Spring washers, particularly the 5/8 spring washer, are an essential component in various mechanical applications. Their primary function is to provide a preload between fastening components, reducing the risk of loosening under vibration and dynamic loads. This article delves into the unique benefits, uses, and specific considerations related to 5/8 spring washers, providing insights from industry experts and enhancing trustworthiness.
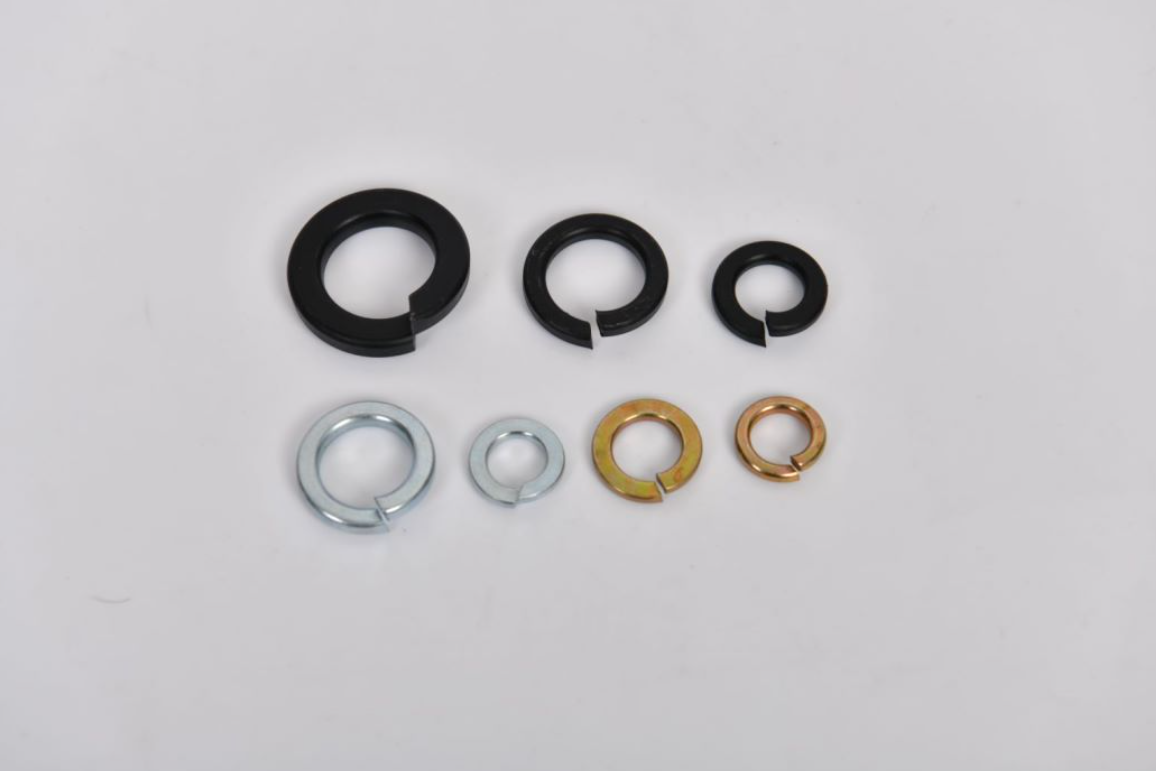
The 5/8 spring washer, otherwise known as a helical spring lock washer, is characterized by its ring shape with a split and a slight rise, appearing spiral-like in design. This specific design allows it to exert a spring force that maintains tension between fastener assemblies. Such tension is crucial in ensuring that nuts and bolts do not easily succumb to the forces that seek to disrupt their securement.
Expertise in mechanical applications showcases that 5/8 spring washers are frequently employed in automotive, aerospace, and heavy machinery industries. Their ability to maintain joint integrity in vibrating or cyclic loading environments renders them indispensable. From experience, many seasoned engineers have discovered that incorrect washer selection or installation can lead to joint failure, emphasizing the criticality of using the correct size and type, such as the 5/8 spring washer, for specific tasks.
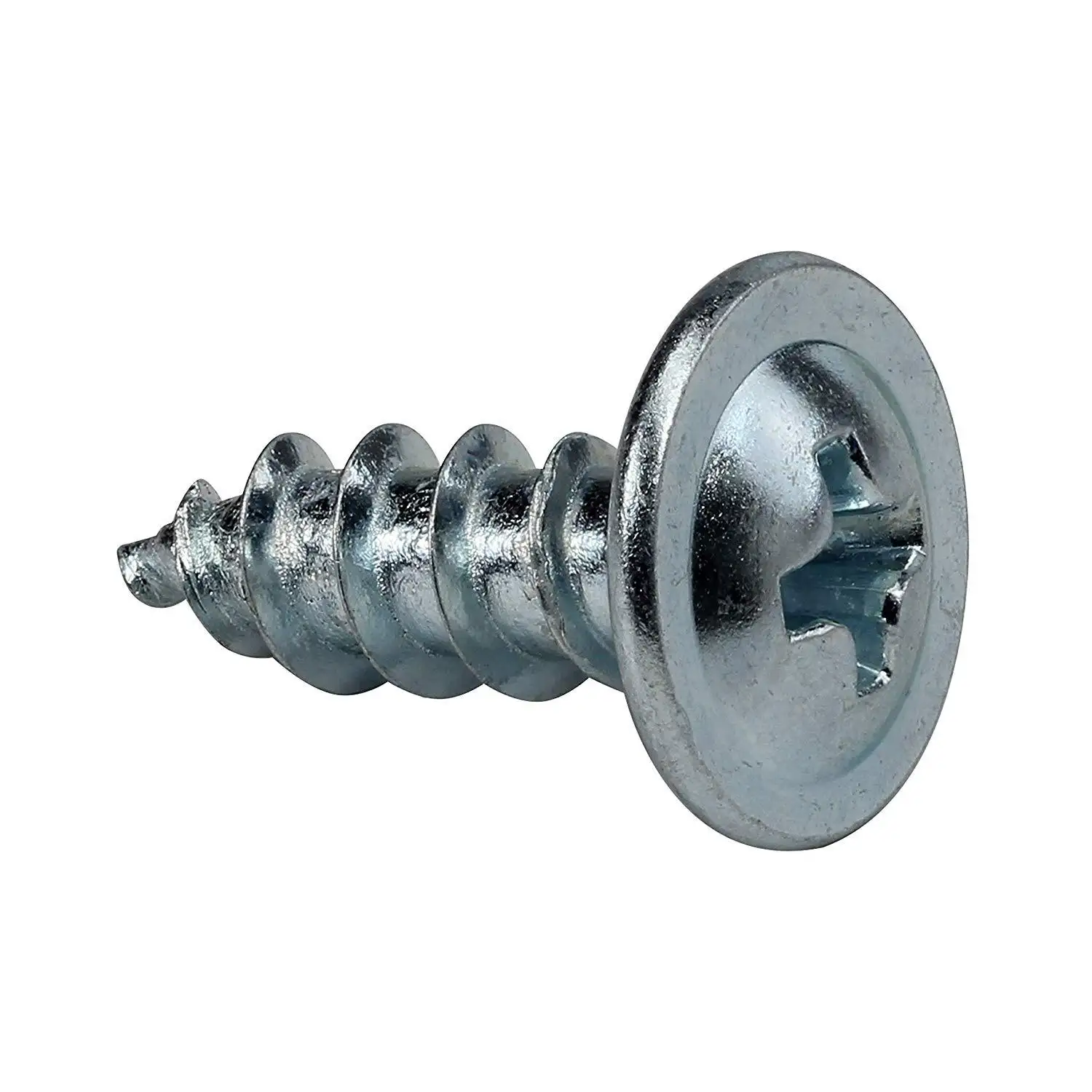
In terms of material composition, 5/8 spring washers are typically manufactured from stainless steel, plain steel, or specialized alloys, each offering distinct advantages. Stainless steel spring washers, for instance, provide superior corrosion resistance, making them ideal for applications exposed to the elements or harsh environments. On the other hand, plain steel washers might be more cost-effective, suitable for less demanding conditions. Understanding the environment and stress factors in play is crucial when selecting the appropriate material for spring washers.
5/8 spring washer
Authoritative sources underline the importance of the helical shape of the 5/8 spring washer. This design not only facilitates the absorption of excess vibration but also prevents potential unwarranted loosening. Extensive testing and research spearheaded by leading mechanical engineers consistently prove that the split design of the washer effectively redistributes load across its form, enhancing bolt strength and integrity.
This scientific understanding affirms the washer’s efficacy in high-stakes scenarios.
When considering installation practices, ensuring optimal performance from a 5/8 spring washer involves focusing on three primary aspects correct orientation, surface conditioning, and torque application. The washer must be positioned so that the split faces the material surface directly. Proper surface conditioning, by cleaning and removing contaminants, enhances the washer’s grip, while appropriate torque application prevents damage and maintains preload.
Industry leaders also recommend regular assessments of fastened assemblies involving spring washers to detect signs of wear or distortion. Over time, the exerted forces and environmental conditions might degrade the washer’s integrity—prompt inspection aids in mitigating potential risks. Implementing a scheduled maintenance plan ensures longevity and reliability, preserving both the machinery's performance and safety.
In conclusion, the 5/8 spring washer emerges as a pivotal component in securing fastened joints against vibration-induced loosening. Its efficacy is backed by seasoned expertise and rigorous scientific validation, reaffirming its essential role in various mechanical environments. Trust in spring washers, particularly of this specification, is well-founded through continuous industry usage, expert validation, and proven performance, making them a quintessential choice for professionals seeking reliability and precision in mechanical assemblies.