Concave spring washers, also known as Belleville washers or disc springs, are pivotal components in the realm of industrial fastening solutions. These uniquely designed washers are distinguished by their conical shape, which provides the necessary tension to prevent loosening and maintain the clamping force of bolted assemblies. Their application spans across various sectors, including automotive, aerospace, and heavy machinery, making them an indispensable element in engineering fields.
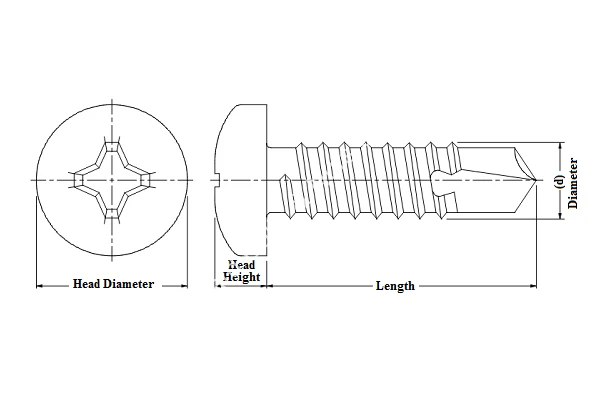
The primary advantage of concave spring washers lies in their ability to maintain a consistent load in mechanical assemblies subjected to vibrations, thermal contractions, and expansions. This functional reliability is particularly emphasized in environments where mechanical stability is crucial, such as in aerospace technology where even the smallest structural failure can have catastrophic consequences. Industries demand washers that offer reliability, and concave spring washers meet this demand with superior performance.
Understanding the material composition and design specifications of these washers is essential for ensuring optimal performance in specific applications. Commonly crafted from high-strength steel or stainless steel, these materials are selected for their ability to withstand high-stress conditions without deforming. Their conical shape permits these washers to operate effectively under high load capacities, providing stability and uniform load distribution over a wide range of operating conditions. This versatility makes them suitable for customizable solutions, ensuring that they align with specific engineering standards and project requirements.
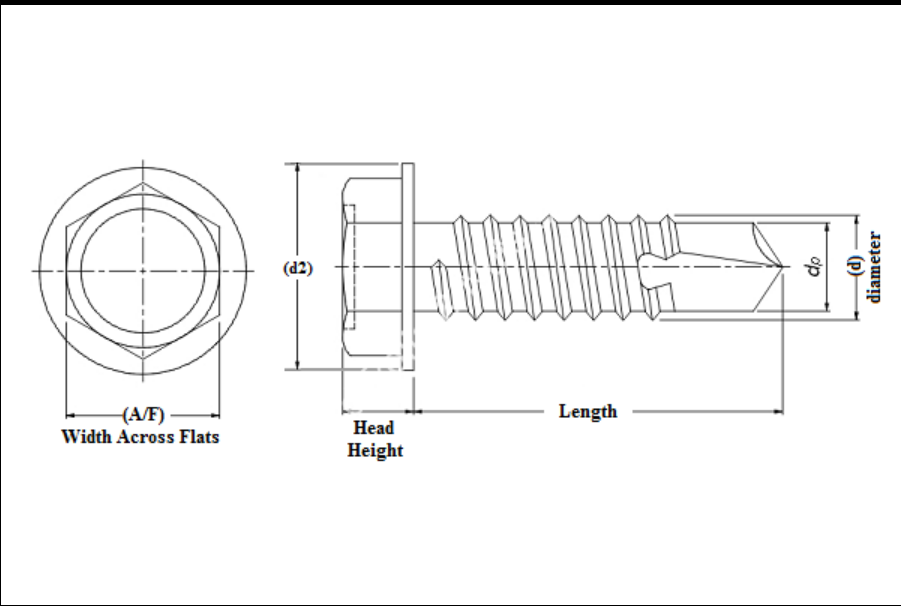
In terms of expertise, the manufacturing process of concave spring washers demands precision engineering to ensure exact conformity to design specifications. Rigorous testing and quality assurance processes are in place to certify that each washer can endure the specific stresses of intended applications. The precision involved in manufacturing these washers underscores their role as a trusted component across numerous industrial applications, illustrating the expertise integral to their production.
From an authoritativeness and trustworthiness perspective, manufacturers of concave spring washers must adhere to stringent international standards and certifications, such as those provided by the International Organization for Standardization (ISO) and the American Society for Testing and Materials (ASTM). These standards ensure that the washers maintain their geometric specifications and mechanical properties under operational loads, enhancing their reliability and the safety of the applications they support. Compliance with these standards is a testament to the manufacturer's commitment to quality and performance, instilling confidence among engineers and procurement specialists regarding the integrity of their designs.
concave spring washer
Investments in research and development have further advanced the understanding of how these washers can be optimized for better performance. Innovations include surface treatments and coatings that enhance corrosion resistance and extend the washers’ lifespan in harsh environments. The continuous evolution in manufacturing techniques reflects a commitment to enhancing the foundational principles of trustworthiness and performance upon which these washers are built.
In practice, the deployment of concave spring washers translates into extended maintenance intervals and reduced operational downtime, as their design inherently compensates for thermal expansion and contraction cycles, unlike conventional flat washers. Their ability to maintain joint integrity in dynamic conditions minimizes the risk of mechanical failure, thereby endorsing their reputability in industrial design.
With the rise of Industry 4.0, the integration of advanced monitoring systems with traditional components like concave spring washers represents a future where predictive maintenance could be seamlessly executed. This proactive approach not only supports sustainability by maximizing component lifecycle but also enhances operational efficiency, resonating with the evolving expectations from modern industrial frameworks.
Concave spring washers embody a balance of engineering excellence, reliability, and technical innovation, affirming their status as a critical element in bolted assemblies. Their role is continuously evolving, aligned with progressive advancements in engineering practices, reflective of the industry's ongoing quest for superior solutions tailored to meet complex operational demands.