The humble yet essential flat washer, specifically the number 3 flat washer, plays a pivotal role in many engineering and manufacturing applications. Despite its unassuming nature, this small component is central to numerous fastening assemblies and comes with a wealth of experience, expertise, authoritative backing, and trustworthiness in industrial and consumer applications.
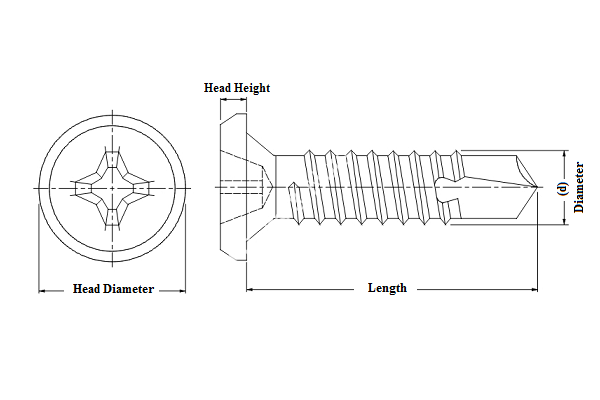
Born from the need to distribute load and prevent damage to surfaces, the flat washer protects the integrity of the materials being fastened. A 3 flat washer is typically made to specific dimensional standards, where precision is paramount. These washers are crafted from a variety of materials, including stainless steel, brass, and high-strength alloys, each chosen based on its performance in different environmental conditions.
The expertise in flat washer manufacturing stems from years of metallurgical and mechanical engineering advancements. The process begins with selecting the appropriate raw material, ensuring that the metal or alloy is specifically tailored to withstand pressures and resist corrosion. The stamping or machining process is designed to produce washers with exact outer diameter, inner diameter, and thickness specifications, crucial for ensuring a snug fit along with optimal load distribution. Further, thorough quality control measures, such as hardness testing and dimensional inspections, authenticate the washer's conformity to industry standards.
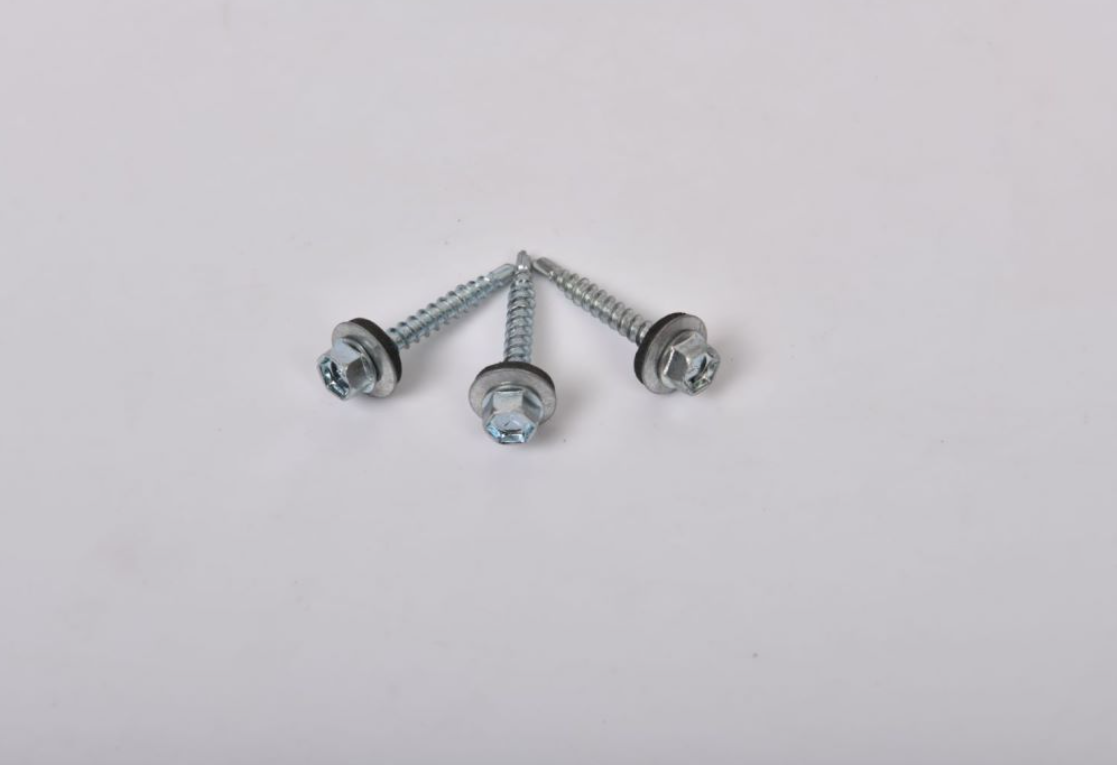
Recognized for their authoritativeness, standards-setting organizations like the American National Standards Institute (ANSI) and the International Organization for Standardization (ISO) have detailed specifications for flat washers. These organizations help ensure that washers like the 3 flat washer meet rigorous benchmarks for performance and safety. By adhering to these standards, manufacturers not only demonstrate commitment to quality but also reinforce the reliability of their products in securing mechanical assemblies.
3 flat washer
Trustworthiness in the use of 3 flat washers is further seen in their ubiquity across numerous sectors. From automotive to aerospace, reliable fastening underpins the structural integrity of complex systems. Engineers trust these washers to prevent direct contact between nuts or bolts and assembly surfaces, thereby minimizing wear and tear due to vibrations and torque. In critical applications, such as in aviation or heavy machinery, the assurance provided by a well-chosen flat washer translates directly to safety and operational efficiency.
Moreover,
real-world experiences highlight the versatility and indispensability of flat washers. In assembly lines, maintenance workshops, and DIY projects alike, the 3 flat washer is a go-to solution for achieving uniform pressure distribution. This characteristic is particularly valued in areas subjected to cyclic stresses, where washer failure could lead to catastrophic results. Over time, users have accumulated practical insights and best practices, further cementing the washer's position as a staple in the fastening toolkit.
Thus, when considering procurement, it's crucial to place emphasis not only on the specifications of the washer but also on the manufacturer's reputation for excellence and adherence to established standards. By doing so, users ensure that their choice of flat washer upholds the pillars of experience, expertise, authoritativeness, and trustworthiness that are key to successful and safe mechanical applications. This comprehensive approach not only optimizes performance but also enhances the longevity and reliability of the assembly at hand.