Self-tapping screws are an essential component in various industries due to their unique ability to drill their own holes as they are driven into materials. This characteristic makes them invaluable for both DIY enthusiasts and professionals. With a variety of options on the market, the quest to select the perfect self-tapping screw can be daunting. Here's a comprehensive guide to understanding the six primary types of self-tapping screws and their optimal applications, ensuring that your next project is executed with precision and expertise.

For starters, it's crucial to understand the distinction between self-tapping and self-drilling screws. While both can drill into materials, self-drilling screws come with a drill bit-like tip that can penetrate metal without a pilot hole, unlike self-tapping screws, which may require a pilot hole depending on the material.
1. Countersunk Self-Tapping Screws These are designed for a flush finish, where the screw head sits flat against the material's surface. Commonly used in woodwork and furniture assembly, they provide a neat appearance and prevent snagging on fabrics or skin. Experience shows that utilizing a countersunk screw can enhance the structural integrity of wooden joints by distributing force evenly across the surface.
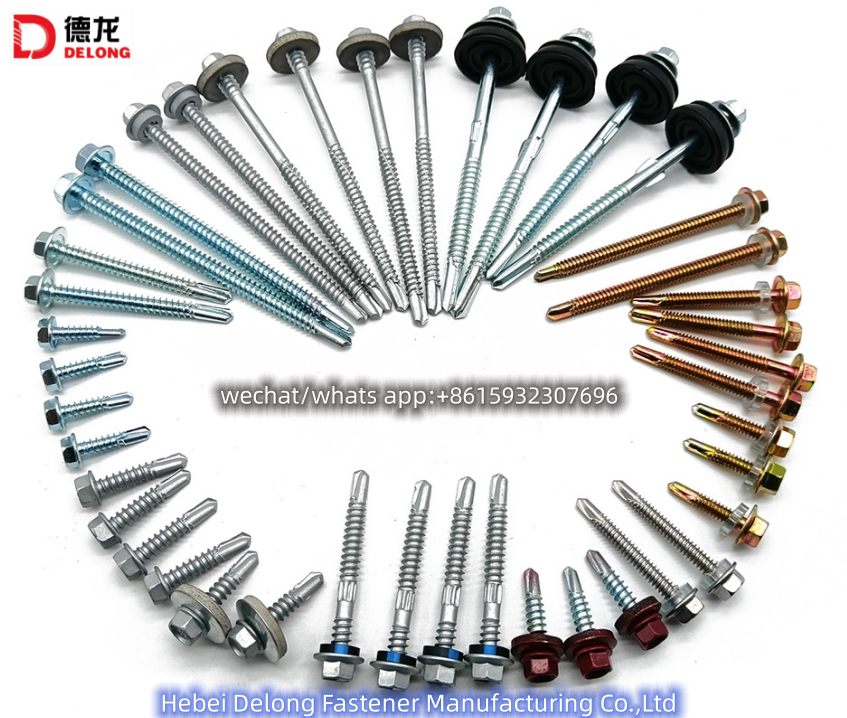
2. Pan Head Self-Tapping Screws These screws have a slightly rounded head, allowing them to sit on the material's surface. Ideal for metal-to-metal fastening, the pan head design provides a larger surface area under the head, ensuring a secure grip. Their expertise lies in providing excellent torque capabilities without over-tightening, a crucial aspect when working with delicate materials.
3. Round Head Self-Tapping Screws Featuring a domed head that extends above the surface, these screws are perfect for applications requiring a distinctive aesthetic, such as decorative hardware fittings. Professionals trust round head screws for joining thin metals and plastics, where the additional head height can accommodate washers, enhancing load distribution.
4. Hex Head Self-Tapping Screws Known for their robustness, hex head screws are frequently employed in heavy-duty applications like steel constructions and structural fixings. Their authoritative design provides maximum grip and torque transfer, essential for projects demanding high holding power and reliability under stress.
6 self tapping screw
5. Flat Head Self-Tapping Screws Similar to countersunk screws, these are designed for materials where a smooth finish is desirable. The flat head ensures minimal protrusion, offering both aesthetic appeal and safety. Flat head screws are trusted in cabinetry and paneling, where the finest details can distinguish quality craftsmanship.
6. Oval Head Self-Tapping Screws These screws offer a combination of flat and pan head designs, providing an elegant finish with a slight dome. They are widely appreciated in boat manufacturing and automotive sectors, where water-resistant and aesthetically pleasing fastenings are required. Their trustworthiness in creating watertight seals makes them indispensable in industries where exposure to elements is a concern.
When selecting self-tapping screws, material compatibility is vital. For instance, stainless steel screws are preferable for corrosion resistance, especially in marine or outdoor environments. Furthermore, the screw thread's design can significantly impact drilling efficiency and holding capacity. Coarse threads are typically better for soft materials like wood, while fine threads provide superior grip in harder materials like metal.
Moreover, tool compatibility is a critical consideration. While handheld screwdrivers offer control in delicate projects, electric or pneumatic tools enhance efficiency and consistency for larger-scale tasks. Understanding the correct application of tools alongside your choice of self-tapping screws can elevate your project's success.
In conclusion, the right self-tapping screw can transform the outcome of your project. By considering factors such as head design, compatibility, and material, you can achieve both functionality and aesthetics. Trust in your expertise, rely on authoritative sources for your materials, and let experience guide your tool selection. With this knowledge in hand, you're well-equipped to tackle any assembly challenge with confidence and precision.