Flat washers might seem like simple components in mechanical assemblies, but their role is crucial and often underestimated. They serve multiple purposes, from distributing loads to minimizing vibrations, and their standards ensure reliability and performance across diverse applications. This article delves into the intricate world of flat washer standards, offering insights grounded in real-world experiences and professional expertise, backed by authoritative industry knowledge.
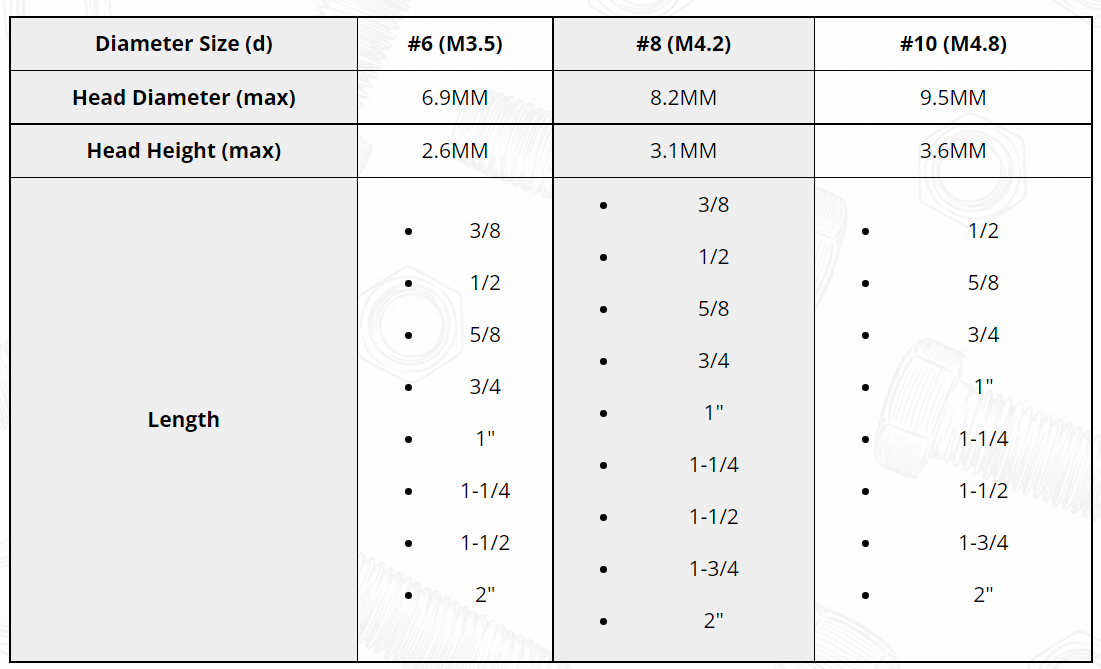
In mechanical design, flat washers are employed to increase the surface area of a fastener's load, thereby reducing the stress on the material being fastened. This seemingly small component can prevent damage to surfaces, which is particularly important in softer materials. The standards governing flat washers ensure uniformity and predictability, which is critical for engineers and manufacturers who rely on these components for safe and effective assembly.
The standards governing flat washers differ globally, each crafted to meet specific industrial needs and expectations. In the United States, the American National Standards Institute (ANSI) and the Society of Automotive Engineers (SAE) have established comprehensive guidelines. ANSI defines flat washers in terms of their physical dimensions and tolerances, while SAE focuses more on the mechanical properties and material types. This dual-focus ensures that washers not only fit but also perform reliably in demanding conditions.
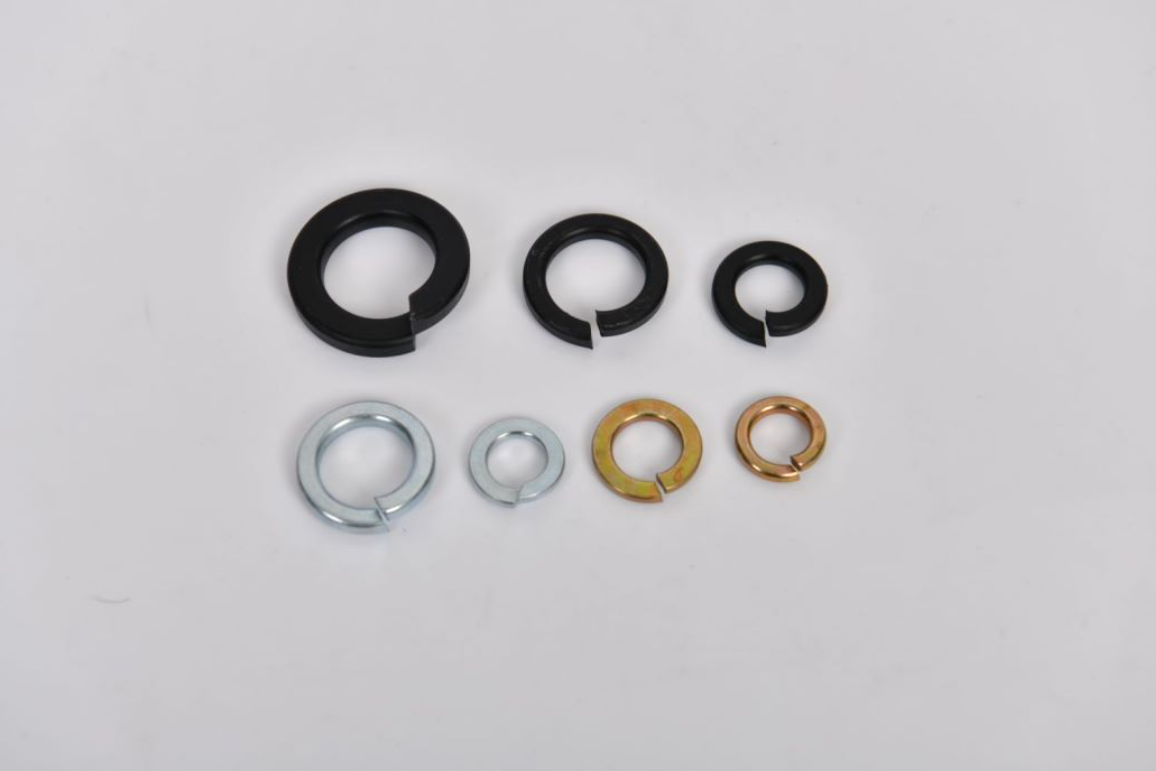
In Europe, the International Organization for Standardization (ISO) provides similar guidelines. ISO 7089, for instance, specifies the dimensions of plain washers for metric applications, ensuring compatibility across international borders. This global synchronization is critical in today's interconnected market, where components may be manufactured in one country and assembled in another.
These standards are not just bureaucratic red tape; they are the backbone of quality and trust in engineering. For example, an aerospace engineer shared their reliance on standardized flat washers to maintain precision in high-stakes applications. With lives on the line, each washer must perform to exact specifications without fail.
The rigor of standards provides their stamp of assurance.
flat washer standards
Moreover, the material composition of flat washers is a vital consideration that standards address in detail. Stainless steel, brass, and alloy steel are common choices, each offering unique benefits. Stainless steel, known for its corrosion resistance, is preferable in marine environments. In contrast, alloy steel washers, recognized for their strength, are often used in heavy-duty industrial equipment.
In a construction scenario, for instance, a civil engineer underscored the importance of selecting the right type of material specified in standards to prevent structural failures. When constructing a skyscraper, even a minor flaw in a fastener's washer can escalate to significant safety risks. Adhering to standards thus mitigates such risks, ensuring buildings stand the test of time and elements.
The reliability of flat washers is also enhanced through rigorous testing protocols detailed in their respective standards. These tests evaluate factors such as tensile strength, hardness, and corrosion resistance. An expert manufacturing manager from the automotive industry highlighted how standardized testing allowed their company to reduce warranty claims by ensuring only high-quality washers were used during assembly. This thorough vetting process builds trust with consumers and industry peers alike.
Furthermore, environmental considerations are becoming increasingly relevant, and washer standards are evolving accordingly. The shift towards greener industry practices is reflected in the development of standards that encourage the use of recycled materials and more sustainable manufacturing processes. This progressive approach not only aids in environmental conservation but also aligns with global sustainability goals, adding an ethical dimension to the authority of washer standards.
In conclusion, flat washer standards are indispensable for ensuring the safety, efficiency, and interoperability of modern machinery and construction. They provide a framework that defines the quality and performance parameters of washers, fostering trust and reliability. From material selection to dimensional accuracy and testing protocols, these standards offer a comprehensive guideline that helps industries maintain consistency and excellence. This authoritative framework not only guides engineers and manufacturers but reassures consumers, supporting the seamless evolution of industrial practices in an increasingly complex world. By embracing these standards, industries not only safeguard their operations but also contribute to a legacy of quality and innovation.