Choosing between a lock washer and a regular washer may seem trivial to some, yet it's a critical decision that can significantly impact the stability and longevity of mechanical assemblies. With years of expertise in mechanical components, I've garnered substantial insights into their applications and benefits. Let's delve into these insights, taking a close look at how this choice can be optimized for performance.
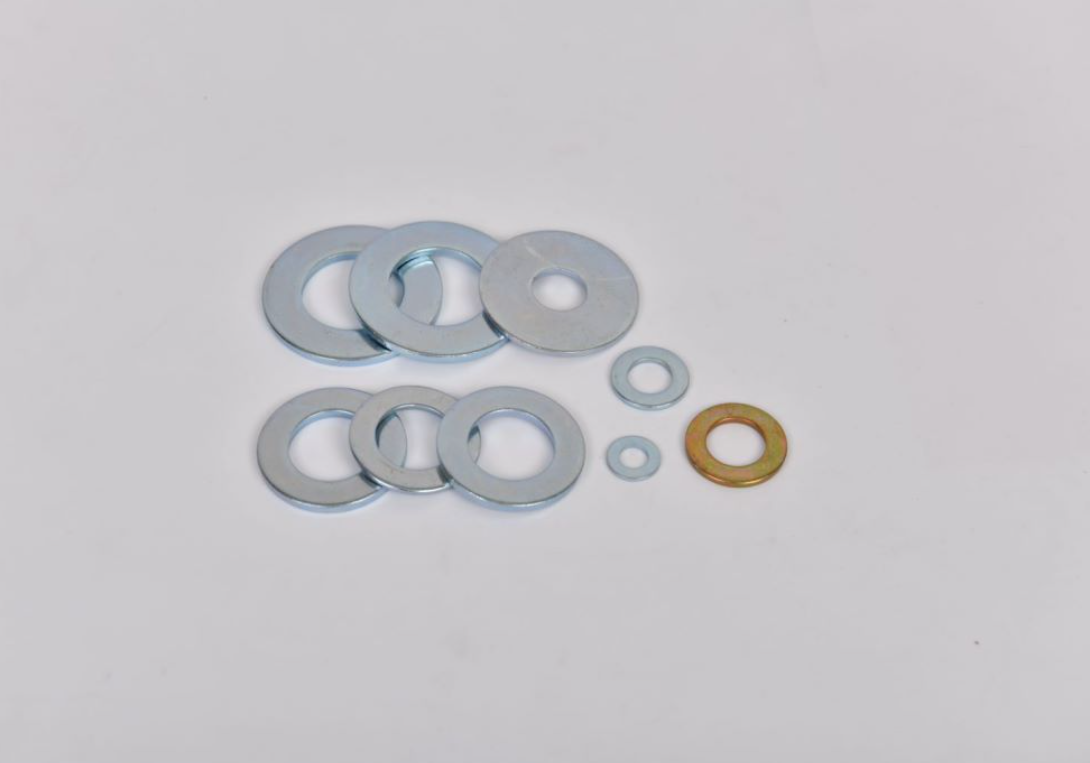
Experience has taught me that the primary function of washers is to distribute the load of the fastener. Regular washers, often known as flat washers, optimize the surface area in contact with the material, reducing the damage that might occur when the fastener is tightened. They're ideal for applications where surfaces are softer or prone to indentation under load, such as aluminum or wood.
On the other hand, lock washers play a critical role in maintaining tension in bolted assemblies, preventing them from loosening due to vibrations and dynamic loads. This function makes them indispensable in automotive and machinery applications where movement or shock is frequent. The expertise gained from using these components underscores their importance in applications where safety and reliability can't be compromised.
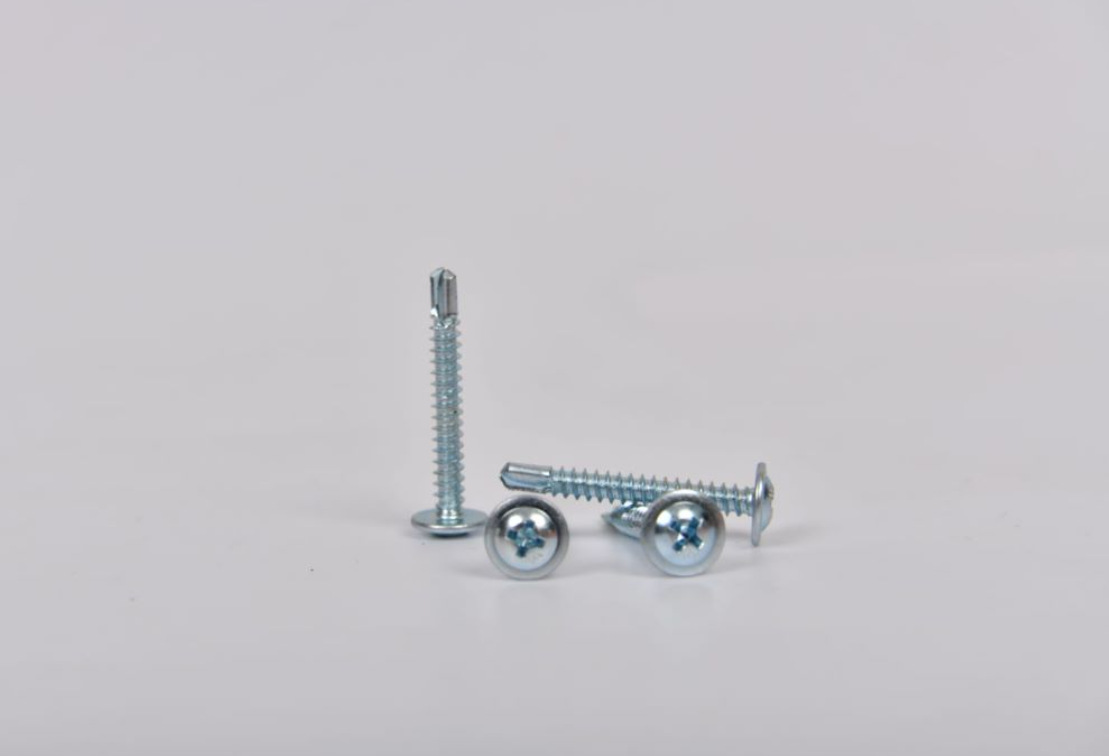
In the realm of expertise, the choice between a lock washer and a regular washer should be influenced by the type of stress the assembly will endure. For static applications with consistent loads, regular washers suffice, providing the necessary buffer between the bolt and the surface. However, for dynamic applications where movement leads to the loosening of fasteners, lock washers become the preferred choice, enhancing the structural integrity by resisting rotational forces.
Authoritativeness in this field comes from understanding the nuances of hardware components. Regular washers vary in thickness and diameter, offering versatility across industries. Yet they lack the ability to prevent loosening. Split lock washers, tooth lock washers, and other variants provide a mechanical advantage, gripping tighter as the bolt is tightened, which is critical in environments with constant vibrations like engines and turbines.
lock washer or washer first
Considering trustworthiness, it’s pivotal to select high-quality materials that correspond to the application’s demands. Stainless steel and alloy steel washers offer exceptional corrosion resistance and tensile strength. Such materials ensure that both lock and regular washers effectively perform their intended roles without premature wear, a testament to durability and reliability.
When evaluating whether to use a lock washer or a regular washer first on a bolt, the sequence often depends on the desired outcome. Typically, the lock washer only ensures its functionality when positioned directly under the nut or bolt head to counteract rotational movement. Hence, the conventional wisdom is to place the flat washer first, followed by the lock washer. This order allows the lock washer to fulfill its role without compromising the load distribution provided by the flat washer.
Ultimately, making the right choice between a lock washer and a regular washer demands a deeper understanding of application-specific stresses and how different washer types address these needs. This decision influences the lifespan and reliability of the assembly, reflecting the importance of informed choices in mechanical design.
In conclusion, the critical decision of whether to opt for a lock washer or a regular washer first requires careful consideration based on the mechanical demands of your application. By recognizing each type's unique benefits and limitations, you can enhance the reliability and performance of your assembly, underpinned by an authoritative command of product knowledge.