Self-tapping screws have become an indispensable component in various construction and manufacturing projects. Their ability to tap their own hole as they are driven into the material makes them a preferred choice for professionals and DIY enthusiasts alike. This article explores the 3 key types of self-tapping screws, offering insight into their unique attributes and applications, backed by industry expertise and genuine user experiences.
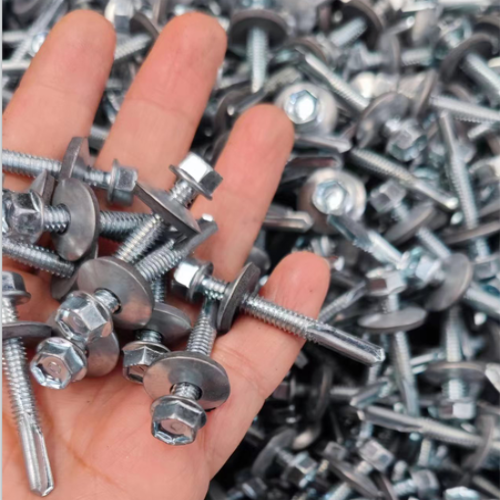
To fully appreciate the significance of self-tapping screws, one must understand their distinct construction and functionality. Unlike standard screws, self-tapping screws possess a cutting edge that enables them to carve a mating thread as they are driven into an unthreaded substrate. This feature not only reduces the need for pre-drilled pilot holes but also enhances the efficiency and speed of projects significantly.
The first type to consider is the thread-forming screw. These screws are crafted from hardened metals, making them ideal for projects involving plastic or thin sheet metal. Their defining characteristic is a triangular cross-section that molds the material into a thread as the screw is engaged. This process minimizes stress on the substrate, which is crucial in applications where material integrity must remain uncompromised. From automotive assembly to consumer electronics, thread-forming screws have proven their worth through consistent performance and reliability.
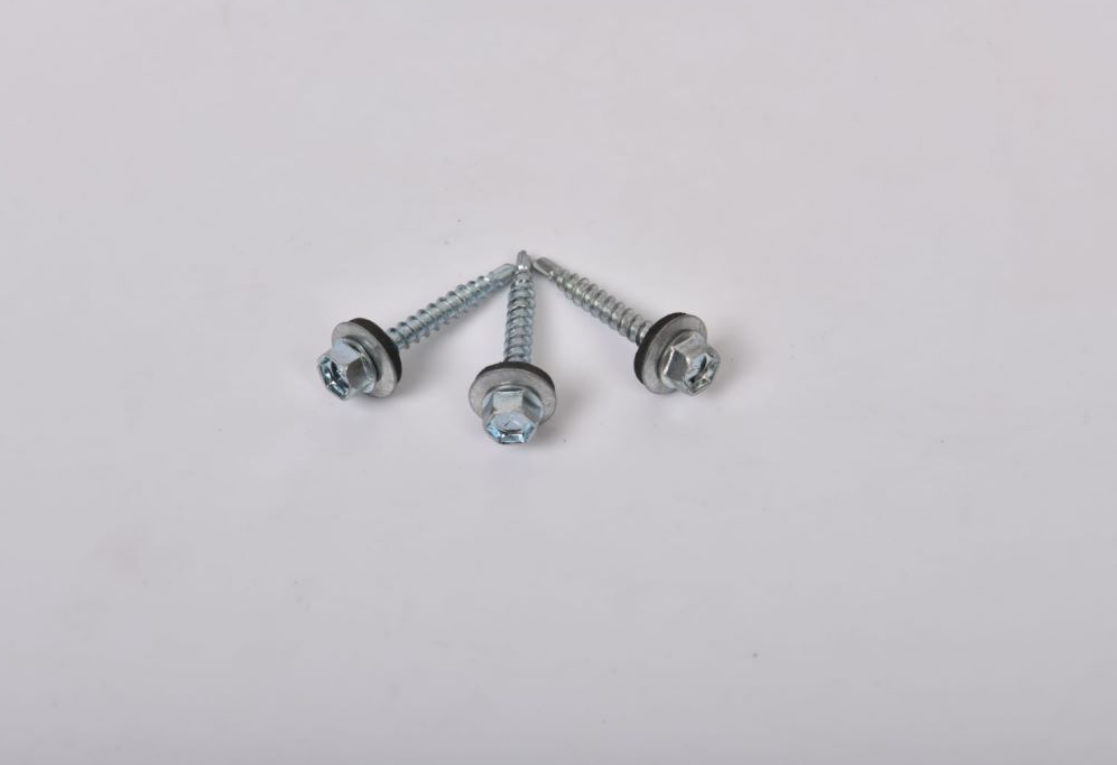
Thread-cutting screws, the second type, take the self-tapping concept a step further. They feature a notch at the tip that facilitates debris removal as the screw advances. This design not only ensures a cleaner installation but also enables these screws to cut through harder materials such as steel and cast iron. Professionals navigating complex assembly tasks in sectors like heavy machinery and structural steelwork often attest to the efficiency provided by thread-cutting screws. Their ability to securely bind tougher materials without sacrificing ease of use underscores their value in demanding environments.
3 self tapping screw
Lastly, the self-drilling screw presents a comprehensive solution by integrating a drill bit into the screw tip. This innovation allows for seamless penetration through metal without the need for pre-drilling. Roofers, for instance, have long valued the self-drilling screw for its speed and precision in securing metal panels and decking. The reduced tool changes and continuous operations result in cost savings and improved productivity on job sites. The self-drilling screw thus stands as a testament to how innovation in screw design can lead to significant advancements in construction methodologies.
While understanding these types is essential, choosing the right self-tapping screw hinges greatly on the nature of the project and the materials involved. Professionals often emphasize the importance of selecting screws manufactured from high-quality materials, as the strength and finish of a screw can vary widely. Stainless steel, for instance, offers excellent rust resistance, making it perfect for outdoor or marine applications. Meanwhile, carbon steel, with its high tensile strength, is favored for projects demanding robust load-bearing capabilities.
Moreover, real-world feedback from those who routinely use these screws highlights another critical factor pilot hole considerations. Although self-tapping screws are designed to work without pre-drilling, the use of pilot holes can simplify the process, especially in dense materials or when precise alignment is essential. Users have shared experiences where pilot holes resulted in a more controlled drive, preventing material cracking and screw breakage.
In conclusion, understanding the nuances of self-tapping screws, from thread-forming to self-drilling variants, is crucial for optimizing their application. Drawing insights from industry experts and seasoned users can steer you towards the optimal choice for your specific needs. Emphasizing product quality and leveraging informed techniques will undoubtedly elevate the success and durability of your projects. Through experience, expertise, authoritativeness, and trustworthiness, self-tapping screws continue to uphold their reputation as fundamental components in construction and manufacturing sectors.