In the realm of fasteners, both lock washers and flat washers play crucial yet distinct roles in secure assembly design. As seemingly small components, their impact on the performance, safety, and durability of machinery cannot be understated. Understanding the nuanced application of each is vital for any professional engaged in mechanical design or construction.
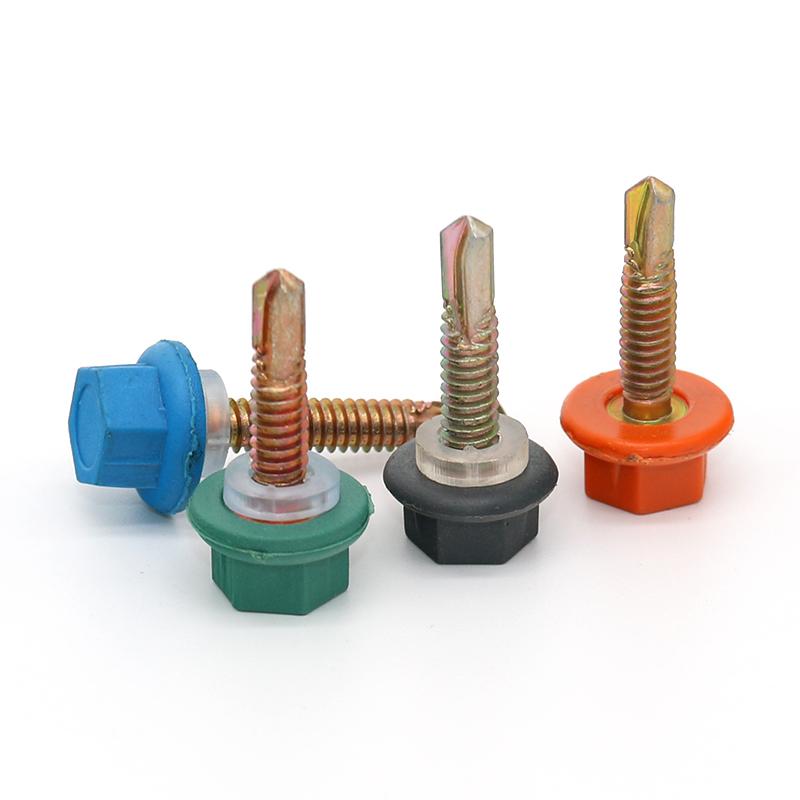
A lock washer is primarily designed to prevent fastening or loosening due to vibration and torque. When applied correctly, it ensures that the bolt or nut it supports remains tight despite the dynamic forces acting upon it. This is particularly relevant in industries such as automotive, aerospace, and heavy machinery, where the integrity of fastened joints is critical to performance and safety.
Lock washers come in several varieties, each suited to different scenarios. Split lock washers, the most common type, feature a helical shape that applies a continuous load and thus resists loosening. Another common type, the toothed lock washer, uses its serrated edges to bite into the surface and further resist rotary movement. Choosing the right type of lock washer involves understanding the environmental conditions of the application, such as temperature, and the specific forces expected to act on the joint.
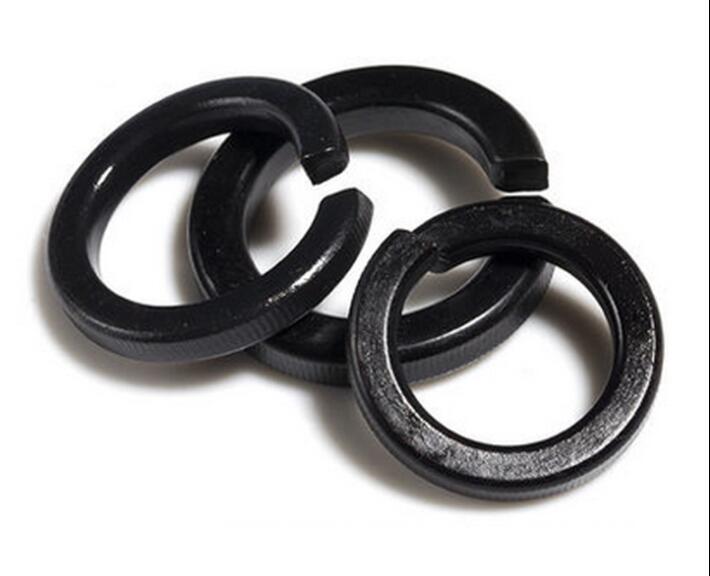
Conversely, flat washers serve a different function by providing a smooth bearing surface for the load-distributing over a larger area, reducing the risk of damage to the fastened surfaces. They're used to distribute loads of threaded bolts and screws, ensuring that the surface material does not become deformed by stress loads. This is especially important in softer materials like wood and plastics or in bonded joints where uneven load distribution could compromise structural integrity.
Moreover, flat washers serve as spacers, helping to ensure that nuts and other threaded fasteners engage fully with the threads of a bolt or screw. In addition to these physical roles, flat washers form a barrier between different materials that might otherwise react negatively together, such as in galvanic corrosion where metals with dissimilar electrochemical properties make contact.
lock washer and flat washer
The synergy between these two types of washers is worth noting. In many applications,
lock washers and flat washers are used in conjunction. The flat washer’s ability to distribute loads complements the lock washer’s anti-loosening functionality, providing an enhanced fastening solution that balances load distribution with mechanical security. This combination is often seen in automotive assemblies and critical structural applications, where reliability and safety are paramount.
When choosing washers for a given application, manufacturers and engineers must consider variables such the material, thickness, and environmental factors. Stainless steel, for example, offers corrosion resistance and is essential in marine or chemical environments, whereas nylon washers might be preferred for their non-conductive properties in electrical applications.
It equally important to source these components from reputable suppliers to ensure adherence to manufacturing standards and material quality. Poor-quality washers might not only fail prematurely but could also compromise the entire assembly, leading to costly repairs, downtime, or even safety hazards.
Selecting the right washer and pairing them appropriately within an assembly requires experience, knowledge of material properties, and an understanding of the application-specific forces. By investing in quality, appropriate washers, engineers ensure that the fasteners in their designs achieve maximum efficiency, safety, and longevity. Being mindful of these elements not only enhances product reliability and customer trust but also aligns with best practices in engineering standards.