The Efficiency and Precision of Custom M10 Self-Tapping Screws
In the realm of mechanical fastening, custom M10 self-tapping screws stand out for their efficiency and precision. These specialized screws are designed to create their own thread as they are driven into materials, eliminating the need for pre-drilling or tapping holes. This not only speeds up assembly processes but also ensures a secure fit that can withstand significant forces.
Custom M10 self-tapping screws come in various materials and finishes, catering to diverse application needs. Stainless steel is a popular choice for its corrosion resistance and strength, making it ideal for outdoor or marine environments. Zinc-plated versions offer improved rust prevention and are suitable for moderately harsh conditions. For high-temperature applications, titanium screws provide excellent heat resistance and strength without adding much weight.
The design of these screws is optimized for specific tasks. The M10 designation refers to the screw's major diameter, which is approximately 10 millimeters, and is a commonly used size that balances strength and ease of installation. The self-tapping feature is achieved through a specially formed thread at the tip of the screw, which cuts into the material as it is inserted, creating an internal thread that matches the screw's thread pattern. This threading action allows for quick installation while maintaining a tight grip on the material.
Applications for custom M10 self-tapping screws range from automotive and aerospace to construction and furniture assembly
Applications for custom M10 self-tapping screws range from automotive and aerospace to construction and furniture assembly
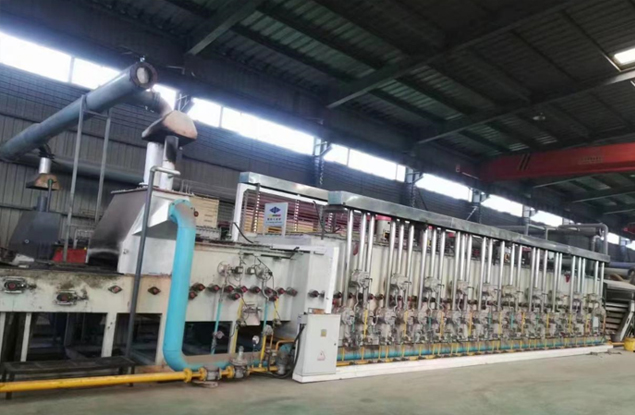
Applications for custom M10 self-tapping screws range from automotive and aerospace to construction and furniture assembly
Applications for custom M10 self-tapping screws range from automotive and aerospace to construction and furniture assembly
custom m10 self tapping screw. In automotive engineering, they might secure components within the engine bay, where high temperatures and vibrations are common. Aerospace engineers may use them in the interior fittings of aircraft, where lightweight and durable fasteners are crucial. In construction projects, these screws can be used to attach electrical boxes or hangers with minimal effort and maximum security. Furniture makers appreciate them for streamlining the assembly process, reducing production time without sacrificing stability or aesthetics.
Manufacturers can tailor these screws to meet specific requirements by adjusting the thread pitch, length, head style, and drive type. A finer thread pitch may be requested for more precise control during insertion, whereas a coarser thread pitch could be chosen for quicker installation in softer materials. The screw heads can vary from hexagonal to round, depending on the tooling available and the torque required during installation.
In conclusion, custom M10 self-tapping screws represent a pinnacle of convenience and reliability in modern fastening solutions. Their ability to quickly create a secure thread in various materials makes them indispensable across industries. By carefully selecting the right material, thread configuration, and head style, users can optimize their assembly processes, ensuring both speed and durability in their projects.