Exploring the Intricacies of Flat Cut Washers A Comprehensive Guide
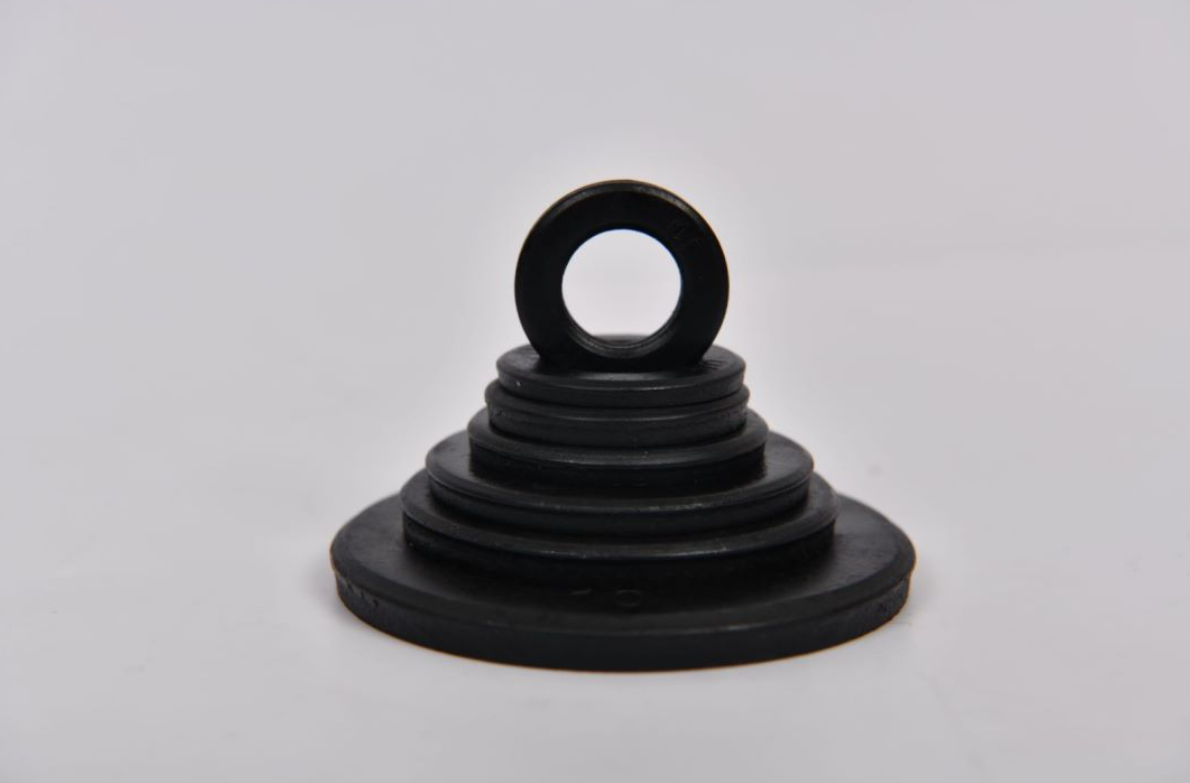
Flat cut washers, often overshadowed by their more complex counterparts in the world of fasteners, play a pivotal role in ensuring the longevity and functionality of countless mechanical assemblies. These unassuming components are crucial in distributing load, preventing galvanic corrosion, and protecting the surface of joined materials. Understanding the nuances of flat cut washers not only enhances mechanical integrity but also boosts efficiency and maintenance.
1. Understanding Flat Cut Washers
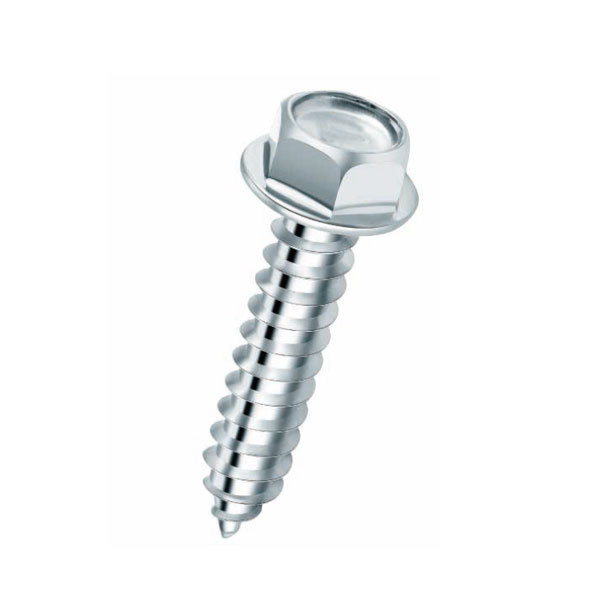
Flat cut washers are typically circular metal discs with a central hole designed to accommodate bolts or screws. Their primary function is to spread the fastener's load over a larger surface area, minimizing the risk of damage to the material into which the screw or bolt is driven. This component is fundamental in assemblies where preserving material integrity is crucial, especially in lightweight or soft materials such as aluminum or plastic.
2. Variants and Materials
Though the basic design of flat cut washers is fairly uniform, variations exist in terms of size, thickness, and material. Materials range from stainless steel and brass to plastic, each bringing its unique benefits. Stainless steel washers, for instance, offer exceptional corrosion resistance, making them ideal for outdoor or maritime applications. Plastic washers, on the other hand, provide electrical insulation and are chosen for their non-conductive properties in electrical assemblies.
3. Key Benefits of Flat Cut Washers
Flat cut washers are indispensable due to their diverse benefits, including
- Load Distribution By spreading the load, these washers protect bolt heads and nuts from embedding into the material, thus preventing structural damage.
- Surface Protection They act as a buffer, protecting the surfaces from scratches, dents, or other forms of damage during tightening.
- Vibration Damping In machinery or equipment where vibration is a concern, flat washers help in absorbing vibrations, preventing them from loosening or damaging the fasteners.
- Sealing Functionality Some washers, especially those made from softer materials, can function as seals to prevent fluid or air leakage.
flat cut washer
4. Installation and Best Practices
Proper installation of flat cut washers ensures maximum efficiency. When installing, ensure the washer lies flat against the surface with even pressure applied during fastening. Misalignment can lead to uneven load distribution and eventual failure of the assembly. It's also essential to match the washer's material and size with the specific requirements of the application to maximize lifespan and performance.
5. The Role of Flat Cut Washers in Industry
In sectors ranging from automotive manufacturing to electronics, flat cut washers find myriad applications. Their role in preventing galvanic corrosion is particularly crucial in aerospace and maritime industries where dissimilar metal contacts could lead to corrosion. In electrical applications, non-metal flat washers are preferred for their insulating properties.
6. Innovations and Trends
As technology progresses, so too does the design and functionality of flat cut washers. Recent innovations include coatings that enhance corrosion resistance and materials developed for specific environmental conditions, such as high temperatures or acidic atmospheres. Moreover, advancements in manufacturing are seeing the production of ultra-thin, high-strength washers that meet the rigorous demands of modern engineering.
7.
Conclusion
Flat cut washers, though simple in design, are sophisticated in function. Their ability to distribute load, protect surfaces, and prevent corrosion makes them indispensable in any assembly process. As industries evolve, the humble flat washer continues to prove its worth, adapting to new challenges with innovative solutions. For those in engineering and manufacturing, understanding and utilizing the full potential of these washers will lead to more reliable and enduring structures. This dedication to quality not only reflects expertise but also instills trust and authority in the production processes that rely on them.