efficacy with durability ensures that they will continue to play a pivotal role in innovation and application in various sectors. Therefore, investing in M8 self-drilling screws translates to investing in reliability, efficiency, and progress in construction endeavors.