Lock washers and flat washers, often overlooked but critical components in many fastening applications, play a pivotal role in ensuring joint stability and longevity. Understanding the intricacies of these washers enhances reliability in various construction and mechanical tasks.
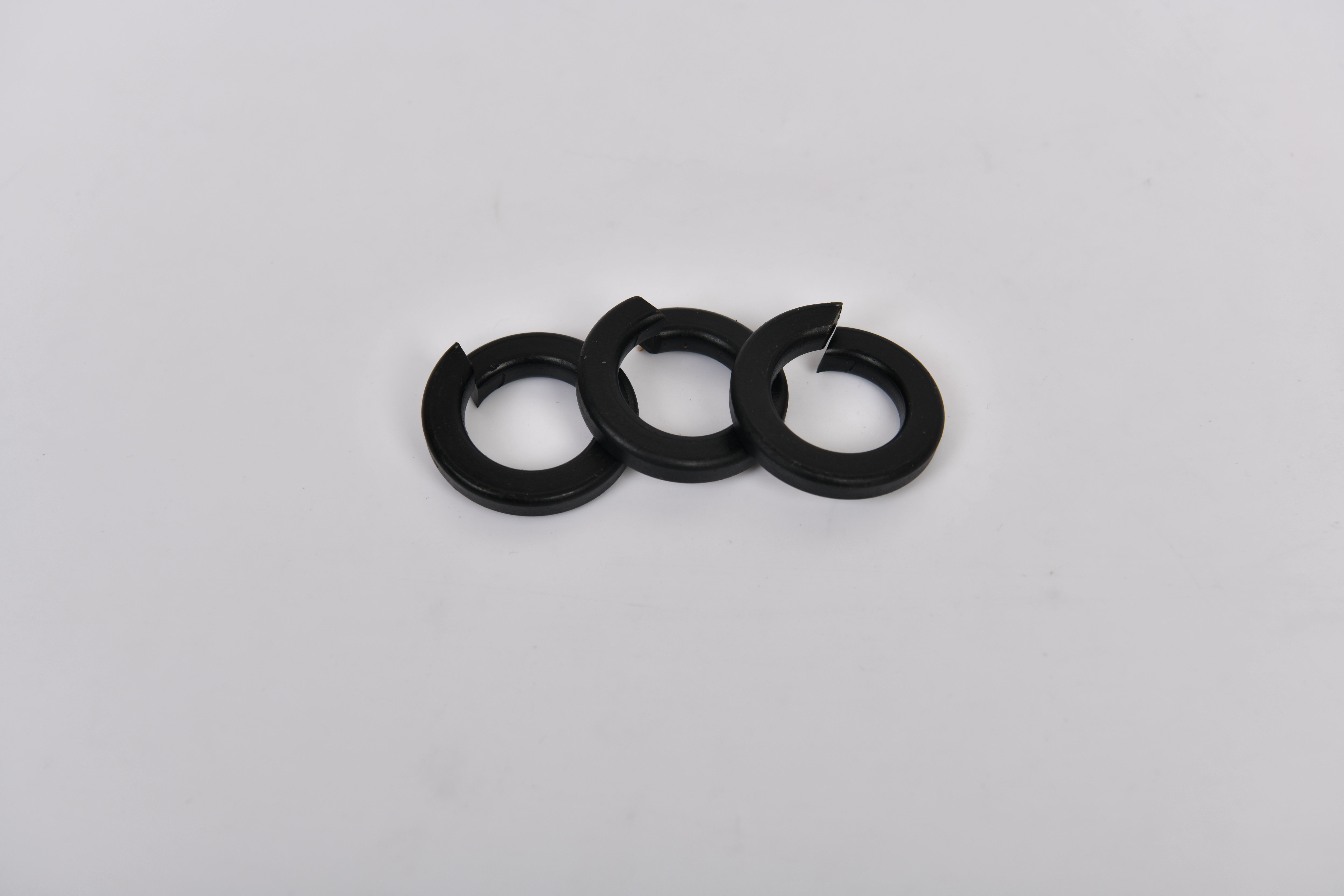
Lock washers are specifically designed to secure fasteners, preventing them from slipping or loosening due to vibration or torque. Among the various types, such as split, tooth, and conical lock washers, each serves a unique purpose depending on the application. For instance, split lock washers appear simple, yet their helical design provides a spring-like action that grips fasteners securely, making them ideal for use in situations subject to constant motion or vibrations.
Flat washers, on the other hand, are more straightforward, offering a smooth surface to distribute the load of a fastener more evenly. They play a fundamental role in minimizing surface pressure and preventing damage to the material being fastened. This even load distribution is essential in delicate applications, from electronics to automotive industries, where excessive pressure can easily compromise materials.
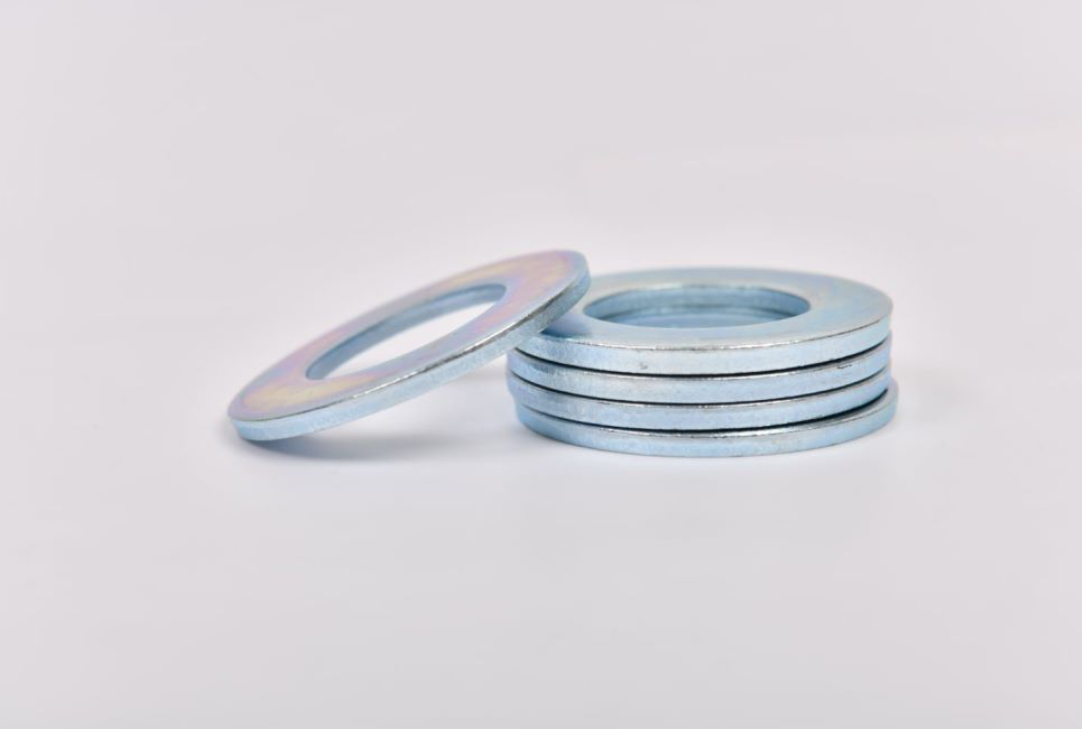
The combination of both lock washers and flat washers is a strategic approach to addressing complex fastening challenges. Utilizing them together maximizes the benefits of each, particularly in scenarios requiring robust security under varying conditions. For example, in automotive applications where parts are often subjected to both heavy loads and constant movement, combining these washers ensures components remain secure against opposing forces.
Incorporating lock washers together with flat washers requires expertise to ensure optimal performance. Understanding the materials involved, the environmental conditions, and the specific requirements of the task are essential in selecting the right washers. For example, in corrosive environments, using washers made of stainless steel or coated with anti-corrosive materials is critical to prevent premature failure.
lock washer with flat washer
Expertise in this domain also extends to understanding the torque specifications for the assembly. Over-tightening can deform lock washers, reducing their effectiveness, while under-tightening might not deliver sufficient clamping force. Precision in applying the correct torque is vital to leverage the full potential of these components.
Authoritativeness in selecting the right washers is evidenced by adherence to industry standards and best practices. Manufacturers often provide detailed guidance on the appropriate sizes and materials for specific applications. Consulting these references ensures the reliability and safety of the assembly, bolstering confidence in the security of the solution.
Building trustworthiness in a technical field like fasteners involves consistent performance and safety assurances. Certified testing and quality assurances from reputable manufacturers can significantly increase confidence. Verifying that the products comply with international standards, such as those from the American National Standards Institute (ANSI) or the International Organization for Standardization (ISO), provides further peace of mind.
Through expert knowledge and practical experience, the combined use of lock washers with flat washers can optimize the integrity and durability of fastened joints. This approach enhances not only the mechanical reliability but also extends the lifespan of the assembly—leading to reduced maintenance costs and improved safety over time. Understanding and implementing these components effectively is essential for professionals seeking excellence in engineering and construction domains.