Countersunk head self-tapping screws have carved a niche in both professional and DIY projects, renowned for their discreet yet powerful fastening capabilities. These screws are pivotal when a smooth surface finish is imperative, as their design allows them to sit flush with or below the surface — a crucial feature for applications demanding aesthetics alongside function.
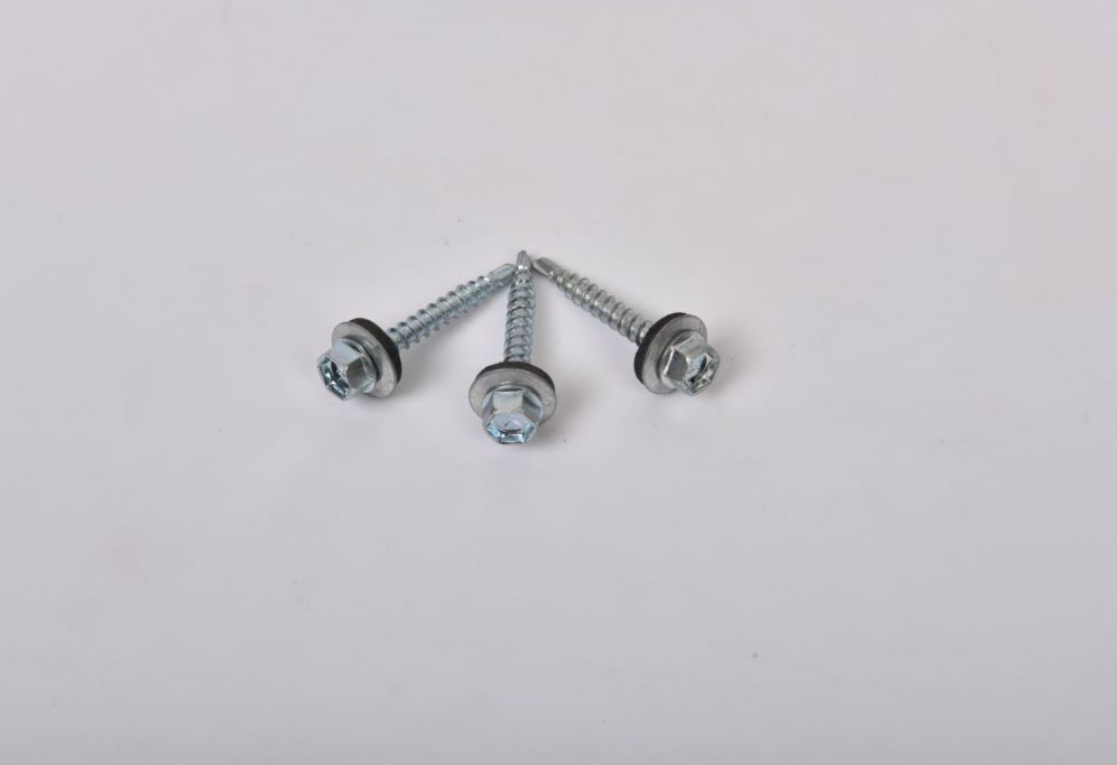
Understanding the essence and application of these screws starts with their structural design. The countersunk head is engineered for a streamlined appearance and seamless integration into materials. Such design attributes uphold both aesthetic and functional elements, reducing snagging and enhancing the product's structural integrity. The self-tapping nature further simplifies the process by negating the need for pre-drilling, thus offering a significant advantage in terms of efficiency and time-saving.
From an experiential perspective, using countersunk head self-tapping screws in projects delivers an unparalleled level of satisfaction, especially in woodworking, metalworking, and plastic assembly. The tactile feedback when engaging the screw into the material offers a sense of reliability and precision. Unlike traditional screws, whose heads remain visible and often lead to potential misalignments, countersunk versions provide reassurance that the finished product will maintain its intended sleek profile.
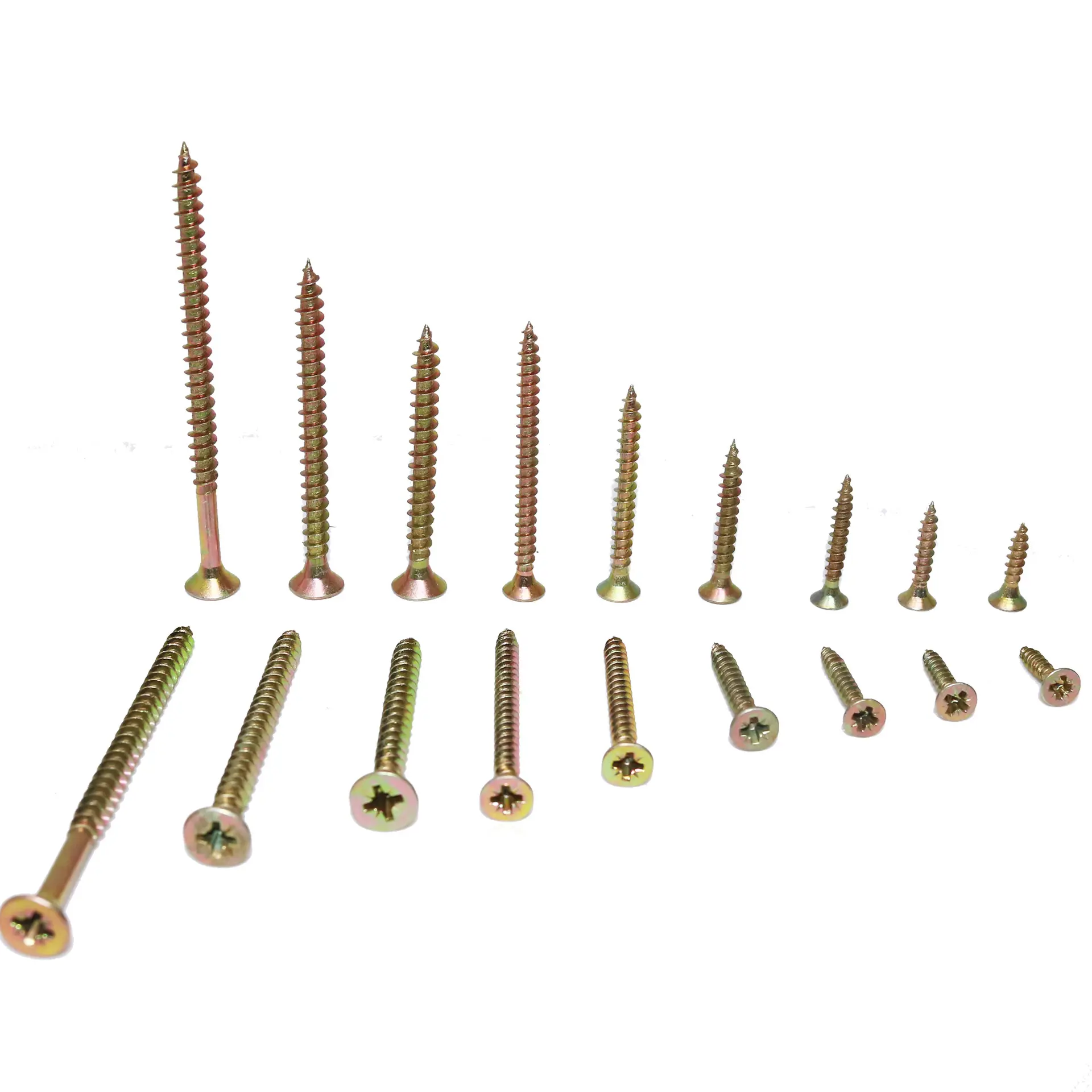
Professionally, the choice of material for these screws should align with the project requirements. They're commonly available in stainless steel, brass, and carbon steel, each serving specific needs. Stainless steel variants, for instance, are ideal for environments susceptible to corrosion, providing durability and longevity. Knowledge of these material properties enhances expertise in selecting the right screw type for various industrial applications, ensuring optimal performance and resilience.
countersunk head self tapping screw
Delving deeper into the mechanics, a countersunk head screw's ability to cut into the substrate without requiring a pilot hole stems from its sharper, self-threading tip. Engineers and construction professionals recognize this feature as a game-changer, permitting not only cost reduction on labor but also minimizing the wear and tear of tools. This reflects the authority and trust these screws command within the construction sector as reliable, robust, and economical fasteners.
The market trust in countersunk head self-tapping screws underscores their engineering excellence. Manufacturers adhere to stringent standards, like ISO and DIN specifications, ensuring consistency in quality and performance. These screws are subjected to rigorous testing — from tensile strength to resistance against environmental factors — fortifying user trust in their widespread industrial application.
Real-world testimonies emphasize the transformative impact of these screws on projects. Users routinely highlight how these screws have simplified assembly processes, reduced material costs, and improved structural integrity. Such endorsements further elevate the trustworthiness associated with these screws and testify to their indispensable role in modern manufacturing and construction practices.
In summary, the countersunk head self-tapping screw stands as a testament to innovative design merging with practical efficiency. Its impact on various industries continues to grow as understanding and technology improve, ensuring this component remains a staple in the quest for excellence in fastening solutions. Whether driven by the quest for a flawless finish or the need for cost-effective and efficient assembly, these screws provide unparalleled utility and credibility, fortifying their place as a cornerstone in the art and science of modern construction and design.