For businesses and hobbyists dealing with the assembly of plastic components, the M2 self-tapping screw has emerged as an indispensable asset. Navigating the complexities of fastener selection can be daunting, especially when working with softer materials like plastics. Understanding the unique characteristics of M2 self-tapping screws for plastic offers invaluable insights and ensures success in both production efficiency and end-product durability.
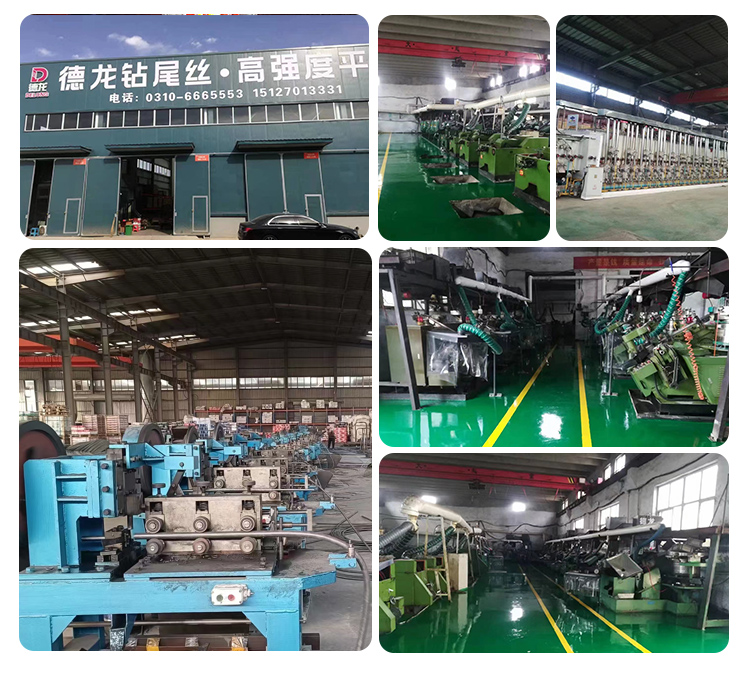
M2 self-tapping screws designed specifically for plastic applications are engineered to conquer the challenges associated with assembling thermoplastic and thermoset materials. One pivotal distinction of these screws is their thread design, which significantly minimizes stress concentration during insertion. Traditional screws, when used in plastic, often lead to cracks, stress fractures, or substrate deformation due to incompatible thread profiles. M2 self-tapping screws, however, feature specialized threads that distribute load evenly and facilitate smooth penetration without compromising the integrity of the plastic.
The precision of these screws stems from meticulous engineering that takes into account the various mechanical properties of plastics. Different plastics exhibit diverse levels of hardness, tensile strength, and thermal expansion. M2 self-tapping screws cater to this diversity by incorporating thread angles and point geometries that adapt to the substrate material. The sharp point of the M2 screw initiates a clean cut into the plastic, while a gradual thread taper prevents excessive radial forces that can cause splitting. Such nuanced design reflects an expert understanding of material science that sets these screws apart in the domain of fastener technology.
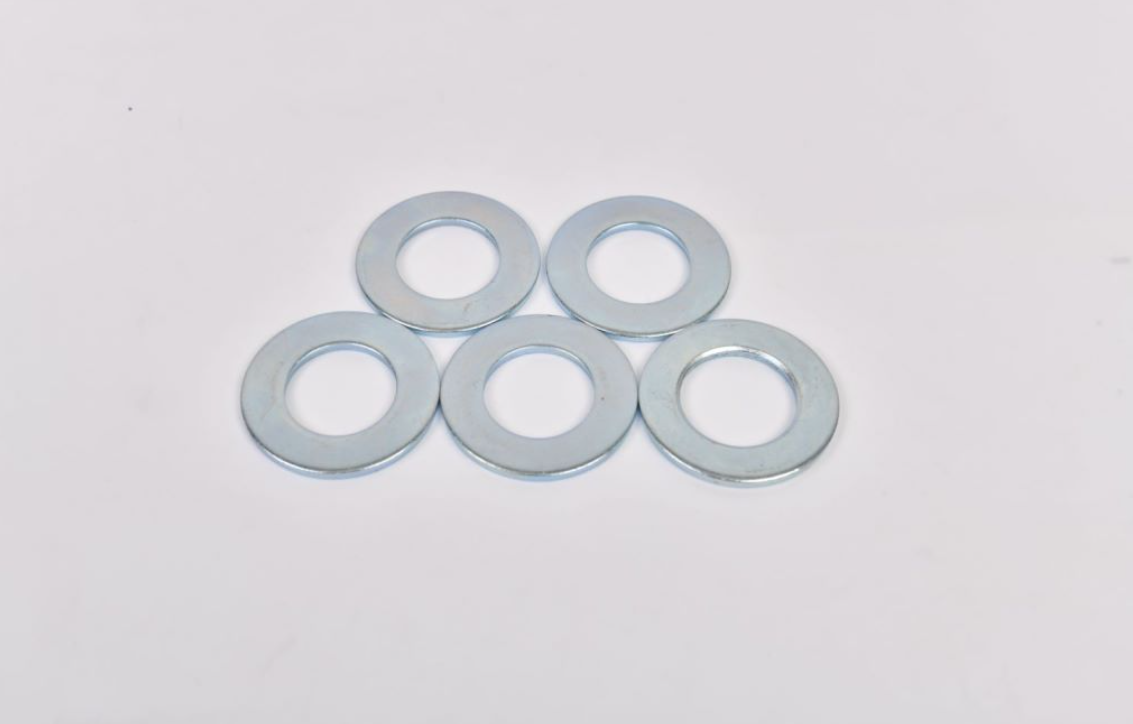
An essential aspect of their expertise is the screws' ability to self-create mating threads upon installation. This not only reduces the need for pre-drilled pilot holes but also accelerates the assembly process, enhancing production speed without sacrificing connection quality. The automatic thread formation maximizes engagement and pull-out resistance, assuring a steadfast hold that can withstand operational stresses and environmental influences. This feature emphasizes their reliability and promotes trust in scenarios where long-term performance is non-negotiable.
m2 self tapping screw for plastic
Moreover, the authoritativeness of M2 self-tapping screws for plastic is underscored by rigorous testing and compliance with industry standards. Manufacturers subject these screws to extensive evaluations, measuring torque, shear strength, and environmental resilience to ensure they meet stringent guidelines. Such adherence to standards reassures users of their dependable application across various industries, from consumer electronics to automotive components.
Drawing from genuine experiences, practitioners consistently report on the versatility and efficacy of M2 self-tapping screws. Testimonials from assembly line workers and engineers highlight a decrease in production time and an increase in joint reliability, attributes that translate directly into cost savings and enhanced product longevity. The positive feedback underscores their preferred status among materials specialists who value not only the immediate tactical benefits but also the strategic implications of reduced maintenance and improved safety margins.
In closing,
the utilization of M2 self-tapping screws for plastic illustrates the blend of sophisticated engineering and practical application. Their specialized design ensures a robust engagement with plastic components, mitigating traditional challenges and enhancing overall assembly quality. These screws exemplify a commitment to excellence and authority within the fastener industry while fostering trust among users who demand the pinnacle of performance and reliability. As products increasingly incorporate plastic elements, employing M2 self-tapping screws becomes not just an option but a strategic necessity for anyone devoted to engineering excellence and product integrity.